Sightline has recently had the opportunity to work with a leading producer of poultry products in the US. Utilized by restaurants throughout the country and distributed by major retailers, this company aims to supply products of the highest quality, maximizing its vertically integrated operations through cutting-edge technology.
Skinless, boneless, butterfly chicken breasts prepared in batches of up to 40,000 lb form the basis of some of the company’s most popular products.
In the original process, approximately 200 lb (0.5%) of each batch is sampled to ascertain the size and other observable features through caliper measurement and visual inspection as part of its official incoming acceptance procedures.
The results are noted by hand and are sent to downstream teams to manually input the data into the company’s present quality assurance systems.
Challenge
According to the measurement data gathered by the incoming QA team, the butterfly breasts are moved to the cutting area to be divided into strips, chunks, and fillets after being graded and inspected.
Reliable measurements are vital in enhancing the downstream processes and make exceptional end products that follow the guidelines set out by their own regulatory bodies and customers while preventing needless waste.
The company found that the present method of manual inspection was in danger of inconsistency and subjective observation by various operators. For example, one inspector might apply more pressure to a caliper than another because of the flexible nature of poultry, which produces contradictory measurements for the same piece.
Objectives
To optimize the efficiency and scope of this incoming inspection process, the quality assurance and operations teams at the company highlighted the following aims:
- Increase quality inspection’s reliability and precision.
- Sample a larger quantity of incoming products within the same period.
- Automate the gathering of inspection data in a digital format that is possible to share on current systems.
- Obtain a wider range of measurement and characteristic data in the inspection process.
Sightline Process Controls, Inc. was contracted to succeed in these goals and gage the solutions available for this application. The Sightline BT-300WD, Washdown Benchtop 3D Visual Inspection System was the system found to successfully meet the customer’s requirements.
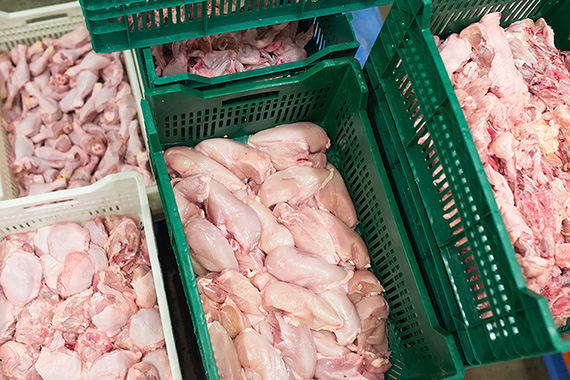
Figure 1. Chicken breast ready for quality inspection and packaging.
Solution
The BT-300WD Washdown Benchtop Measurement System from Sightline was selected because of its 2D/3D vision features, together with its portability and appropriateness for a washdown environment.
A Sightline technician configured and calibrated the BT-300WD and taught the employees how to control the unit, within just one day at the customer’s facility. For simple extraction whenever required, the data obtained by the BT-300WD is stored in an SQL database and, during an inspection, is shown to the operators.
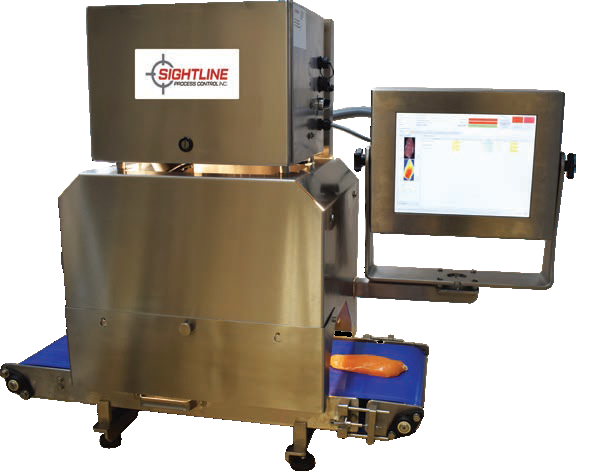
It was possible to automatically transfer data as the existing SPC software that the customer used was easily integrated into the Sightline system. The Sightline measura™ Inspection and Analytics software modules were successfully utilized to provide detailed metrics and reporting which were tailored to the customer’s specific operations.
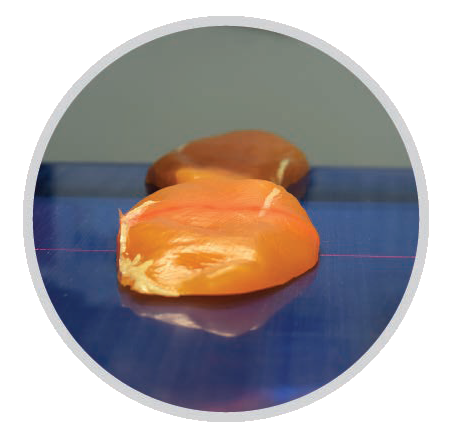
Figure 2. 3D Imaging with Sightline Automated Inspection System.
Results
Following the installation of the Sightline BT-300WD, the operations team efficiently adopted the new system. In the first quarter, operators were testing 1,700 butterfly breasts per month, which is an average increase of 380% in relation to the manual procedures used before the Sightline solution was deployed
The automated measurements improved reliability and precision, together with the substantially increased number of data points collected by the BT-300WD system, which led to a decrease in waste, higher quality, and higher productivity in downstream processing operations.
Utilizing both Sightline’s measura™ Analytics along with the company’s current software, inspection results can be assessed by the company’s managers in real-time, allowing data-driven decisions to be made.
All four of the outlined inspection goals were achieved and the customer has used more Sightline BT-300WD systems in its various manufacturing hubs across the country. The company is also discussing the possibility of utilizing Sightline for finished product inspection.
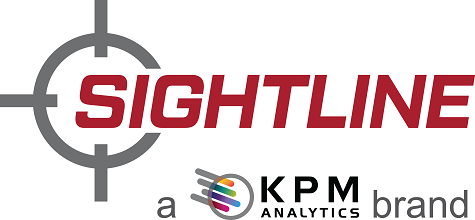
This information has been sourced, reviewed, and adapted from materials provided by Sightline Process Control Inc.
For more information on this source, please visit Sightline Process Control Inc.