Impact welding is a procedure which establishes metallurgical bonds, even between metals that are not similar. Electromagnetic pulse welding has been produced as one technique for impact welding.
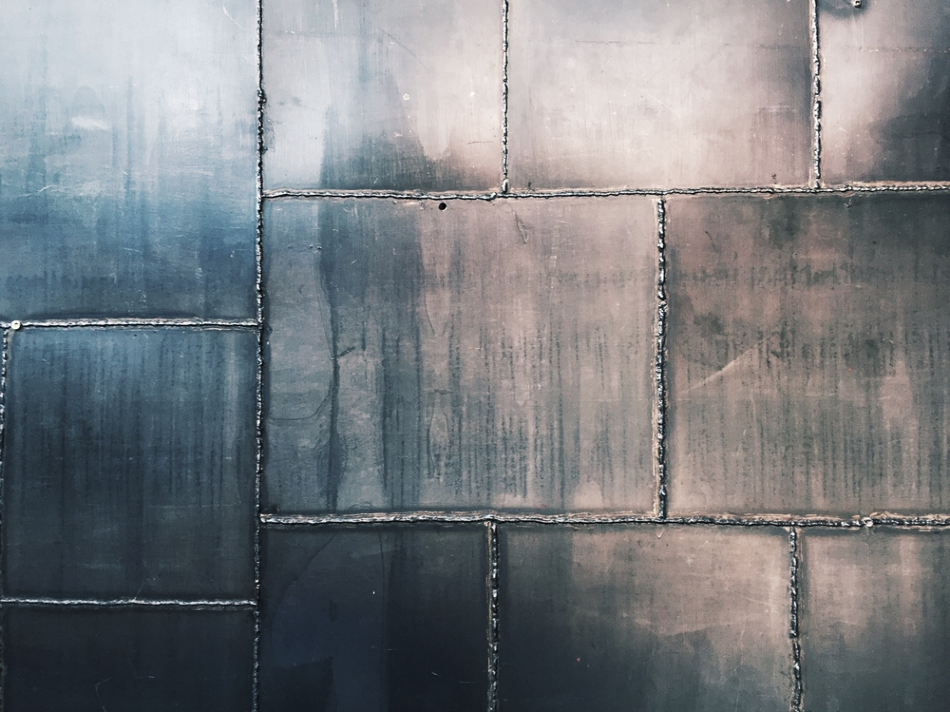
Image Credit: Shutterstock/HALCHYNSKA KSENIIA
Its energy is provided from charged high-voltage capacitors. A coil generates the accelerating force on the workpiece and the current is controlled by discharging the capacitors.
The key applications of electromagnetic pulse welding are the gas-tight sealing of high-pressure containers, low-ohmic joins between copper to aluminum for electromobility, and the construction of hybrid space frames.
The joints created with impact welding are very hard-wearing as the joint region is not debilitated by thermal influences but manifests fine grains.
In Figure 1, the key mechanisms are described: One workpiece must impact another at velocities in the range of around 250 m/s and higher. The impact must happen under a specific angle of impact.
This results in a point of collision (or line) moving across the surface. Characteristic to this process is a bright flash occurring at the moment of impact.
The metallically pure surfaces are then joined together by the sheer pressure of the impact, which lastly establishes the metallurgical joint.
.jpg)
Figure 1. Schematic illustration of impact welding.
Experimental Configuration
A special test rig has been created at the PtU for the basic investigations. It mitigates the limitations of electromagnetic pulse welding and explosion welding by welding and colliding flat sheets mechanically.
The buildup comprises of two rotors which are each controlled by one motor. Each rotor contains an aluminum tube with a welding specimen fixed at one side of it. Figure 2 presents the test rig without its housing.
.jpg)
Figure 2. Left: Test rig without housing. Right: Rotors with specimens in collision position.
Each rotor has an equal sense of rotation so the velocity of the specimens combine when they make contact in the center. When the specimens are effectively welded, they rip off their clamped rest with the assistance of a preselected breaking point. The clamped parts and the welded specimens are displayed in Figure 3.
.jpg)
Figure 3. Welded specimens (center) with the clamped parts.
Imaging Setup
As the joint formation and the real-life impact occur in only a few microseconds, the procedure is difficult to record with a traditional high-speed camera. For these research investigations, an image intensifier camera is utilized.
This allows frame delays and exposure times in the range of nanoseconds at still exceptional spatial resolutions of more than 1000 pixels.
There are two further obstacles when filming the impact along with the high speeds. A bright flash shields the actual joint area during impact. Its creation will be outlined in the next section of the article.
The second challenge is precise triggering as the camera method does not enable pre-triggering. The precise measurement of the momentary angle is almost impossible because of the fast turning rotors.
The bright process glare can be weakened by a method which is similarly employed when traditional welding processes are analyzed.
As the glare is normally white, it can be argued that its intensity is spread almost consistently across all wavelengths that are visible. The source of light that is essential for high-speed and high-quality images only generates light in a small wavelength range.
Its intensity is much stronger than the process glare, even if the latter seems to be brighter to the human eye. Figure 4 displays this issue.
.jpg)
Figure 4. Emitted wavelength range of the light source and the wavelength distribution of the process light.
An optical bandpass filter is mounted to the camera along with the special light source in order to reduce all other wavelengths.
The CAVILUX Smart laser illumination system with a nominal wavelength of 640 nm ± 10 nm is utilized in the analysis along with a filter for 640 nm ± 5 nm.
The laser light is simple to handle in comparison as the light can be seen and the generated beam itself is neither collimated or coherent which stops speckling.
The laser pulses are coordinated with the camera as their length is restricted to a few microseconds. This is because of the limited duty cycle which reduces a constant illumination. Using both rotors as a kind of switch for the trigger circuit is how triggering is created.
Figure 5 outlines the procedure in two independent experiments instantly after the finished impact, both with and without a bandpass filter. It can be obviously seen that it is nearly impossible to analyze the impact in detail without the filter.
.jpg)
Figure 5. Propagation of the jet 20 µs after the impact with (left) and without (right) optical bandpass filter.
.jpg)
Figure 6. Image series taken from the side the process with 2 mm aluminum plates at 3 Mio fps.
.jpg)
Figure 7. Image series taken from the side of the process with 0.74 mm steel plates at 2 Mio fps. The process creates also shockwaves which can be seen in the images.
Jet Formation and Process Glare
A popular explanation for the process glare is that it is a result of the jet. The jet consists of parent material, not only of oxides.
The argument suggests that this parent material burns when it is emitted which generates the intense light. It is widely agreed at the same time that high temperatures or even melting do not happen during the welding and impact process.
An adequate source of energy which can start the oxidation should actually not exist. The electromagnetic pulse welding procedure is evaluated under various atmospheres in order to analyze jetting and glare in further detail.
The full housing of the test rig has a volume of around 1 m³ and it is not gas-tight. The coil is housed in an acrylic glass box, which is filled with an inert welding gas for the experiments.
When the inert gas completely fills the enclosure, the pulse generator is charged and the weld is established after just a few seconds.
The next images demonstrate the welding of two aluminum sheets with a thickness of 2 mm by a peak current of 300 kA at 20 kHz. Figure 8 presents the welding procedure with the inert gas atmosphere (left) and with the surrounding air (right).
The inert gas does not only extensively reduce the generated light, but also greatly weakens the emitted pressure wave throughout the impact.
.jpg)
Figure 8. Electromagnetic pulse welding of two aluminum sheets with (left) and without (right) inert gas atmosphere.
Welds between two copper sheets (Cu-ETP, with a thickness of 1 mm) present a different behavior. Neither the pressure wave nor the light emission is strongly affected by the atmosphere surrounding them.
It is similar to aluminum welds with inert gas in both cases. These experimental results indicate that an oxidation happens throughout the impact. Aluminum burns with a bright white flame and the oxidation is a strongly exothermic reaction.
As displayed in Figure 5, the emitted jet appears like a dust cloud. If this dust does not only comprise of superficial oxides but also of pure aluminum from the base material, a large surface is produced.
If a sufficient source of energy is available, then a powerful exothermic reaction can occur.
This argument is supported by the investigations with the test rig. The strength of the jet and glare are almost the same as shown in Figure 8. This suggests that jetting and glare are the same event, or at least correlate closely.
.jpg)
Figure 9. Electromagnetic pulse welding of two aluminum sheets with (left) and without (right) inert gas atmosphere.
The auto ignition temperature of aluminum is heavily related to the particle size.
Research completed in this field demonstrates that the auto ignition of aluminum powder with a particle size of less than 10 µm can already occur at around 600 °C.
As burning aluminum can even split molecules of water, a hydrogen explosion as a result of the atmospheric humidity may occur as well. In contrast, copper does not burn, which explains why the surrounding environment does not affect the light emission.
Conclusions
Due to ultra-high-speed imaging achieved using a CAVILUX Smart laser illumination and an image intensifier camera, an investigation of jet formation and process glare in electromagnetic pulse welding was possible.
The laser illumination provided the accurate removal of thermal light created by the procedure. This allowed for a closer view behind the bright process light. With short pulse duration and back illumination, the observation of shockwaves is also possible.
The high image quality allowed theoretical models to be validated, along with the research in this field.
Acknowledgments
Produced from materials originally authored by Christian Pabst from the Darmstadt University of Technology – Institute for Production Engineering and Forming Machines (PtU).
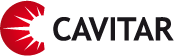
This information has been sourced, reviewed and adapted from materials provided by Cavitar.
For more information on this source, please visit Cavitar.