In a study published in Optik, researchers proposed an expert optimization model for optical design performance and parameters of an imaging system. The proposed solution achieves optimal performance by reducing the optical lens system errors.
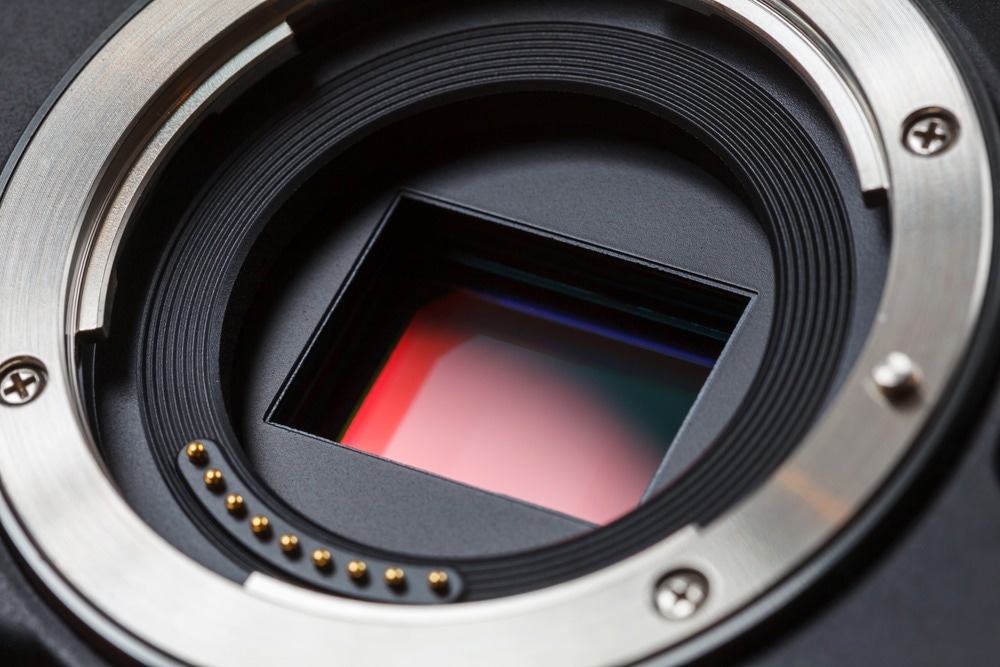
Study: An Optical Design for Enhanced Image Quality Based on Minimal Lens Error Optimization. Image Credit: Alex Yeung/Shutterstock.com
Imaging Lenses
Imaging lenses are parts of imaging systems that concentrate an image of the object being examined onto a camera sensor.
Concave lens
A concave or diverging lens is thicker at the sides and thinner at the center. It diverges straight light beams to generate diminishing, virtual and upright images.
Convex lens
Converging or convex lenses have a thicker center and a narrower edge. A convex lens causes parallel light rays to be refracted and converge at a single point.
A convex lens can produce images with varying characteristics. For example, images formed can be virtual or real, upright or inverted, and magnified or smaller, depending on the object's distance from the lens.
Optical Aberrations
Spherical aberration
A single convex lens cannot produce sharp images since it does not bring all parallel rays to a common focal point, resulting in spherical aberration. As a result, it causes the creation of highly distorted or blurred images.
Chromatic aberration
Chromatic aberration occurs when a lens either cannot focus all color wavelengths onto the same focal plane or when various color wavelengths are concentrated at different locations on the focal plane.
Therefore, multiple lenses are installed in microscopes and cameras to correct these aberrations to generate clear, high-resolution images.
Optimized Imaging Design
High-quality images can be achieved with an optimal imaging design when all design constraints, including size, manufacturing limitations, and tolerances, are within acceptable ranges.
Tools such as lens optimization tolerancing and sequential ray tracing contain unique optimization algorithms for efficient system design; these algorithms may include either a local or global optimization model.
Various general-purpose global and local optimization algorithm models have been developed to address various scientific and engineering issues. These open-source models are also applicable to optical design.
For example, after the error function of a lens is created, these algorithms can alter the optimization variables to decrease the error function's value. This removes the optic aberrations and enhances the performance of the imaging system.
Using an Expert Optimization Model to Reduce Optical System Errors
In this study, an expert optimization model was proposed to address a basic lens design issue involving the optimization of a gauss lens. Expert optimization model combined asphere expert, automatic optimization, and glass expert tools to achieve the maximum optical design performance.
Each system was validated using CODE V analytical instruments such as the spot diagram, quick ray aberration and modulation transfer feature (MTF). The spec evaluation technique was used to analyze the specification builder, which comprises all performance analysis goal values and optical design parameters.
An RMS wavefront error function was developed using the proposed expert optimization model to remove the aberrations and errors. The RMS wavefront error function quantifies errors as the difference between the ideal and real spherical wavefronts converging on the single image point.
After the implementation of each tool, all analysis metric values and design parameters were automatically shown in the spec builder. Goal mode was used to verify that all metrics values correspond to their targeted values.
Important Findings of the Study
The proposed expert optimization model enhanced and optimized the imaging system's performance. The suggested model can analyze the optical system error function and performance by tracking the field rays at 25o, 20o, 15o, 10o, 5o, and 0o.
The spherical tool integrates a spherical glass surface with an optical design parameter to reduce the size of the convergence point at the image sensor during both initial and automated design processes. As a result, the spherical tool minimizes the error function from 1495 to 123.
The aspherical tool enhances system performance by including the asphere glass substitution method into the optical design parameters with the help of asphere, glass fitting, and glass expert techniques.
The spot size of the percent and RMS error functions at the semi-field of view 25o are 0.153595 and 0.034659, respectively. The spot size of the aspherical design is five times less than that of the spherical design.
Reduction in RMS and error function values increases the MTF metric values to 0.7466 and 0.3686 at the field of view 0o and 25o.
The spec builder optical design solution satisfies all design specifications and performance measures. Future modifications will be made to the proposed expert optimization model to improve optical design performance and parameters.
Reference
B N Vijay Kumar Gowda, Sabitha Gauni and Vivek Maik. (2022). An Optical Design for Enhanced Image Quality Based on Minimal Lens Error Optimization. Optik, 169934. https://www.sciencedirect.com/science/article/abs/pii/S0030402622011925
Disclaimer: The views expressed here are those of the author expressed in their private capacity and do not necessarily represent the views of AZoM.com Limited T/A AZoNetwork the owner and operator of this website. This disclaimer forms part of the Terms and conditions of use of this website.