Apr 29 2016
Quality control is essential in production plants. Also for the food and beverage production. It doesn't matter if it is packaging, labeling or the cap, zero error production is a necessity. To guarantee a zero error production the image processing software (such as the EyeVision software) and the appropriate hardware such as smart cameras are getting more and more powerful. This leads one to believe that there is already an image processing solution for each machine vision application.
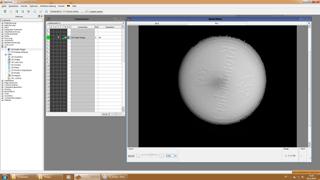
The EyeVision software for example contains commands for various measurement technology applications, for pattern matching, for code reading, for object counting or in plain terms for error detection (scratches, holes, cracks, contaminations, printing or color errors, etc.)
Concerning the bottling industry, the EyeVision software not only inspects the fill level, detects if bottles are without caps or checks the correct position of the label, it also offers the opportunity to inspect with a 3D application, that the cap is not askew.
Then if the cap is not in the correct position, it can also mean that the cap does not close tight and the bottle is leaky. And a sealed bottle is an essential requirement for the quality control of a bottling plant. Not only that the liquid can leak from the bottle, but also the leakiness can influence the quality and expiration of the product and is therefore inadmissible for customer and bottler. The EyeVision software supports various 3D sensors such as e.g. the EyeScan AT 3D and contains commands for evaluating point clouds and grayscale images. The EyeScan AT 3D has a profile resolution of up to 4096 points/profiles (4k Ultra-HD) and integrated 3D evaluation algorithms with up to 25 kHz and a robust enclosure with IP67 and M12 connectors.
In the concrete case of a bottling plant, the requirement was to check the cap on glass bottles with metal caps, which do not have a measurable cap curve, such as beer bottles with crown caps. To guarantee that is tightly seals with a crown cap, the EyeScan AT 3D inspects with laser triangulation principle, if the cap askew or is not present at all. So if the cap is askew or missing, the whole crate is discharged and the defective bottle exchanged against a new one.
The sensor is aligned vertically over the crate. On defined positions in the camera image the distance of the crown cap to the sensor is measured and evaluated.
In addition to the cap inspection, the sensor also detects if bottles are missing. And other errors on the crate can be detected, such as e.g. if bottles jut out in the crate even just a little, compared to the other bottles, due to for example broken glass at under the bottle. The EyeScan AT 3D is a laser triangulation sensor. This means that a laser is scanning the surface and a camera is capturing the height profile of the laser line.