A recent study used X-ray diffraction (XRD) to watch chemical reactions taking place under mechanical stresses as materials were crushed in a tiny grinding mill. The new information obtained with XRD will help the emerging field of mechanochemistry to realize its full potential – which may introduce greener manufacturing methods for numerous synthetic industrial materials.
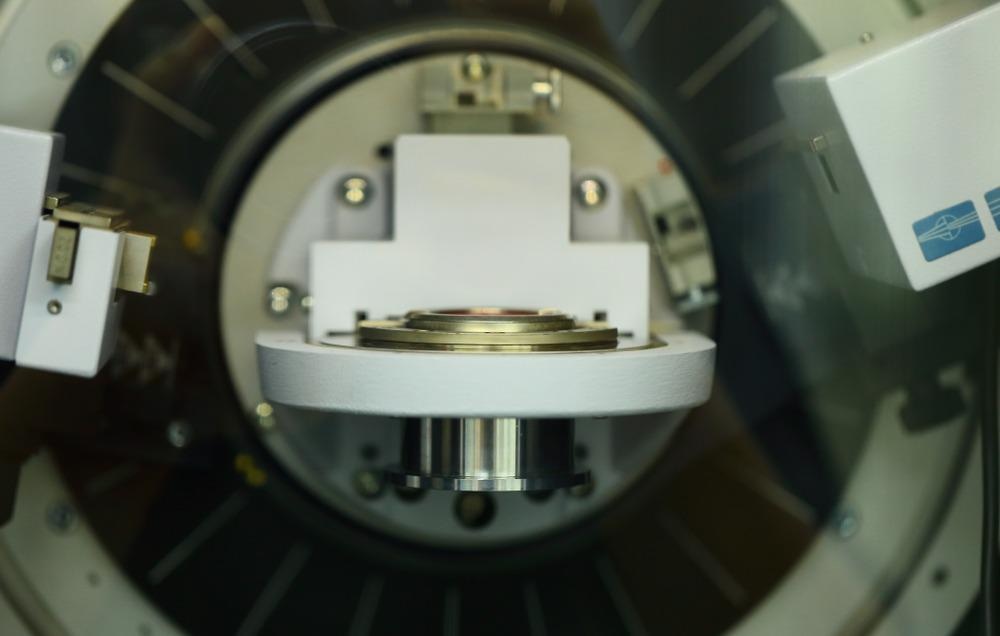
Image Credit: AgriTech/Shutterstock.com
What is Mechanochemistry?
The field of mechanochemistry – the science of creating chemical reactions and chemically reactive materials with mechanical processes – is heralded as a greener approach to materials synthesis, as it removes harmful bulk solvents used for conventional synthetic materials manufacturing.
While modern mechanochemistry approaches are at the cutting edge of materials science, chemistry, and physics, mechanochemical phenomena have been manipulated by humans since our very first interactions with technology.
Our most ancient technology, fire, is an example of mechanochemistry. Fires are lit by rubbing pieces of wood against one another to create friction and heat, or by hitting steel against flint to bring about a spark (a particle of pyrophoric metal that spontaneously combusts).
Modern mechanochemical techniques involve complex mechanisms that differ from typical photochemical or thermal mechanisms. Among the most widely used of these modern techniques is ball milling, through which researchers can apply consistent mechanical force to materials to create chemical transformations or processes.
Mechanochemistry has applications in a range of advanced manufacturing and technology sectors. Metallic nanoparticles, catalysts, magnets, γ‐graphyne, metal iodates, nickel-vanadium carbide, and molybdenum-vanadium carbide nanocomposite powders have been synthesized using mechanochemical techniques so far.
Traditionally, industrial chemistry relies on dissolving, heating, and stirring products in solvents. The large number of solvents used in these processes both consume a lot of energy in their production and manufacture and heavily pollute the local environment and water sources.
Mechanochemistry can eliminate the need for solvents by creating industrial chemistry products in mechanical processes. This has led some researchers to promote it as a greener alternative to traditional manufacturing processes.
Modern mechanochemical transformations were studied using time-resolved in situ (TRIS) monitoring techniques. However, TRIS provides only limited data quality, which in turn has limited our understanding of mechanochemical processes.
New Approach to Mechanochemistry with XRD
A new study increased the quality of data we have on mechanochemical processes by using XRD alongside TRIS for monitoring and recommends that others use this new technique to identify and study more mechanochemical phenomena in the future.
The authors tested their technique with a mechanochemical milling process to make new chemical compounds and materials. They found new data on how various materials’ crystals were formed and structured.
The study was led by University of Cambridge (UK) scientists and published in Nature Communications in 2021.
The researchers already knew how the kinetics in the mechanochemical processes would affect the newly formed materials from theoretical analysis and prior experimental work. But the new technique combining XRD with TRIS gave them a new level of detail that had not been previously possible.
It is important to observe mechanochemical reactions in real-time. This enables researchers to identify dynamic chemical processes and events taking place in the materials.
Observation must also be done with as little disturbance as possible because chemical processes continue to occur after the mechanical catalyst has stopped moving. This is why TRIS is commonly used for mechanochemical analysis.
To improve on the grainy, low-resolution image data provided by the TRIS analysis, Cambridge researchers modified the typical TRIS workflow to include XRD.
To do this, they reduced the sizes of the mills and the sample down significantly: mills are typically a few hundred milligrams, this one was less than ten milligrams. This enabled the team to capture information about the size and structure of crystals as they formed using XRD.
Working at a smaller scale also enabled the team to study safer quantities of toxic substances and smaller amounts of expensive materials. The team realized after the experiment that this would also open up the possibility of mechanochemical research to more areas of chemistry and materials science.
Scientists determined that accurate phase compositions could be obtained with their XRD technique using small sample loads. While phase compositions can also be obtained by ex-situ measurement, the XRD technique was able to simultaneously determine microstructural parameters such as the crystals’ size and microstrain with a high degree of confidence.
The researchers used the XRD set up to study a wide range of mechanochemical reactions. They tested it with organic and inorganic materials, as well metal organics, to show that it can be used to tackle problems in numerous and diverse industrial sectors.
The XRD strategy can be applied to all chemistries immediately and with significant effect in terms of data on mechanochemistry. As well as becoming the standard for mechanochemical investigations, the technique’s developers hope that it will enable new avenues of research as well. It allows for faster kinetics and will be central to many new investigations in the future.
References and Further Reading
Baláž, P., et al. (2013). Hallmarks of mechanochemistry: from nanoparticles to technology. Chemical Society Reviews. Available at: https://doi.org/10.1039/C3CS35468G.
Lampronti, G. I., et al. (2021). Changing the game of time resolved X-ray diffraction on the mechanochemistry playground by downsizing. Nature Communications. Available at: https://doi.org/10.1038/s41467-021-26264-1.
Miniature grinding mill closes in on the details of 'green' chemical reactions. (2021) Nanowerk. Available at: https://www.nanowerk.com/nanotechnology-news2/newsid=59294.php.
Munnings, C., S. P. S. Badwal, and D. Fini (2014). Spontaneous stress-induced oxidation of Ce ions in Gd-doped ceria at room temperature. Ionics. Available at: https://doi.org/10.1007/s11581-014-1079-2.
Salmatonidis, A., et al. (2018). Chemical Cross-Linking of Anatase Nanoparticle Thin Films for Enhanced Mechanical Properties. Langmuir. Available at: https://doi.org/10.1021/acs.langmuir.8b00479.
Disclaimer: The views expressed here are those of the author expressed in their private capacity and do not necessarily represent the views of AZoM.com Limited T/A AZoNetwork the owner and operator of this website. This disclaimer forms part of the Terms and conditions of use of this website.