In a study published in Sensors, researchers proposed a novel embedded sensor for noninvasive in-vitro measurement and continuous monitoring of engineered-muscle-tissue contractility.
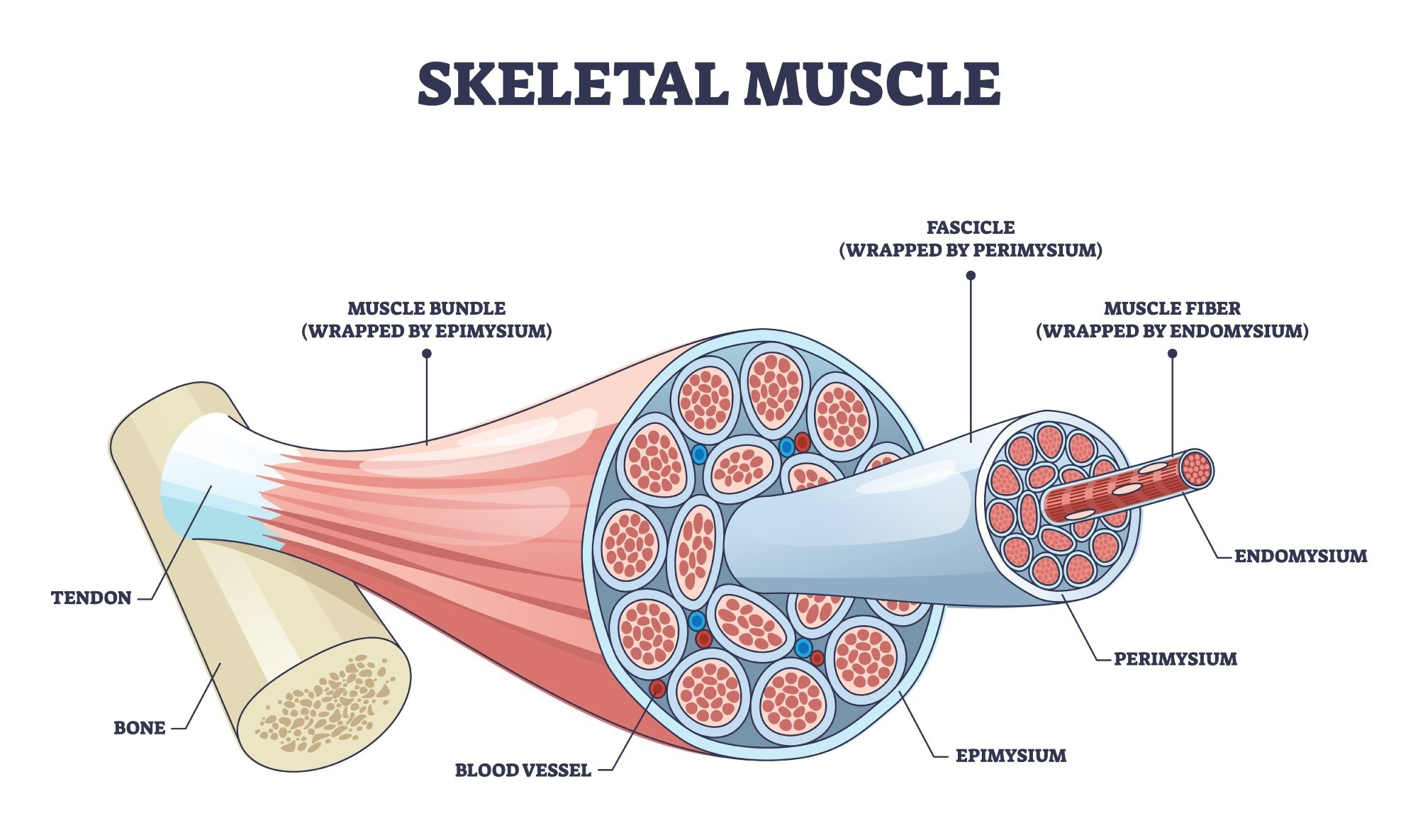
Study: The Development of an Innovative Embedded Sensor for the Optical Measurement of an Ex-Vivo Engineered Muscle Tissue Contractility. Image Credit: VectorMine/Shutterstock.com
Significance of Skeletal Muscles in Tissue Engineering
Tissue engineering is a cross-disciplinary method for creating novel bio-artificial alternatives for damaged tissues and organs.
Among all tissues, skeletal muscle is the most abundant tissue in the human body, accounting for 40-50% of total weight. It is a metabolically active tissue that requires a continuous flow of nutrients and metabolites. It is delivered by a large capillary network that forms an orderly pattern throughout the muscle fibers.
In-vitro skeletal muscle engineering has potential applications in drug screening, tissue replacement, and treating various muscle diseases caused by electrical stimulation or spontaneous contraction.
Technologies for Characterization of Engineered Tissues
The ability to precisely regulate and measure the functional characteristics of engineered muscle tissues is an essential component of tissue engineering, enabling a reliable assessment of the tissues before transplantation or modeling for investigating disease alterations.
Establishing new technologies and platforms for measuring the contractile activities of in-vitro-created tissues is critical for improving tissue development.
Traditional methods for measuring tissue contractility
Most conventional techniques rely on attaching a high-resolution force transducer to one end of the designed specimen while anchoring the other to the substrate. Even though force measurements have a high degree of precision, using a force transducer only enables endpoint measurements and necessitates physical contact with the specimen.
To measure tissue contractility, one end of the tool must be detached from its anchor and attached to the force transducer, potentially causing damage to the tissue's structure and resulting in changes in contractility measurements.
Noninvasive optical methods
Noninvasive technologies and methods, such as optical approaches, have recently been developed for measuring tissue contractile force to overcome the shortcomings of traditional systems.
However, they are extremely difficult to implement since they need microfabrication facilities or specialized fabrication equipment. In addition, integrating them with other measuring systems is challenging.
High-speed traction microscopy
Recently, traction force microscopy has been suggested to measure tissue contractility. The working principle of this technology is based on recording tissue culture's bioelectrical signal.
Traction force microscopy is noninvasive and compatible with high-resolution measuring systems, but it has some limitations.
First, it measures the relaxation and contraction velocities curves rather than measuring contractile force directly, with contractility often measured as a percentage of movement.
It is compatible with limited types of tissue culture and requires the entire tissue culture to be placed in close contact with the device, which can cause damage to tissues.
Developing an Optical Sensor for In-Vitro Noninvasive Measurements of Tissue
In this study, researchers created an embedded sensor that uses an optical tracking algorithm to continuously measure the contractility of synthetic muscle tissue. The sensor core is built around a calibrated pin that supports the muscle tissue under observation and monitors movement using an optically noninvasive technique.
The proposed sensor calibrates using a micro-force transducer and a linear actuator and then outputs the force generated by the 3D in-vitro system.
The noninvasiveness of the embedded sensor in terms of correct tissue development was verified by continuously measuring the contractile force of five 3D-engineered skeletal muscle tissues for five days.
Significant Findings of the Study
The experiments on five healthy 3D-engineered skeletal muscle tissues revealed that the sensor successfully measured dynamic changes in force responses without damaging muscle tissues.
The coefficient of variation acquired during the calibration method validated the sensor's accuracy in measuring forces.
The proposed sensor was used to quantify the contractile force present in accelerated aging, a specific physio-pathological condition. The results demonstrated that the sensor could also distinguish changes in the force generated by tissues treated to imitate an aged microenvironment.
The sensor was designed to not disrupt the growth and development of the engineered muscle tissue and to prevent numerous changes in the tissue's connections to the external force transducer, allowing it to be fully embedded in ordinary culture dishes.
Due to this, it was simple to link the sensor with an optical system to perform continuous measurements for extended periods and detect tissue contraction non-invasively.
In addition, the sensor was developed using inexpensive materials, and its manufacturing took only a short period because no specialized equipment was needed.
Reference
Apa, L., Cosentino, M., Forconi, F., Musarò, A., Rizzuto, E., & Del Prete, Z. (2022) The Development of an Innovative Embedded Sensor for the Optical Measurement of an Ex-Vivo Engineered Muscle Tissue Contractility. Sensors. https://www.mdpi.com/1424-8220/22/18/6878
Disclaimer: The views expressed here are those of the author expressed in their private capacity and do not necessarily represent the views of AZoM.com Limited T/A AZoNetwork the owner and operator of this website. This disclaimer forms part of the Terms and conditions of use of this website.