The technological advancements in laser sources and systems has given industrial laser users the benefit of improved quality and more reliable laser processes. Collaborations with laser applications development houses, system component manufacturers, and end users have enabled laser system integrators and OEMs to make advancements in their respective services and products.
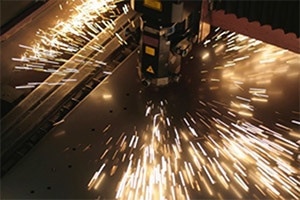
Figure 1. Laser sources and systems
During the development and installation of these laser systems, performance measurements of the system and components should be taken into account so that laser users can benefit from the highest quality system.
In some cases, the performance of the system after installation can be considered a lower priority by the end-sers. However, maintaining the system performance should be thought of as a way to protect the large investment in the equipment.
The continuous advancements of lasers in terms of power, consistency, and quality have also resulted in major advancements of systems for measuring laser performance (Figure 2). However, three things about lasers have remained the same;
- Lasers systems include components that contain physical matter, and over a period of time, these will degrade in one way or another.
- The power density of laser will define the way the laser interacts with the material, which is being processed by the system.
- The physical changes occurring in the laser system will lead to changes in the power density delivered by the laser.
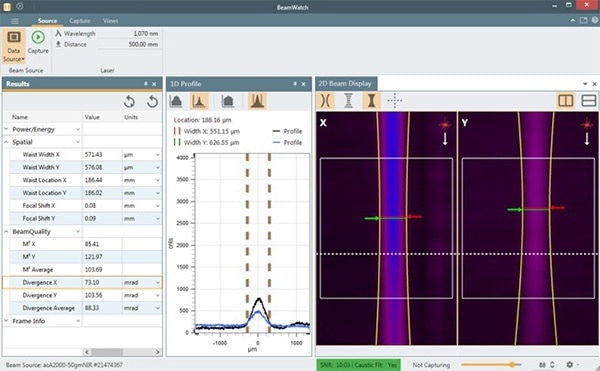
Figure 2. Laser performance measurement
It is possible to control these changes by taking regular measurements of the laser system as a whole. There can be a number of objections to carrying out these measurements, which this article aims to address.
Physical Barriers
Industrial lasers are typically designed with sufficiently high power to process material, by connecting pieces together, subtracting material, adding material, or altering the material’s physical properties. Traditionally, it has been quite complicated to measure these lasers, as users may end up damaging the measurement system during the course of the measurement.
Recent developments in laser systems and applications have led to increased laser powers in disc, fiber, and direct diode lasers. Materials that could not be processed before can now be processed efficiently, or will be able to in the near future. It is also possible to process materials at faster throughput rates.
With increasing laser power, the degradation of the laser systems as a result of aging, thermal effects and component contamination also increase further. When this degradation occurs, changes in the power density also occur, leading to issues such as reduced laser output power, or alterations in the laser’s focused spot location and size with regard to the material being processed.
Measurements on high-powered lasers have historically been problematic, since any measurement system impinging on the beam will have hard limits on the power density it can handle.
Overcoming Physical Barriers
Any modification occurring in the laser system due to ultimate thermal effects will alter the process, and this would often lead to inconsistent results, such as a reduction in the joint or a poor cut.
However, it would not be possible to control the changes with conventional measurement techniques, as they would fail to effectively determine the changes in the laser. This issue can be resolved by using non-contact measurement in the form of a technological advancement - BeamWatch® by Ophir-Spiricon.
In order to take a laser measurement, the BeamWatch utilizes a lens camera to image the Rayleigh Scattering from the focused beam that provides a laser image at and around the “beam caustic” or focused spot, without actually coming into contact with the beam.
As it does not impinge on the beam, the high power density does not directly affect the measurement system. In reality, it enhances the signal provided for analysis. As it is a camera-based system, dynamic measurement can be made and data points can be acquired several times a second.
Through such dynamic changes, laser users can visualize and determine the performance of the laser in real time. The size of the focused spot, shifts in the location of the focused spot, the M2 of the laser, along with a number of other important parameters, can be measured quantitatively with respect to time.
Changing Habits in Laser System Maintenance
When it comes to maintaining laser systems, a “don’t fix what isn’t broken” approach is often adopted. Methods used by laser users years ago are still considered to be fine today. However, tools and methods that were applied years ago do not provide a complete picture about the laser’s performance. This is particularly true when it comes to acquiring and studying time-based laser properties. Laser “power pucks”, laser burn paper, and acrylic mode blocks are legacy equipment that offer single data points in a short time period.
The current generation of laser measurement systems provide information from beam-on time to a number of seconds, minutes, or hours later, providing laser technicians with a better picture about the behavior of their laser system. Though newer laser measurement technologies can be daunting at first, a better understanding about the laser light’s behavior could be very important.
It is natural to be cautious when innovative technologies are introduced, as laser technicians do not know whether the data collected and results produced are indeed accurate. These questions were raised during the launch of the BeamWatch beam analyzer in 2013, because the method of producing the signal was novel to the industry.
Engineers at Ophir-Spiricon are confident that the data provided by the BeamWatch beam analyzer is precise within +/- 5%. This confidence comes from years of experience, mathematical proofs, measurement data, and a comparison of results with known measurement methods. The use of the BeamWatch beam analyzer has not only provided the expected results, but also provided data about the laser system that was never captured before.
Environmental Barriers
In addition to the physical and old habits barriers, environmental barriers are another aspect that are beyond the control of the user, or that the user would need to work hard to resolve. Money is lost when a costly tool breaks down. A general belief is that the laser should run continuously and must be maintained only when it is not operating efficiently or not working at all.
In most cases, the overall cost to this approach is much higher than the proactive approach of tracking the performance of the laser over time and searching for trends, which can point to a need for corrective action. Systems integrators and laser OEMs provide training on laser system maintenance, which helps laser users to understand the workings of their laser systems and also enables them to sustain high quality processes and troubleshoot issues as and when they occur.
Regulations
Laser systems in most industries are highly regulated. Companies have to prove to the FDA that their laser systems are working the way that they are intended to. As part of the regulation, laser measurements are usually required. Even when measurements are not needed, steps would still need to be adopted to make sure that the collected data is precise and that it can be applied to improve the laser process.
These barriers may prevent laser technicians and users from adopting new laser measurement practices. Nevertheless, dynamic laser measurements are the only way that laser users can achieve a complete analysis of the performance of the laser.
Laser users or technicians will often see the benefits provided by electronic laser measurement solutions. Being able to see what the beam actually looks like, including an array of quantifiable data, is generally highly convincing.
However, the benefits might not be so obvious to the person who purchases the laser measurement system. In such scenarios, the customer should realize that an appropriate use of laser measurement combined with appropriate laser maintenance training is less costly overall, compared to the cost of recovering from a major failure of their laser systems.
Why the Barriers?
The applications would appear to be limitless when considering laser technology developments as a whole. However, these changes highlight the need to understand and measure the lasers, and how they will behave after they are deployed for service.
Earlier, there were physical barriers when making laser measurements, but these constraints have now been removed. Systems measuring laser performance can be used easily. By understanding the fundamental behavior of lasers, users can easily set up the systems and can prevent the damage.
When the BeamWatch system is used, the system will not be damaged, as long as it is set up properly. Environmental barriers and traditional habits can be overcome once users realize the value of a proactive against reactive approach to laser maintenance.
By eliminating these barriers, users can realize the actual advantages of using laser performance measurement in their day-to-day maintenance routine.
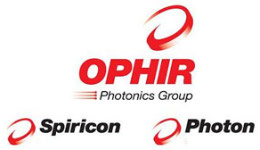
This information has been sourced, reviewed and adapted from materials provided by Ophir Optronics Group.
For more information on this source, please visit Ophir Photonics Group.