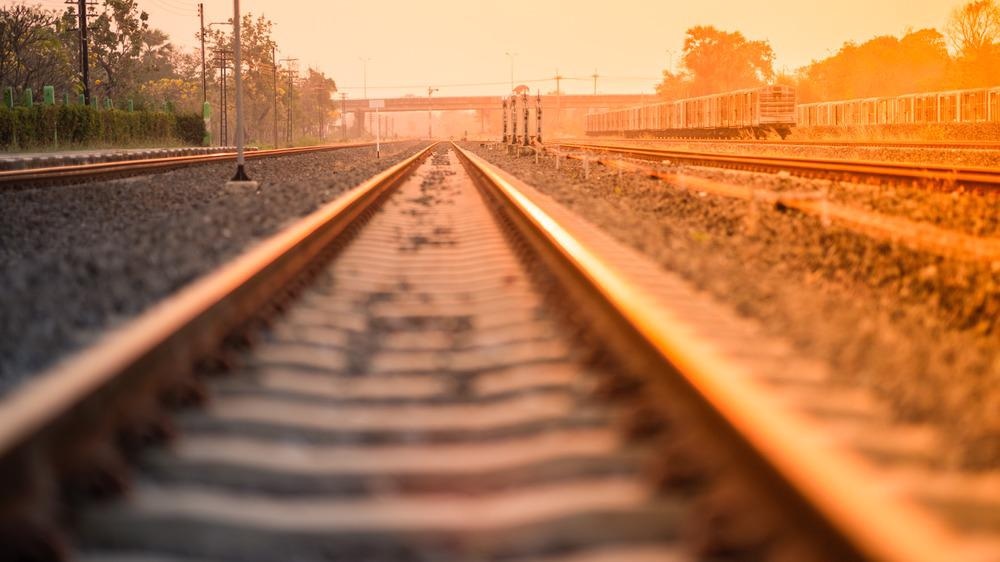
Image Credit: Torychemistry/Shutterstock.com
Rail tracks are vulnerable to defects caused by rolling contact fatigue such as head checks and squats. These defects can be expensive and jeopardize rail operations and the safety of travel. While numerous techniques have been established to analyze such faults, they are not without their drawbacks. The rail industry needs a reliable and effective non-destructive method of testing rails. Now, scientists have created a novel technique using inductive thermography and infrared cameras which could be developed into an automated method of rail analysis.
Why are Non-Destructive Analytical Methods Required for Testing Rail Tracks?
Rolling contact fatigue (RCF) leads to common defects on rail tracks that can lead to operational issues and safety hazards. Head checks and squats are the most frequently arising defects. Head checks are caused by high-contact stresses between the gauge corner of the rail and the train’s wheel. This can lead to visible surface cracks, known as head checks, that appear at regular intervals. Squats occur when small bits of hard material become trapped between the rail and the wheel, forcing a crack to appear. This crack then grows in the direction of the surface layer, forming a bump known as a squat. Both common defects can be costly and dangerous to train operations.
Railways are currently inspected via ultrasound, eddy currents, and visual inspections to detect and characterize rail defects. However, there are drawbacks to these methods. Ultrasound, for example, requires water as a coupling medium and visual inspections are vulnerable to human error. While scientists have developed new ultrasound techniques that do not require a coupling medium, these methods have not been widely adopted by the industry.
There is a need for new, reliable, and effective non-destructive methods of analyzing rail tracks that can run testing on-site. In recent years, a novel method of inductive thermography has been established. Scientists believe it has potential for use in automated rail inspection. The technique uses inductive thermography and infrared cameras to inspect rail surfaces and just below to detect and characterize defects.
What is Inductive Thermography and How is it Used to Test Rail Tracks?
Inductive thermography is a non-destructive analytical method where the sample is heated using a short heating pulse. An infrared (IR) camera is then used to measure temperature changes on the surface.
In a recent study, scientists in Austria heated samples with a pulse in the range of 0.1–1s. Because any cracks in the rail, no matter how small, cause disruptions to the eddy current which is induced by means of a high-frequency magnetic field applied to the sample’s surface, the infrared camera can highlight where these cracks are located, making them ‘visible’ through the differences in heat diffusion.
The team analyzed several different parts of rail pieces using this method, all of which had head checks or squats. With the aim of testing the process for analyzing longer pieces of the track, even, the entire track, the team inspected lengths of track measuring 1 meter in length via two methodologies. First, the longer track segments were inspected with a stop-and-go technique, where images of the track surface were taken and combined to create a panorama image. The second technique involved scanning the track surface over one continuous movement of the rail.
What Did the Results Say About Using Infrared Cameras in Rail Inspections?
Overall, the data demonstrated the efficacy of the inductive thermography in conjunction with infrared cameras at detecting and characterizing common rail defaults (head checks and squats). The results not only demonstrated that these defaults were successfully detected but also gave insights as to factors that impact the analysis, such as the type of material tested, and the potential resolution of the method.
The results showed that head checks could be reliably determined via infrared imagery and that the surface angle of head checks could automatically be computed, offering in-depth detail on the nature of the fault. The results revealed that squats could also be reliably detected by inductive thermography, with shallow cracks that characterize squats appearing visibly via infrared images.
Analysis of the data collected via the two distinct methods of inspecting longer pieces of track concluded that the stop-and-go method may be more advantageous. The results showed that this method resulted in better contract than the scanning technique and that as a result head checks could be more accurately located and characterized in higher quality. However, the stop-and-go method was slower than the scanning method and more research is needed to develop and optimize the technique before it is ready to be adopted on a wide scale by the rail industry.
References and Further Reading
Netzelmann, U., Walle, G., Lugin, S., Ehlen, A., Bessert, S. and Valeske, B., 2016. Induction thermography: principle, applications and first steps towards standardisation. Quantitative InfraRed Thermography Journal, 13(2), pp.170-181. https://www.tandfonline.com/doi/abs/10.1080/17686733.2016.1145842
Stock, R., Kubin, W., Daves, W. and Six, K., 2019. Advanced maintenance strategies for improved squat mitigation. Wear, 436-437, p.203034. https://www.sciencedirect.com/science/article/abs/pii/S0043164819301048
Tuschl, C., Oswald-Tranta, B. and Eck, S., 2021. Inductive Thermography as Non-Destructive Testing for Railway Rails. Applied Sciences, 11(3), p.1003. https://www.mdpi.com/2076-3417/11/3/1003/htm
Disclaimer: The views expressed here are those of the author expressed in their private capacity and do not necessarily represent the views of AZoM.com Limited T/A AZoNetwork the owner and operator of this website. This disclaimer forms part of the Terms and conditions of use of this website.