In an article published in the journal Micromachines, researchers designed a novel measurement technique that combines transmission digital holographic microscopy (DHM) and reflection DHM to obtain thickness and surface information of elements to deduce the 3D structure.
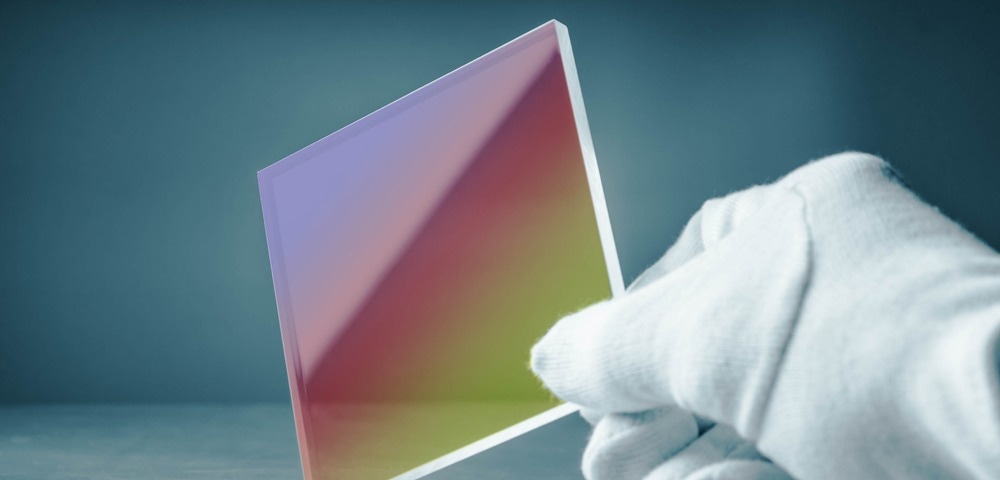
Study: A Novel Approach for Measurement of Free-Form Optical Elements with Digital Holographic Microscopy. Image Credit: luchschenF/Shutterstock.com
Free-Form Optical Elements
At the moment, free-form optical components are crucial in many industries. They are important components in an expanding variety of optical systems to boost their performance. For instance, free-form optical elements are used in head-mounted displays and micro-projectors to decrease size and weight, as well as enhance picture quality. In car and street lighting, they are used to expand the effective illumination range and improve energy efficiency.
However, due to their high complexity and lack of rotational symmetry, free-form optical components provide substantial hurdles for high-precision measurements. These issues include how to further enhance measurement accuracy, efficiency, and adaptability to attain the high performance and low cost needed for their field of application.
Contact Measurement Methods
Two types of measuring techniques are now used for free-form optical elements: contact and non-contact. The CMM and profilometer techniques are examples of contact methods that employ a point-by-point scanning methodology for measuring with an accuracy of microns in the vertical direction and run the risk of contaminating the sample.
Although the profilometer approach is more precise than the CMM method, it can only be used to measure aspheric off-axis free-form surfaces at this time. Furthermore, contact approaches are no longer sufficient due to the high requirements of polished optical free-form components for measuring precision and range.
Non-Contact Measurement Methods
Due to its potential for full-field non-destructive measurement, non-contact techniques have drawn much interest. Exemplary techniques include interferometry, structured light 3D measurement, and Shack-Hartmann wavefront detection.
Interferometry has received universal acclaim as one of the most precise detection techniques now available for the detection of aspheric surfaces, spherical surfaces, and optical planes. Digital holographic microscopy (DHM), a technique for ultra-high precision interferometry, has attained sub-nanometer scale axial resolution, allowing for quick and contamination-free detection and having a wide range of applications in high-precision measurement.
(a,b) The structure of the sample at different angles, MLAs on the top of the surface. (c) The designed structure of the sample, the MLA parameters shown in the zoomed image. Xuhui Zhang , Chonglin Wu, Lei Chen, Gengliang Chen and Guoliang Zheng (2022)
How the Study Was Conducted
By examining the measurement outcomes of a free-form optical element, the researchers in this work have shown the distinctive benefits of DHM for measuring certain kinds of optical elements. They created a cutting-edge technique for measuring such an element that gathers thickness and surface data by independently transmitting and reflecting the DHM. The findings are consistent with the intended and produced specifications when the thickness and surface data are combined to determine the element's structure.
Important Measurements
The measured optical element features a concave bottom surface, a top surface covered in microlens arrays, and total exterior measurements of 40x40x1.5 millimeters. The important measurements are the aggregate radius of curvature of the top and bottom surfaces, the microlens's vector height, the diameter of the aperture, and the center's radius of curvature, with the corresponding values being 33.3 μm, 31.8 millimeters, 10.9 μm, 241.5 μm, and 900 μm.
White light interferometer findings are erroneous due to substantial under-measurement of light scattering. To measure such an element, this study developed a digital holographic interferometric technique that combines transmission and reflection DHM to provide a completely structured measurement.
Digital Holographic Microscopy (DHM)
The laser offers a better coherent light in transmission DHM to produce high-contrast interferences. The laser travels via the polarization beam splitter and is divided into two beams. The non-polarization beam splitter reflects and transmits these two beams, which have a little variation in their angles of incidence, but they interfere with one another. The CCD sensor captures the hologram, which is subsequently sent to the computer for processing.
The 3D surface form of the element was effectively retrieved by the DHM system using holograms captured at 20x and 4x objectives. The measurements were accurate and in line with the manufactured and designed specifications, highlighting the distinct benefits of DHM for measuring certain kinds of optical components.
Significant Findings of the Study
The measuring technique described in this study is an inventive fusion of techniques for recreating the form of micro and nano components by interferometric phasing. It incorporates holograms of transmitted DHM and reflected DHM.
An optical element with free-form surface characteristics serves as the measurement's subject. The essential features and element roughness was measured by the researchers and given quantified values. The element is compatible with the designed and fabricated structure, as shown by comparing the theoretical and measured values. The measuring techniques include off-line 3D reconstruction, high resolution, label-free, non-contact observation.
This technology may be used in various domains, including the biological sciences, MEMS measurements, and tiny optical element characterization. It is also possible to detect free-form optical components with great accuracy and little scattering.
Reference
Xuhui Zhang , Chonglin Wu, Lei Chen, Gengliang Chen and Guoliang Zheng (2022) A Novel Approach for Measurement of Free-Form Optical Elements with Digital Holographic Microscopy. Micromachines. https://www.mdpi.com/2072-666X/13/10/1719/htm
Disclaimer: The views expressed here are those of the author expressed in their private capacity and do not necessarily represent the views of AZoM.com Limited T/A AZoNetwork the owner and operator of this website. This disclaimer forms part of the Terms and conditions of use of this website.