Surface imaging plays a crucial role in the validity and accuracy of automation processes. Scientists and engineers have relied on surface imaging techniques to study the structure of materials at the nanoscale for many years. The various imaging technologies have different device alterations that have to be substituted to suit the experimental objectives, including the choice of scanning tip in scanning probe microscopy or the ideal camera with adequate frame rates.
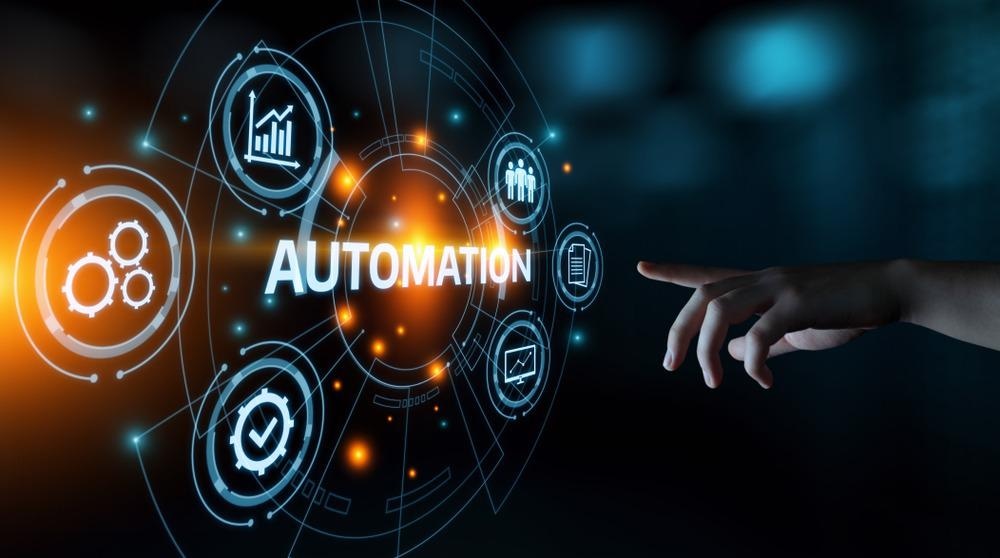
Image Credit: Alexander Supertramp/Shutterstock.com
Wide-scale, fast imaging, important for industrial processes, is still hampered by the complex operation and handling of scanning and imaging technology. Automating the imaging process is critically important in such settings.
The quality of surface imaging is vital in automation. When a surface image is acquired, a two-dimensional (2D) spatial projection is received by the computer to analyze. Surface automation uses 2D surface shots and image recognition techniques to examine the material studied. The particle sizes that make up the topology of the materials have to be precisely distinguished for the results to be accurate.
Automated Imaging Techniques
Automated imaging determines particle size, shape, and other physical properties such as transparency. This method makes it possible to observe particles in detail to reveal the presence of agglomerates and particles with irregular shapes.
Statistically representative size distributions can also be obtained as thousands of surface features are captured in one measurement.
Automated imaging is often used in conjunction with other particle characterization techniques to gain a deeper understanding of the sample or to cross-validate particle and surface feature approximation methods.
Automated imaging techniques use digital cameras to capture 2D images of a dispersed particulate sample. They can be divided into two types: dynamic analysis and static analysis.
In dynamic image analysis, particles flow through the field of view of the camera, so samples such as particles dispersed in water are captured during the movement.
In static image analysis, particles are dispersed on the surface, pictures are taken from stationary particles, then slides with particles are moved to take multiple images, at different positions as shown in figure 1.
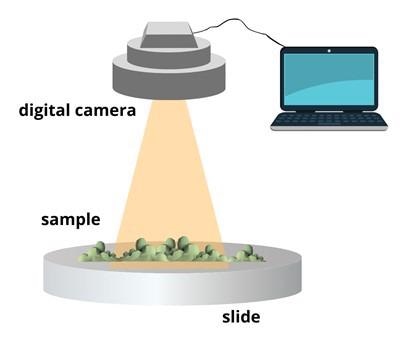
Figure 1: A typical surface imaging setup for automation. Image Credit: Ilamaran Sivarajah
Static imaging systems are more flexible in terms of sample presentation and offer the ability to reanalyze the same particles. While dynamic imaging systems offer advantages in speed of measurement and ease of sample preparation.
Surface imaging for automated analysis consists of four main steps. The first step is sample dispersion. Proper sample dispersion is important to obtain good surface imaging results. The dispersion procedure is optimized according to the material type, particle size, and type of dispersion required for the experiment. The goal is to have enough of the surface structures separated and not grouped together.
The second step is to choose a region of interest within the field of view and magnification. Once a region is established, scanning is initiated. The system scans over the region of interest and captures images of individual structures while maintaining focus and magnification. Dynamic changes and differences in size or shape distribution can be observed during the scan.
Step three is image processing or image thresholding. Image thresholding is a partitioning of an image into a foreground and background. This image analysis technique isolates the structure of interest from the background by converting grayscale images into binary images. The resulting images offer a contrast that is correlated with processing algorithms.
The final step involves results generation. There are some common size parameters that are reported for each structure.
Particle size can be expressed as circle equivalent diameter, which is a diameter of a particle that has the same area as a particle of interest.
Length and width are also used in structural analysis. Aspect ratio and elongation are the most common parameters to describe particle shape. Circularity and solidity show the degree to which the particle is similar to a circle. For example, the further away a particle deviates from a perfectly round smooth circle, the lower the circularity value is.
Advantages and Outlook
Surface imaging offers several advantages for automated analysis. Individual particle size and shape can be resolved. Particle size distribution can be obtained and analyzed for fine particle concentration within the sample structure.
Post-processing software control enables statistical analysis of the dispersion and distribution of variants within the specimens studied. Surface automation is also used to compare and validate other experimental methods such as laser diffraction.
Some areas where image automation can be improved are selective magnification thresholds.
During the imaging process, poor contrast is observed for some structural discrepancies. Certain samples suspended in liquid can also exhibit diffusion at higher magnifications.
References and Further Reading
Alberto Boschetto, Veronica Giordano, Powder sampling and characterization by digital image analysis, Measurement, Volume 45, Issue 5, 2012, Pages 1023-1038, ISSN 0263-2241.
Arvaniti, E.C., Juenger, M.C.G., Bernal, S.A. et al. Determination of particle size, surface area, and shape of supplementary cementitious materials by different techniques. Mater Struct 48, 3687–3701 (2015). https://doi.org/10.1617/s11527-014-0431-3
Shekunov, B.Y., Chattopadhyay, P., Tong, H.H.Y. et al. Particle Size Analysis in Pharmaceutics: Principles, Methods and Applications. Pharm Res 24, 203–227 (2007). https://doi.org/10.1007/s11095-006-9146-7
Disclaimer: The views expressed here are those of the author expressed in their private capacity and do not necessarily represent the views of AZoM.com Limited T/A AZoNetwork the owner and operator of this website. This disclaimer forms part of the Terms and conditions of use of this website.