In an article published in the open-access journal Sensors, researchers suggested a novel laser parameter measuring technique based on cone-arranged array fibers to enhance the measurable spot size, spatial sampling resolution, and permissible incidence angle range.
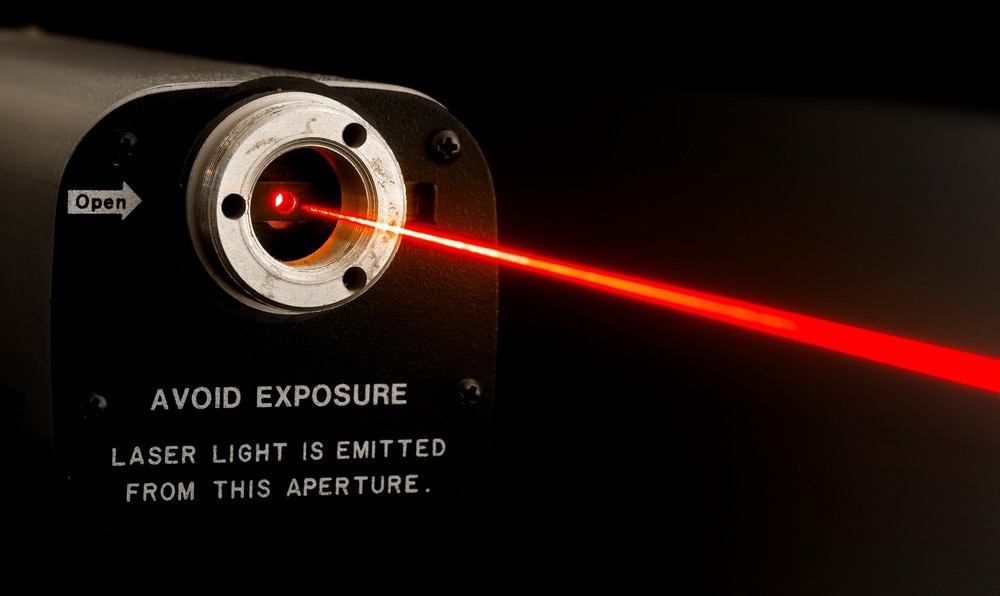
Study: Study on Laser Parameter Measurement System Based on Cone-Arranged Fibers and CCD Camera. Image Credit:Doug McLean/Shutterstock.com
The cross-section spots of the laser beams were sampled and reduced using a conical array made of flexible fibers in this laser parameter measuring method. The laser parameter technique allowed low-distortion shooting via a charge-coupled diode (CCD) camera. Finally, the spot was corrected through homogenization processing and algorithm analysis.
The authors demonstrated that with the laser parameter measuring method, it was possible to measure the skew angle with excellent accuracy at decimeter-level spot receiving surfaces, high tolerance, and millimeter-level resolution. The root mean square error (RMSE) for the power in the bucket (PIB) curves, when contrasting the measured spot in normal incidence with the actual one, was less than 1%.
Based on the assumption that the array fibers' numerical aperture (NA) was 0.22, the RMSE was less than 2% when the incident angle variation was between -8° and 8°. In contrast, the measurement error of total power was less than 5%. It was also reported that modifying the fiber characteristics and design of the array fibers allowed further optimization of the measurement technique.
Understanding the Laser Parameter Measurement Technique
The laser parameter is an influential factor in the scientific assessment of laser systems. By evaluating the intensity distribution in one or more axial cross-section sites, it is possible to determine the standard laser parameter like beam width, M2 factor, and factor. The measuring system prioritizes the array fibers of detection units and attenuation when the spot is significant.
Since the system always has a big aperture, it is simple to remedy the inconsistent responsiveness of sample units by calibrating the entire target. However, the intricate unit architecture frequently limits its resolution. In many applications, the units' transmittance and responsiveness are also sensitive to the incidence angle, which is a substantial cause of the error.
Typically, a CCD camera is utilized when the spot is small. The beam can be imaged on different screens and then captured by the CCD camera, or it can operate directly on the CCD array fibers in the camera. However, CCD camera shooting requires exact spatial alignment. Therefore, rapid servo equipment is needed, which makes practical applications more challenging.
Additionally, the critical reason limiting the resolution shifts from the attenuator or detector's outside diameter to the sampling unit, which results in a notable improvement in resolution. In conclusion, the two methodologies can be used to improve the overall laser parameter measuring system.
Thus, the authors suggested sampling and shrinking the beam using cone-arranged array fibers in this paper. The optical waveguide served as a conduit for the beam's propagation route after leaving free space. As a result, the high-uniform transmission of the array fibers could be used to produce the high-fidelity shrinkage of the spot.
This research aimed to develop a laser parameter measurement technique based on this application to demonstrate its viability. The closely packed array fibers at the opposite end were utilized as the output, while the protection target plate with loosely spaced fibers was employed as the input. Also, the intensity distribution was computationally rectified by crosstalk elimination, average pooling, and interpolated beam expansion after the CCD camera captured the spot imaged on the homogenizer.
The study outcomes demonstrated that the intensity distribution's RMSE for the PIB curves between the two points was less than 1%. Also, the shift in the measured total power was just below 2% in the interval of -6° ~ 6°. In comparison, the RMSE of the PIB curve was less than 1% in the interval of -8° ~ 8°. These values were less than 5% and 2%, respectively, assuming that the theoretical NA of the array fibers was 0.22.
Proof-of-Concept Investigations
A high-reflectivity target plate, array fibers, attenuator, filter, homogenizer, packaging structures, CCD camera, and a data-processing system were the essential components of the instrument design. The array comprised 400 equal-diameter flexible multimode step-type fibers arranged in 20 rows and 20 columns. These rows and columns of array fibers were placed within a specific distance perpendicular to the array face.
The cone-arranged array fibers-based beam quality measurement system and the accompanying computational correction were described in this work. This system achieved a laser parameter measurement aperture of approximately 114 mm, a resolution of 6 mm, and a viable wavelength range of 600-1800 nm.
The CCD camera captured images of objects less than 3 mm in length after the array fibers reduced the beam's width by 40 times. Hence, the distortion was ignored without requiring a wide field of vision. Finally, a large-size Gaussian spot was reduced in size, photographed, then restored to check the technology's accuracy. The resulting image was then contrasted with one of the real spots captured by the diffuse reflection screen at the exact axial location.
The measured spot closely resembled the actual location, and their PIB curves were harmonious, with an RMSE value of 0.85%. Moreover, less than 6 mm of the sample resolution, or about 0.44 mm, separated the diameters of the two sites' 86.5% PIB. Only 2% at -6° ~ 6° and approximately 5% at -8° ~ 8° of the total power measured change. A similar pattern was seen in the power density distribution. Here, the RMSEs between the measured PIB curves and the actual PIB curves for the spot were less than 1% at -6° ~ 6° and just below 2% at -8° ~ 8°.
Significance and Findings of the Study
This study proposed a novel method for laser parameter measurement based on a collection of cone-arranged array fibers. The computational correction and the system were established and verified through theoretical and experimental study.
Regarding power density distribution, centroid jitter, and centroid position, the results demonstrated that the measured spot closely matched the actual spot. Therefore, it established a foundation for precisely estimating the laser parameter.
The CCD camera could capture larger spots since the cross-section spot was shrunk with excellent fidelity, which prevented distortion produced by a large field of vision. Also, the sampling resolution was greater than the conventional array target, and the design was more flexible.
Finally, the range of permitted incident angles was acceptable. When the beam’s incident angle was between -8° and 8°, both the power density distribution and the total power of the spots were measured with high accuracy.
Reference
Luo, J., Qin, L., Hou, Z., Zhang, S., Zhu, W., Guan, W. (2022) Study on Laser Parameter Measurement System Based on Cone-Arranged Fibers and CCD Camera. Sensors, 22(20), 7892. https://www.mdpi.com/1424-8220/22/20/7892/htm
Disclaimer: The views expressed here are those of the author expressed in their private capacity and do not necessarily represent the views of AZoM.com Limited T/A AZoNetwork the owner and operator of this website. This disclaimer forms part of the Terms and conditions of use of this website.