Global agricultural, construction and forestry machinery manufacturer John Deere recently announced a partnership with historic technology firm Intel that will develop a fresh crop of artificial intelligence (AI) solutions for a key challenge in industrial welding: porosity. Advanced machine vision systems are integral to industry digitization and automation projects such as John Deere’s.
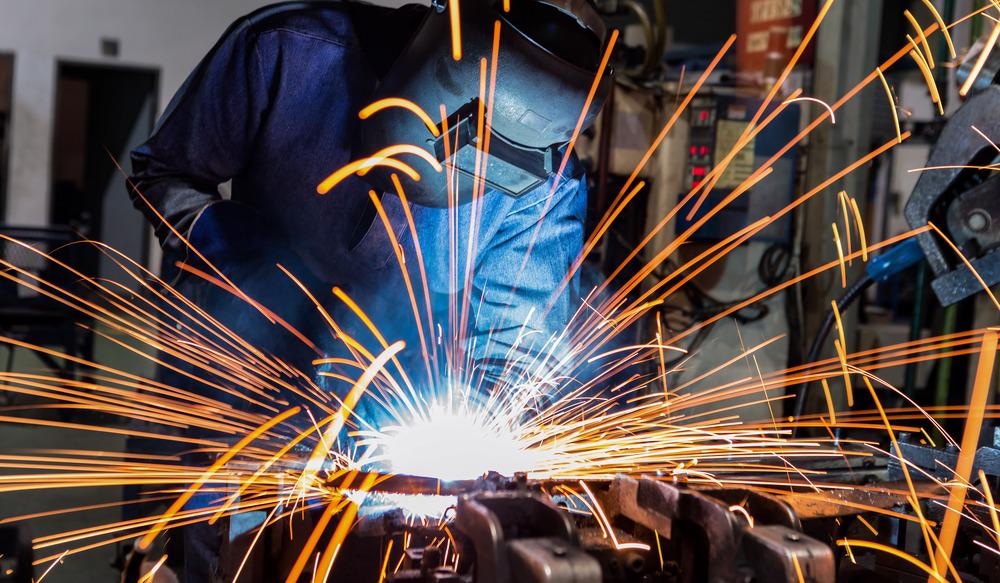
Image Credit: Factory_Easy/Shutterstock.com
The Problem of Porosity
Welding porosity is an undesirable effect of welding metal together, in which cavities form in the material. External gasses are trapped in the bead of molten metal which solidifies around the gas.
Porosity makes the weld weaker. At best, weld porosity will mean the weld needs some reworking before it is suitable for use; this cuts into the production schedule. At worst, manufacturers may have to discard the whole defective part as scrap. In either case, weld porosity negatively affects the manufacturer’s bottom line.
It is also not straightforward to detect porosity, especially in an industrial manufacturing environment. Trained weld engineers can see and hear porosity with a simple inspection, but this skill set is currently in short supply. The challenges of noise, vibrations, and poor air quality are all compounding factors affecting the difficulty of detection in heavy-duty equipment factories.
Automated Systems Used to Detect Porosity
The manufacturing industry is typically the earliest to adopt new industrial methods and processes, and it is no different when it comes to automation. Automation has been present in manufacturing since the earliest factories, and today’s industry is strongly invested in the advanced robotics, sensors, transportation, and AI required to make automation work.
Machinery and equipment manufacturers have introduced some automated monitoring systems to tackle the problem of porosity in industrial welding. However, these have so far proven relatively unsuccessful. They have tended toward a high proportion of false positives, stalling production and increasing materials outlay with wastage.
It has for some time been extremely difficult to make acceptable machine vision systems for welding applications. This is due to the extremely harsh operating environments for industrial welders (a lot of smoke, sparks flying) and the extremely high energy (emitted in light and heat) produced by the welding process.
John Deere’s Partnership with Intel
Overcoming these challenges, John Deere and Intel worked together with other partners to develop an AI system with a camera located close to weld. This will provide imaging capability better than what could be achieved with the human eye.
Intel will use its OpenVINO (Visual Inference and Neural Network Optimization) toolkit in the AI software. This code examines the video data it receives frame by frame to find any defects. When the AI finds a defect, it immediately switches off the welding robot to enable a human technician to fix the problem early on.
The system developed by John Deere and Intel will be end-to-end integrated with the welding equipment manufacturers are using today. This means that current welding operations could immediately adopt it, as well as process engineers and designers developing future automated industrial manufacturing systems.
Multiple streams of footage combine in the system, capable of handling large quantities of raw data and quickly analyzing it for defects. Machine learning is extended to edge devices in the system, to continually increase the algorithms’ speed and accuracy.
Independent of third-party power supply or even the weld robot model itself, the system developed by Intel and John Deere represents a scalable solution that can be widely applied for many industrial welding operations. Intel and John Deere reported detection accuracy rates of over 97% from the pilot project with their new automated porosity identification system.
Next Steps for John Deere
John Deere is very experienced in tackling weld quality challenges. Welding is among the company’s key business and manufacturing activities, literally tying its famous products together and protecting its reputation for durability in ruggedized environments.
The company’s embrace of AI (and the strategic partnership with Intel) marks it out as a key player for the future of heavy-duty machinery manufacturing. The company increasingly utilizes AI and machine vision systems for quality inspection and control. Now, engineers can detect issues as they arise, enabling quick decision-making for the manufacturing environment.
Automating quality assurance processes improves quality and manufacturing speeds simultaneously. John Deere expects its development and use of AI and machine vision for QA will provide the company with a competitive edge over manufacturers slower to adopt the latest technology.
Beyond Porosity: Benefits of Machine Vision for Welding
Advanced machine vision is needed to put welding robots and cobots (robots deployed alongside humans) to work reliably and at scale. The extremely bright light from a welding arc blinds conventional camera systems just as it does the human eye, so specialist equipment is required.
Cavitar produces welding cameras that can clearly image welding processes despite the bright light and heat emitted. Their range of products include compact cameras and comprehensive vision systems with laser illumination.
Machine vision systems can significantly improve on industrial welding operations, ultimately representing a return on investment for some manufacturers. Image analysis and automation such as porosity identification require effective camera sensors, but imaging also helps human and AI operators to optimize welding processes in real time.
References and Further Reading
Boles, C. (2021) Deere turns to AI to solve welding porosity issues. SME.org. Available at: https://www.sme.org/technologies/articles/2021/september/deere-turns-to-ai-to-solve-welding-porosity-issues/.
The Advent of AI / Robotics in the Welding Industry. Philadelphia Technician Training Institute. Available at: https://ptt.edu/blog/the-advent-of-ai-robotics-in-the-welding-industry/.
Welding Cameras for Visualization of Welding Processes. AZO Optics. Available at: https://www.azooptics.com/optics-equipment-details.aspx?EquipID=1245.
Disclaimer: The views expressed here are those of the author expressed in their private capacity and do not necessarily represent the views of AZoM.com Limited T/A AZoNetwork the owner and operator of this website. This disclaimer forms part of the Terms and conditions of use of this website.