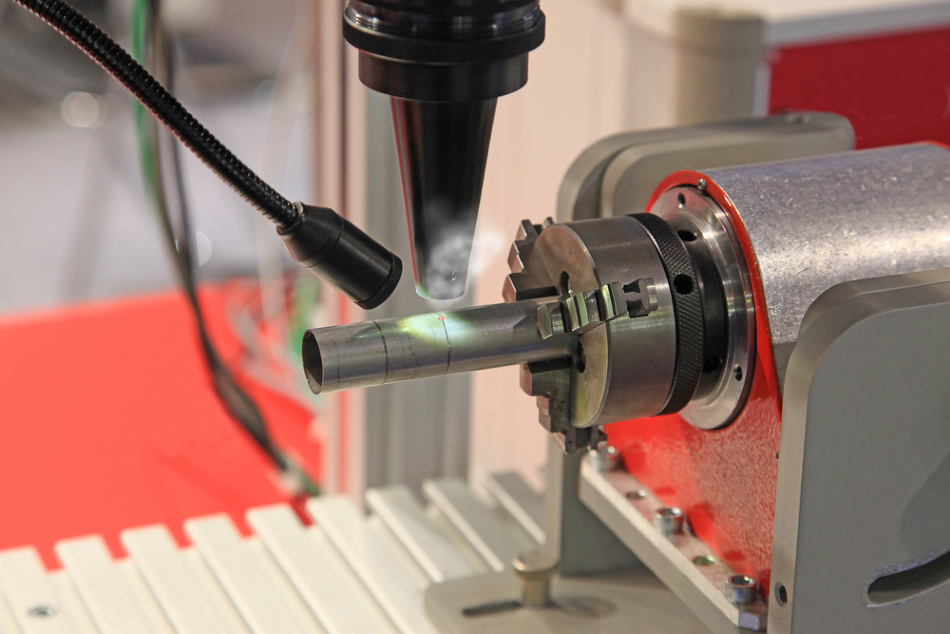
Image Credit: sspopov/Shutterstock.com
Laser beam welding and electron beam welding both have individual benefits that they bring to the manufacturing industry. However, the current commonly held view is that combining the two welding methods is the best-case scenario, resulting in a streamlined manufacturing process the likes of which is not achievable by using a single method alone.
The impact of streamlining is particularly notable when complex geometries are required to be fused together, or the needs of superior weld metallurgy need to be met.
When the design of a product includes features that require both laser beam welding and electron beam welding processes, combining them into a single facility improves the efficiency of the production process, streamlining the entire manufacturing process by eliminating the need to send a component to each welder separately.
Products that commonly benefit from this combination of technologies include medical devices, sensors, and products that have a sealed vacuum within their finished structure.
Combining the welding processes can streamline the production when the size of end product assembly exceeds the electron beam welding chamber, when a component (a liquid) that is incompatible with vacuum processing is included in the finished product, or when the weld is non-critical or shallow.
What is Laser Beam Welding?
There are two methods of laser beam welding. The first uses a continuous wave, where the output of the beam is controlled continuously. The second technique uses a pulsed beam of photons where the system is programmed to produce a series of laser pulses. Welds are created by overlapping individual pulses, allowing for welds to be successfully created in heat-sensitive materials due to the brief cooling period in-between pulses.
What is Electron Beam Welding?
The electron beam welding process welds together refractory and dissimilar metals that cannot be joined using other methods. The product is exposed to a focused stream of high-speed electrons, the kinetic energy of which converts into heat energy, initiating fusion of the target materials.
Combining Both Methods to Streamline Manufacturing
Nowadays, many components require the methods of both electron welds and laser welds. However, conducting these processes separately adds stages to the production process, slowing it down. Therefore, performing both welds simultaneously drastically cuts down on production time and allows manufacturers to benefit from the advantages of both systems. Many manufacturers produce a number of components, all of different sizes, materials, shapes, and functions. Therefore, one welding method will not be suitable for all components.
In some cases, the welding scenario will call for a laser beam weld due to the component being large in size, or because manufacturers want to benefit from the use of simpler tools, or because the component is to be created at low cost without sacrificing quality.
On the other hand, electron beam welding offers different advantages and is suitable for different welding scenarios. To begin with, the electron beam offers a higher quality weld, and for certain products, it is worth going through the process to achieve a higher quality finish.
What’s more, specific materials benefit from being welded in the vacuum environment, like titanium and nickel alloys, for example. Finally, deep welds are often produced better with electron beams as opposed to laser beams, so in these scenarios, it is appropriate to select the electron system.
Overall, not all products will require the same kind of welding as other products and neither will all welds on an individual component. Combining the two processes in the same space therefore cuts time and adds to the quality of the finished product.
References and Further Reading
Disclaimer: The views expressed here are those of the author expressed in their private capacity and do not necessarily represent the views of AZoM.com Limited T/A AZoNetwork the owner and operator of this website. This disclaimer forms part of the Terms and conditions of use of this website.