In an article published in Polymers, researchers described a technique for minimizing thermal residual strain in a metal-CFRP-metal hybrid tube (MCMHT). The suggested axial preload tool demonstrated two means to minimize the thermal residual strain during the co-cure bonding procedure. One way proposed was pre-stretching the one-direction carbon fiber reinforced polymer (CFRP) layers. While the other suggested pre-compressing the metal layers.
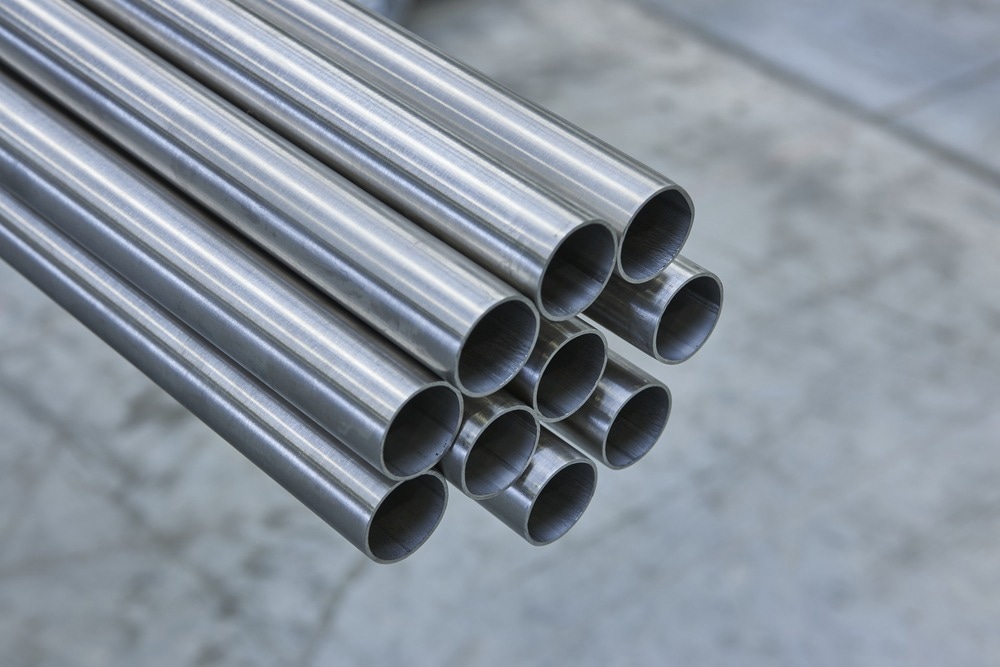
Study: Reduction of Thermal Residual Strain in a Metal-CFRP-Metal Hybrid Tube Using an Axial Preload Tool Monitored through Optical Fiber Sensors. Image Credit: united photo studio/Shutterstock.com
The authors presented an online measurement method using integrated optical fiber Bragg grating (FBG) sensors. The classical lamination theory was used to estimate thermal residual stress under the premise of planar stress. Theoretical calculations and measurement findings of the study demonstrated good agreement.
Tests were performed on the dynamic characteristic of the metal-CFRP-metal hybrid tube. The findings revealed that reducing residual strain enhanced the natural frequency of the metal-CFRP-metal hybrid tube but decreased its damping capacity. Such an observation suggested that this axial preload tool could change the intrinsic dynamic characteristic of the metal-composite hybrid structure.
Understanding the Need and Make-Up of a Metal-Composite Hybrid Structure
A sandwich structure is a unique metal-composite hybrid structure that combines two lightweight core materials such as honeycomb, foam, balsa, fiber-reinforced polymer (FRP) composites, etc., with two thin, rigid, strong faces, including FRP composites or metal. It creates an interdisciplinary idea that blends functional design, material science, integrated manufacturing, and intelligent sensing to fulfill the high-quality demands of contemporary industry.
The rail transportation, automotive, aerospace, and marine industries may benefit from a three-layered metal-FRP-metal sandwich construction's high strength, lightweight, noise, and vibration reduction capabilities. The desirable qualities of FRP composites, including their low weight, high specific strength, strong damping capacity, and tailorability, are combined with the better durability of metals in this hybrid metal-composite structure.
Studies on the connection performance of the metal parts and FRP composites, impacting resistance, mechanical properties, durability, energy harvesting, machinability, etc., are of great interest in theoretical and experimental research.
Due to the challenging construction, most research is done on plate and beam structures, with only a small number of papers reporting on circular tubes with metal-FRP walls and square tubes with metal-FRP-metal sandwich walls.
A few studies have briefly discussed the thermal residual strain in a metal-composite hybrid structure. Due to the complexity of structural elements such as the metal-CFRP-metal hybrid tube, this essential issue of residual strain still needs to be understood and studied further.
A metal-composite hybrid structure inherently develops thermal residual strain throughout the production process. The (i) discrepancies between the coefficients of thermal expansion (CTE) of the metal layers and the FRP, (ii) the elastic properties, (iii) the interaction between the tool and the component, and (iv) the cure cycle are the most crucial manufacturing process variables.
Thermal residual strain results in several problems in a metal-composite hybrid structure, including transverse cracking and delamination. The residual strain harms the flexural stiffness, natural frequencies, fatigue performance, and dimensional precision of the metal-composite hybrid structure.
In this work, the authors proposed and fabricated the metal-CFRP-metal hybrid tube, consisting of sandwich walls made of unidirectional metal-composite hybrid structure core and steel skins. The axial preload tool was suggested to pre-compress the metal layers or pre-stretch the metal-composite hybrid structure layers, minimizing the thermal residual strain during the co-cure bonding process.
Based on the conventional lamination theory, an analytical model for evaluating thermal residual strain was provided. The inbuilt FBG optical fiber sensors monitored the thermal residual stress in real-time. The findings of the modal testing demonstrated that the suggested axial preload tool changed the inherent dynamic characteristic of the metal-composite hybrid structure.
Experimental Investigations
The metal-CFRP-metal hybrid tube, with measurements of 50 ´ 50 ´ 400 mm, was made up of two orthogonal steel plates, a square sheet of unidirectional CFRP core, and an interior steel tube. In this paper, two metal-CFRP-metal hybrid tube structures were built, one of which had a 4 mm pre-stretch in the CFRP layers.
The high-low temperature oven was filled with the two metal-CFRP-metal hybrid tube structures. Each metal-CFRP-metal hybrid tube contained a typical K-type thermocouple attached to its surface with thermally conductive adhesive. The manufacturer's suggested cure cycle was utilized to fabricate the co-cure bonding of the metal-CFRP-metal hybrid tube with the axial preload tool. Each metal-CFRP-metal hybrid tube was then cooled to room temperature.
According to theoretical calculations, temperature and the axial strain showed a proportional relationship with variations in FBG wavelength. A single FBG could not prevent strain-temperature cross-sensitivity since temperature and strain caused a Bragg wavelength shift. This study controlled FBG cross-sensitivity by embedding two different FBG optical fiber sensors into a structure.
The dynamic characteristic of the metal-CFRP-metal hybrid tube with various thermal residual strain states were investigated via modal testing under vibrational excitation. The metal-CFRP-metal hybrid tube with pre-stretching was suspended per the experimental apparatus for emulating the free-free boundary. Finally, the metal-CFRP-metal hybrid tube was subjected to an identical experiment without pre-stretching for comparison.
Real-time FBG optical fiber sensors detected temperatures and strains simultaneously during the co-cure bonding process. The findings showed consistent residual strain and temperature measurements for the metal-CFRP-metal hybrid tube with and without pre-stretching.
Axial Preload Tool and the Future of Residual Strain Reduction
This paper suggested the axial preload tool to pre-compress the metal layers or pre-stretch the CFRP layers to minimize the thermal residual strain during the co-cure bonding process.
A metal-composite hybrid structure also presented residual strain determination using embedded optical fiber sensors. Finally, results for thermal residual strain from FBG optical fiber sensors were contrasted with those from theoretical computations.
The dynamic characteristic of the metal-CFRP-metal hybrid tube under various residual strain situations were contrasted. Based on the multiplexing ability of FBG sensing technology, the embedded FBG optical fiber sensors could be used for future studies to monitor the structural health of a metal-composite hybrid structure in real time. For instance, overall stiffness could be reduced by damage such as microcracks, interface delamination, or matrix crushing in polymer materials. The incorporated FBG optical fiber sensors array helped determine the damage's origin, extent, and placement.
Reference
Li, Z., Ke, W., Liu, M., Zhou, Y. (2022) Reduction of Thermal Residual Strain in a Metal-CFRP-Metal Hybrid Tube Using an Axial Preload Tool Monitored through Optical Fiber Sensors. Polymers, 14(20), 4368. https://www.mdpi.com/2073-4360/14/20/4368/htm
Disclaimer: The views expressed here are those of the author expressed in their private capacity and do not necessarily represent the views of AZoM.com Limited T/A AZoNetwork the owner and operator of this website. This disclaimer forms part of the Terms and conditions of use of this website.