Technological progress in laser ablation has made it the leading method for texturing materials such as ceramics, metals, glasses, and polymers.
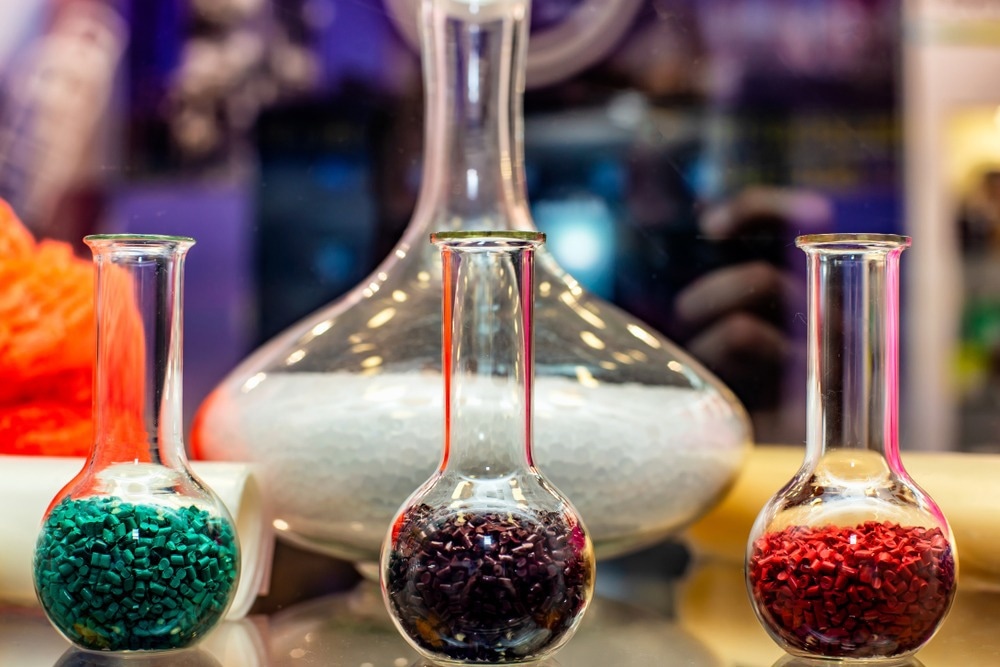
Image Credit: IU Liquid and water photo/Shutterstock.com
Creating micro or nanoscopic structures on materials has broad applications in many fields. Aside from engineering consumer products, chemical, medical and photonic industries reap many functional benefits from different design structures.
A variety of materials are used to uniquely indent and mold useful devices. For example, ceramics, metals and glasses have all been widely used. Polymers are another class of materials that have become a foundation for manufacturing consumer products.
What are Polymers?
Polymers are large molecules made of repeating sub-molecular or atomic structures. These can be naturally occurring macromolecules or synthesized in laboratories to serve a particular purpose.
A lot of everyday objects are made of polymers. For example, polythene is used in plastic bags and bottles. Crates and ropes used in industrial settings are made of polypropene. Infrastructure components such as water pipes and insulation on electricity cables are mostly composed of poly-chloroethene.
Polymers are also widely used in scientific technology such as optical waveguides, microfluidic channels and electronics.
The popularity of polymers lies in the physical properties that lend themselves to nanotexturing. Polymers are lightweight, highly resistive against corrosion, and have a low coefficient of friction, which leads to less wear when compared with other classes of materials.
Texturing Techniques in Polymers
Surfaces of polymers can be textured using several techniques. Micro-milling, hot embossing, laser-based lithography, mechanical texturing, electrochemical machining, and ion-beam etching are some of the methods in use. Laser ablation (LA) has superseded other methods as the most prominent technique as it is a non-contact procedure capable of creating higher-quality textures. LA is also low-cost and easier to implement.
Laser Ablation of Polymers
LA uses ultrashort laser pulses to remove materials from a substrate to create micro or nano features.
The first published report on LA was by Robert Cozzens of the Naval Research Laboratory in 1977. Since then, the use of LA has caught on in many different applications and the technology has advanced rapidly.
High-energy laser pulses can melt and vaporize polymers. Due to this capability, LA is an ideal approach to texture polymer surfaces.
A typical LA setup is shown in figure 1. An ultrashort pulsed laser beam is focused through a lens onto the surface of the polymer. The laser head or the stage on which the polymer substrate is mounted is capable of being translated in 2D. The full setup is automated so that the sequence of movements is uniform.
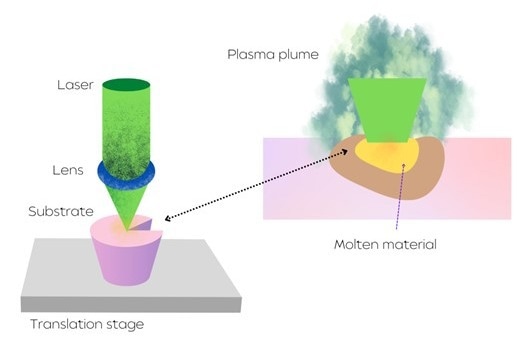
Figure 1: Optical set up for LA. Magnified image shows melting of the surface and the creation of plasma plumes. Image Credit: Ilamaran Sivarajah
When the polymer’s surface is irradiated by the laser beam, electrons in the substrate get excited.
The photon energy absorbed in this process generates heat within the polymer. The amount of heat produced in the substrate depends on the intensity of the laser beam and the thickness of the polymer.
As a result of the heat, the polymer surface around the laser spot begins to melt and vaporize. Consequently, the material is removed from the surface.
In the interaction region, materials transform from solid to gas, forming a plasma plume as shown in figure 1. The phase transition triggered by the laser is a chemical reaction. The process of ablation can occur due to chemical, thermal, or changes affected by a combination of both.
By scanning the lasers across the surface in the desired direction, a pattern can be textured on the polymer.
Alternatively, the laser can be fixed and the platform holding the polymer can be translated to accomplish the same feat.
Advancements in automation and control technology have assisted LA immensely.
Characteristics of the laser source have a major impact on the LA of polymers. Laser specifications such as wavelength, pulse width, repetition rate, and fluence are critical parameters.
The type of texturing required on the polymer determines the optimal laser features needed. Low repetition rate systems offer high pulse energies while lasers with short pulse durations have high peak powers. Fluence of a laser beam is the energy delivered per unit area of the laser spot.
Monochromaticity and pointing stability of the laser beam are also crucial for LA. Monochromaticity ensures that the laser beam’s wavelength is held constant for the duration of the procedure. Pointing stability describes the variation of the beam directionality over time.
Modern laser technology offers high performance in most of the laser parameters required for LA. Integrating lasers with control mechanisms has advanced the performance of LA.
The Future of Laser Technology for Polymer Texturing
LA has advanced rapidly with modern laser technology and control software.
Manufacturing processes have greatly benefited from fast processing times with high-quality textured polymers.
Continued development of highly efficient and accurate controlling technology will further improve LA.
Research efforts developing quantitative modeling to optimize the LA process from laser parameters to mechanical engineering will push surface texturing by LA in polymers and other fields to new heights.
References and Further Reading
Obilor, A.F., Pacella, M., Wilson, A. et al. Micro-texturing of polymer surfaces using lasers: a review. Int J Adv Manuf Technol 120, 103–135 (2022). https://doi.org/10.1007/s00170-022-08731-1
Sandeep Ravi-Kumar, Benjamin Lies, Xiao Zhang, Hao Lyu, Hantang Qin. Laser ablation of polymers: a review. Polymer International (2019) https://doi.org/10.1002/pi.5834
Robert F. Cozzens, Robert B. Fox. Infrared laser ablation of polymers. Polymer Engineering and Science (1978) https://doi.org/10.1002/pen.760181113
Disclaimer: The views expressed here are those of the author expressed in their private capacity and do not necessarily represent the views of AZoM.com Limited T/A AZoNetwork the owner and operator of this website. This disclaimer forms part of the Terms and conditions of use of this website.