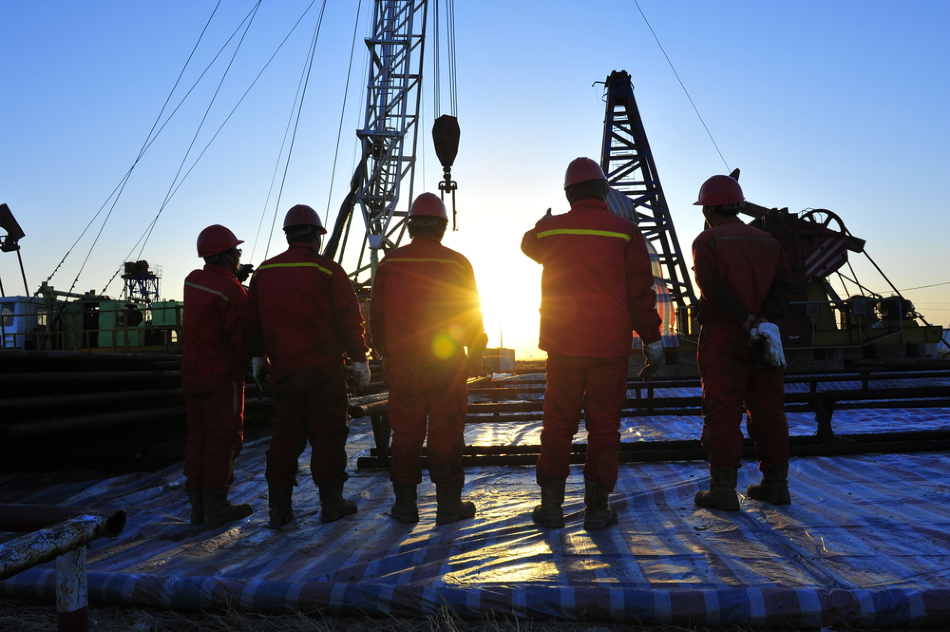
Image Credit: QiuJu Song/Shutterstock.com
Gases are used in many manufacturing environments, industrial sectors, and scientific industries. However, despite being vital for many applications—from use in chemical reactions to igniting a heating source, and many more in between—they can be dangerous if in the wrong environment or in too high concentrations. To monitor occupational, industrial and natural environments, gas analyzers are employed to measure whether there is a localized hazard.
Gases are present in everyday life. Some gases are used to provide an inert atmosphere for chemical reactions, some are used in combustion processes, while others are used to streamline the flow of different substances.
These gases need to be monitored to ensure that too high concentrations of certain gases (e.g. methane) will not cause an explosion, nor will the presence of other gases reduce the oxygen concentration (leading to breathing problems) in occupational environments, as well as ensuring that the correct gases are used in the correct processes/operations.
The Use of Gas Analyzers
Gas analyzers come in a number of forms, from large built-in sensor systems for larger monitoring purposes to handheld devices that provide quick localized measurements. Gas analyzers offer a way of determining the localized gas concentration, regardless of the industrial environment. This ensures that the workforce inside the industrial environment remains protected from harmful levels of gas build-up.
They also ensure that any operations that use gases are running optimally i.e. ensuring that the intended environment is not being flooded with too much gas, nor is too little gas being introduced to the operation (which could cause issues in itself if the process relies on gases).
Gas analyzers are also used by industry in areas outside of the processing environment. In these cases, measuring the local environment outside of the manufacturing/process environment is important for ensuring that not too many toxic/harmful gases are being released into the atmosphere: these emissions constantly require more rigorous monitoring due to the issues of greenhouse gases being released in too high quantities over the last few decades.
In the mining industry, gas analyzers offer a way to determine whether a build-up of gas is occurring during mining operations, which can often result in explosions as there are many methane deposits underground. This provides a much safer occupational environment for everyone involved.
In some other scientific industries, gas analyzers can be employed to measure the levels of gases produced in fermentation processes within biotechnology and food production processes. These are just a few specific examples.
Infrared Gas Analyzers
Infrared gas analyzers can measure a range of gases, with the specific gases being dependent on the manufacturer and type - there are many forms of gas analyzers out there. Most infrared gas analyzers will measure the concentration of carbon dioxide, carbon monoxide, oxygen, and methane, but many can measure the levels of nitric oxide, nitrous oxide and sulfur dioxide gases as well.
All gas analyzers have different working principles. Many shine a beam of electromagnetic light at the target environment, whereas others will cause the gaseous molecules to directly absorb onto a sensing surface. For infrared gas analyzers, it is the former; and as the name suggests, it is a beam of infrared light that is used to provide the analysis.
While the specific operational mechanism differs between the different gas analyzer manufacturers, their operational principles are generally similar. Many of them work using a flow cell—so that the gases will flow past the sensing area to enable localized and accurate measurements. As the gases flow past the analysis area, an infrared beam is fired through the gas.
The number of infrared waves absorbed by the sensor is picked up by the detector on the opposite side of the analyzer to the transmitter enabling the gas concentration to be determined.
In some systems, a reference cell is required containing a known concentration of the gas being analyzed, to calibrate the concentrations by measuring the difference between the real and reference values.
The types of gases in the environment are determined because many of the gases will absorb characteristic infrared waves, enabling the type of gas and its concentration to be determined simultaneously.
While the specific properties of each gas analyzer used in an industrial capacity varies from analyzer to analyzer, for them to be safe in industrial environments, many of them have sensitivities in the low parts per million (ppm) range, can measure changes in gas pressure, and are relatively quick (a few seconds) in their measurement times.
Given that many of them work using a flow cell, the flow properties of the analyzers also vary, but there are many parameters that are changeable in most gas analyzers to enable them to be used in different industrial environments. There are also a number of Fourier Transform Infrared (FTIR) gas analyzers in use now which provide analysis for hundreds of gases simultaneously at the parts per billion (ppb)level by measuring the whole infrared spectrum continuously.
References and Further Reading
Disclaimer: The views expressed here are those of the author expressed in their private capacity and do not necessarily represent the views of AZoM.com Limited T/A AZoNetwork the owner and operator of this website. This disclaimer forms part of the Terms and conditions of use of this website.