By Owais AliReviewed by Lexie CornerSep 3 2024
Optical coatings are thin films applied to optical devices to enhance their performance by manipulating light interactions such as reflections, transmission, and absorption.
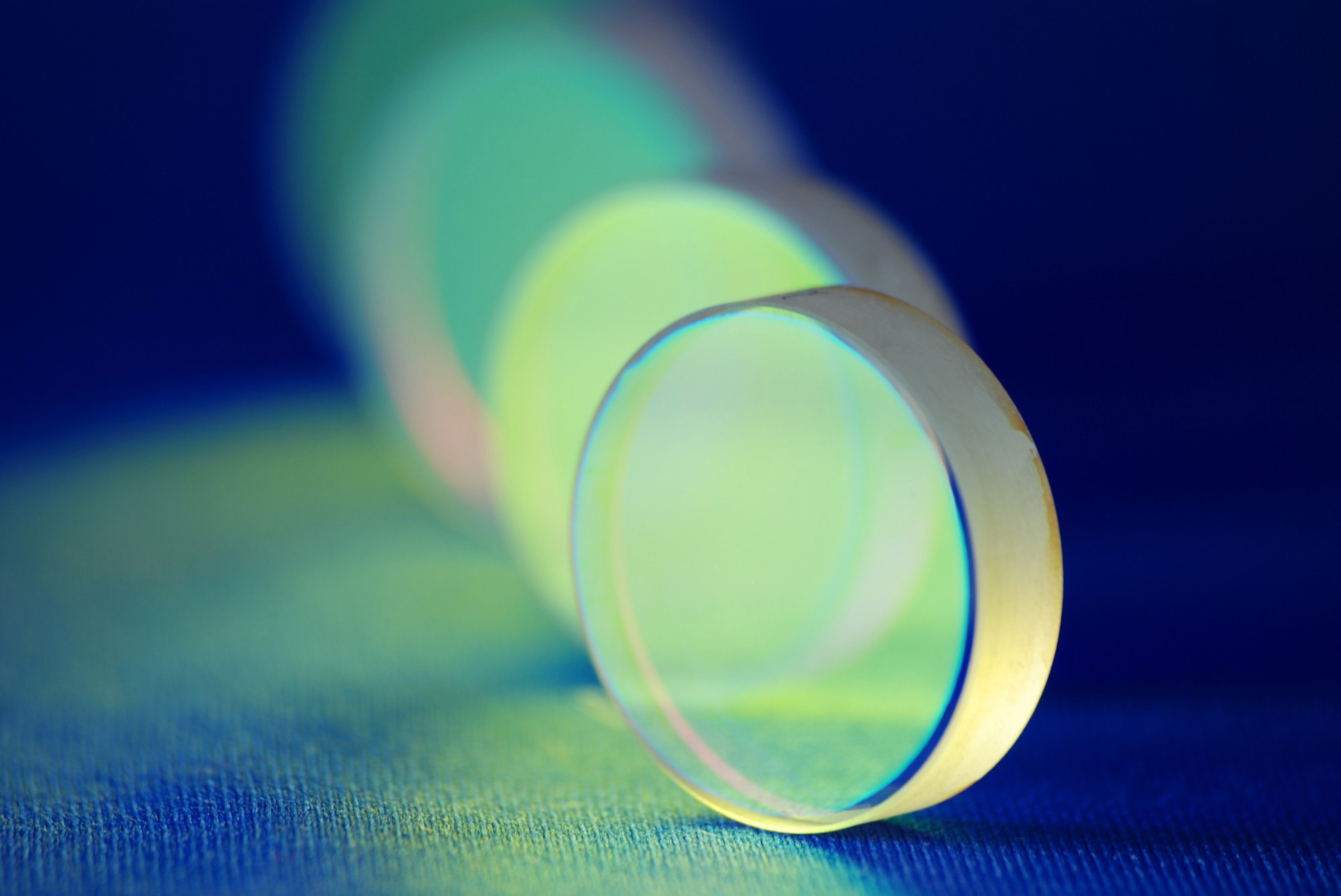
Image Credit: Yury Zap/Shutterstock.com
The history of optical thin-film coatings dates back to 1817, when Fraunhofer first discovered the anti-reflection effect of a single layer on glass. Since then, significant advancements have been made, and modern optical coatings now play a crucial role in electronics and various industries.
These developments address growing demands for enhanced performance and specialized properties, including ultra-low absorption coatings for gravitational wave detection and nano-structured films for next-generation sensors and imaging systems.1
Optical Coating Theory
The behavior of light at the interface between two materials is described by the Fresnel equations and Snell's law. When light encounters a boundary with differing refractive indices, some is reflected while the rest is transmitted.
Snell's Law: n1sin(θ1) = n2sin(θ2)
Fresnel Equations (for s-polarization):
- Reflection coefficient: r = (n1cos(θ1) – (n2cos(θ2)) / (n1cos(θ1) + n2cos(θ2))
- Transmission coefficient: t = 2n1cos(θ1) / (n1cos(θ1) + n2cos(θ2))
Optical coatings utilize these principles by applying layers with varying refractive indices to control surface-light interaction.
The simplest optical coating consists of a single layer with a thickness of one-quarter of the wavelength of light (λ/4), creating destructive interference that reduces reflectance. More complex coatings involve multiple layers to achieve desired optical properties across various wavelengths.2
Types of Optical Coatings
There are various types of optical coating, each designed for specific functions.
Anti-Reflective Coatings
Anti-reflective (AR) coatings are among the most prevalent optical coatings commonly applied to eyeglasses, camera lenses, and various optical devices to minimize reflections and enhance light transmission.
AR coatings cancel out reflected light waves via destructive interference, leading to clearer vision and sharper images, particularly in low-light conditions. They also improve comfort by minimizing glare and internal reflections, making them essential for applications requiring high optical clarity, like night vision and high-definition cameras.
High-Reflective Coatings
High-reflective coatings are designed to maximize reflectivity by layering materials with varying refractive indices to achieve levels exceeding 99.99 % at specific wavelengths. They are exceptionally thin yet durable, able to withstand extreme conditions and cover a wide wavelength range from 200 nm to 2000 nm.
These coatings are commonly applied in laser systems, movie projectors, mirrors, and solar panels to minimize light loss and enhance fast focusing.
Beamsplitters
Beamsplitters are partially transmitting coatings designed to divide a single light beam into multiple beams, making them crucial for interferometers, lasers, and imaging systems. They can be dielectric or metallic, with customizable splitting ratios and anti-reflection coatings on the backside to minimize secondary reflections and energy loss.
Plate beamsplitters feature a thin layer of optical glass or quartz with a semi-transparent reflective coating, whereas cube beamsplitters consist of two prisms with internal coatings to achieve efficient light reflection and transmission.
Filter coatings
This group of coatings manipulates the spectral composition of light by selectively transmitting or blocking specific wavelengths, enabling precise spectral management. They include bandpass filters that transmit a specific range of wavelengths, longpass filters that allow wavelengths longer than a cutoff point, shortpass filters that permit wavelengths shorter than a cutoff, and notch filters that block a narrow range of wavelengths.3,4
How are Optical Coatings Applied?
Optical coatings are applied through sophisticated processes typically conducted using physical vapor deposition (PVD) techniques in a vacuum chamber.
E-Beam Deposition
One common method is electron-beam evaporation, where an electron beam heats and vaporizes the coating material, such as metal oxides or halides, onto a substrate at elevated temperatures (200-250 °C), ensuring good adhesion and material properties.
An advanced version of this technique is ion-assisted deposition (IAD), which incorporates an ion beam to improve coating density and enable deposition at lower temperatures (20-100°C). This makes it ideal for temperature-sensitive substrates and results in coatings with reduced spectral shifting and greater durability.
Ion Beam Sputtering (IBS)
Ion Beam Sputtering (IBS) uses high-energy ion beams to sputter atoms from a target material, forming dense and smooth films on optical components. It offers precise control over coating parameters and high-quality, repeatable coatings, though it is more costly and slower than other methods.
Magnetron Sputtering
Magnetron sputtering uses magnetic fields to enhance the sputtering process, enabling efficient deposition of a wide range of materials onto a substrate within a vacuum at pressures less than one ten-millionth of atmospheric pressure.
This method is cost-effective, highly flexible, operates near room temperature, and is compatible with a wide range of coating materials, especially large substrates used in flat displays.2,5
Common Coating Materials
The materials used in optical coatings are selected based on their optical properties and application requirements.
For example, dielectric materials such as silicon dioxide (SiO₂) and magnesium fluoride (MgF₂) are favored for their transparency and controllable refractive indices, whereas metals like aluminum, silver, and gold are used in reflective coatings.
Semiconductors such as silicon and germanium are utilized in infrared optics due to their hardness, low absorbance, and anti-reflective qualities.
Fluoride-based coatings, such as magnesium fluoride (MgF₂), excel in high-temperature and shock-resistant environments, offering low absorption properties, durability, and scratch resistance, making them particularly suitable for automotive applications.2
Key Applications of Optical Coatings
Optical Lenses and Precision Optics
In ophthalmic applications, anti-reflective coatings on eyeglasses and contact lenses reduce glare and improve visual clarity, enhancing the wearer's comfort and vision. The photography and videography industries heavily rely on multi-layer coatings for camera lenses to enhance image quality by reducing flare and ghosting, resulting in sharper, more vibrant images.
Architectural Glass and Glazing
Wet-chemical coatings create anti-reflective and scratch-resistant layers on glass and polycarbonate. Low-emissive (low-E) coatings minimize heat loss, and spectral selectivity coatings control heat and light transmission. These coatings significantly reduce energy costs in skyscrapers by minimizing heat gain in summer and heat loss in winter.
In residential applications, electrochromic coatings enable smart windows that adjust tint based on sunlight intensity or user preferences, offering dynamic light control.
LiDAR and Sensing Technologies
Optical coatings in LiDAR systems and sensing technologies enhance light transmission, reduce reflection losses, and minimize signal noise. These improvements are critical for accurate object detection and navigation in autonomous vehicles and detailed crop monitoring in agriculture. They also support precise environmental and geological surveys for better climate change understanding and resource management.
Augmented and Virtual Reality Displays
Advanced anti-reflective optical coatings are used in augmented and virtual reality displays to reduce glare and maximize light transmission. This results in clearer, more vivid images, enhancing user experience in gaming, professional simulations, and other applications by minimizing visual artifacts and reducing user fatigue.
Automotive and Aerospace Applications
In automotive and aerospace industries, coatings like indium tin oxide and fluorine-doped tin oxide enhance thermal insulation, reduce ice formation on windshields, and improve visibility in adverse conditions. These coatings also contribute to vehicle efficiency by reducing weight and improving aerodynamics, leading to better fuel efficiency and lower environmental impact.
Data Displays and User Interfaces
In industrial control panels, medical equipment, and commercial interfaces like automated teller machines (ATMs) and gas pumps, optical coatings optimize brightness, contrast, and clarity, ensuring that critical information is readable in various lighting conditions.
For outdoor displays, specialized ceramic coatings provide heat rejection and infrared blocking, maintaining performance in harsh environmental conditions. Additionally, scratch-resistant coatings are commonly used to increase the longevity of touch-sensitive screens, reducing maintenance costs and improving user experience.6
Benefits of Optical Coatings
Optical coatings enhance optical system performance significantly. They improve transmission, reflection, and polarization properties, leading to better image quality and higher signal-to-noise ratios. For instance, an anti-reflection coating can reduce surface reflection from 4 % to less than 0.1 %, while a highly reflective dielectric coating can increase reflectivity to over 99.99 %.
Durability is another key benefit of optical coatings. These coatings offer improved abrasion resistance, protecting surfaces from scratches and mechanical wear, which extends the lifespan of optical components and maintains their performance, particularly in harsh or high-use scenarios.
Optical coatings can induce advanced functionalities, such as wavelength separation with dichroic filters and increased energy efficiency in solar panels and windows. They also facilitate the miniaturization of optical systems by precisely controlling light interactions, allowing for the design of smaller, more efficient components, crucial for compact, portable devices in fields like medical diagnostics and telecommunications.6
Conclusion
Optical coatings are vital in modern optical systems, offering precise control over light interactions with surfaces and significantly enhancing the performance, efficiency, and durability of various technologies, from consumer products to scientific instruments.
Ongoing research promises advancements in coating technologies and materials, leading to more efficient optical systems. These improvements are expected to drive innovation in renewable energy, telecommunications, and medical imaging, pushing the limits of optics and photonics and fostering technological progress across multiple industries.
More from AZoOptics:
Modern Manufacturing: Advancements in Optical Processing Techniques
References and Further Reading
- Song, S., Gibson, D. (2018). Applications of Optical Thin Film Coatings. Coatings.https://www.mdpi.com/journal/coatings/special_issues/optical_film_coat
- Stenzel, O. (2014). Optical Coatings: material aspects in theory and practice. Optical Coatings. https://doi.org/10.1007/978-3-642-54063-9
- Shanghai Optics. (2024). Optical Coatings. [Online] Shanghai Optics. Available at: https://www.shanghai-optics.com/about-us/resources/technical-articles/types-of-optical-coatings/
- Sunita, P., Kumar, VSP., Mukesh, K., Neelam, K., Rao, PK., Vinod, K. (2018). Optical Thin Film Filters: Design, Faurication, and Characterization. In High-Performance Materials and Engineered Chemistry (pp. 3-34). Apple Academic Press. https://www.taylorfrancis.com/chapters/edit/10.1201/9781315187860-1/optical-thin-film-filters-design-faurication-characterization-parinam-sunita-vemuri-srs-praveen-kumar-kumar-mukesh-kumari-neelam-parinam-krishna-rao-karar-vinod-sharma-amit
- Lacroix, B., et al. (2022). Texture in ITO films deposited at oblique incidence by ion beam sputtering. Applied Surface Science. https://doi.org/10.1016/j.apsusc.2022.154677
- Piegari, A., Flory, F. (Eds.). (2018). Optical thin films and coatings: From materials to applications. Woodhead Publishing. https://www.abebooks.com/9780081020739/Optical-Thin-Films-Coatings-Materials-0081020732/plp
Disclaimer: The views expressed here are those of the author expressed in their private capacity and do not necessarily represent the views of AZoM.com Limited T/A AZoNetwork the owner and operator of this website. This disclaimer forms part of the Terms and conditions of use of this website.