In a study published in Lubricants, researchers investigated the effect of surface roughness on friction and wear performances of laser-induced graphene films fabricated on mirror-polished and rough silicon substrates. This study also discusses laser-induced graphene film's potential as a solid lubricant due to its low-cost, large-scale producibility.
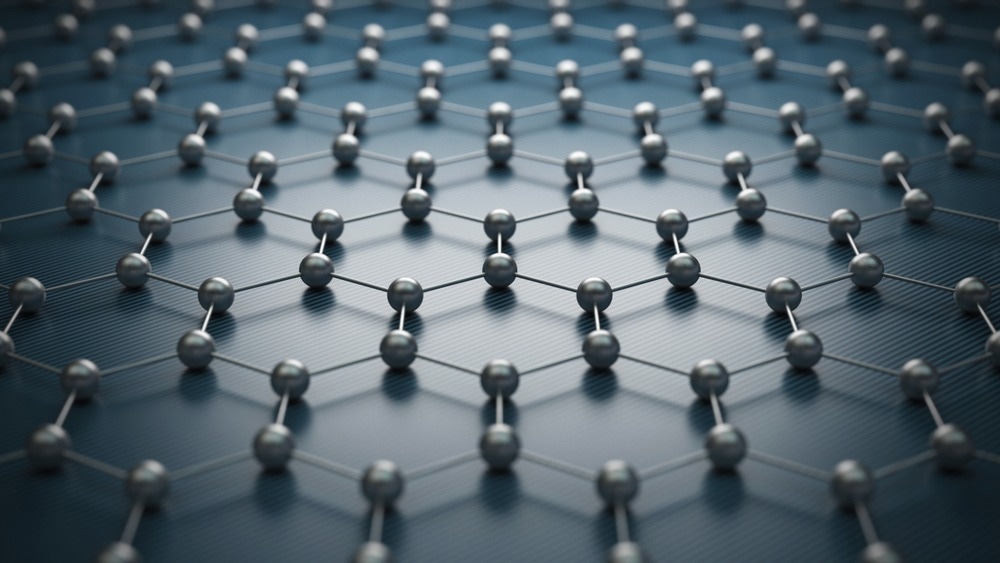
Study: Effect of Substrate Roughness on the Friction and Wear Behaviors of Laser-Induced Graphene Film. Image Credit: koya979/Shutterstock.com
What is Laser-Induced Graphene?
Laser-induced graphene is a three-dimensional high-quality, low-cost carbon-based nanomaterial. Due to exceptional qualities, such as high thermal and electrical conductivity, ease of manufacturing, and environmental friendliness, laser-induced graphene has promising applications in super-capacitors, electro-catalysts, and flexible sensors.
The traditional graphene fabrication methods, such as chemical synthesis, exfoliation, chemical vapor deposition and epitaxial growth, are time-consuming and require special conditions such as high temperatures and a vacuum chamber.
However, the single-step manufacturing approach for laser-induced graphene overcomes the complicated procedures and expensive equipment needs of the traditional methods, making it a low-cost production method with massive potential in various industries.
Graphene Tribology at Micro- and Nano-Scale
Graphene's unique mechanical, physical, and chemical characteristics make it an appealing contender for many tribological applications where wear and friction control is extremely important.
Graphene demonstrates exceptional tribological performance. A single graphene layer can significantly reduce the friction coefficient and wear between tribopairs.
At the nano- and micro-scale, graphene has ultra-low friction and strong wear-resistance qualities, making it a potential solid lubricant. Even though laser-induced graphene has excellent anti-wear capabilities, its effectiveness in macro-scale applications has yet to be investigated.
At a macroscopic scale, rough substrates affect the performance of anti-friction materials, leading to an increase in wear rate and friction coefficient.
Effect of Substrate Roughness on Lubricants
The roughness of the substrate largely dictates the wear and friction performances of lubricating materials.
Since plastic deformation is restricted at high substrate roughness, the friction coefficient rises as the maximum contact pressure and flash temperature at the friction interfaces increase. When high contact pressure generates wear debris particles, wear mechanisms shift from adhesive to abrasive wear.
As roughness negatively affects the lubricants' performance, researchers have experimented with various strategies such as doping, etching, and changing the lubricant's film thickness to lower the roughness.
However, at the macroscopic scale, large substrates reduce the effectiveness of these techniques.
Investigating Effect of Substrate Roughness on Laser-Induced Graphene Films
The effect of substrate roughness on the wear life and friction coefficient of laser-induced graphene films was examined. The direct laser writing process deposited the laser-induced graphene films on silicon substrates.
Brass balls were rolled on rough and mirror-polished silicon substrates. Frictional tests of laser-induced graphene films were conducted using a pin-on-disk tribometer. Each laser-induced graphene film underwent more than five 30,000 cycle tests.
The microstructure of the transfer layers on the brass ball surfaces and wear tracks were investigated using the energy dispersive spectrometer (EDS), a scanning electron microscope (SEM), Raman spectroscopy, and an optical microscope.
Significant Findings of the Study
The friction coefficient of the laser-induced graphene increased from 0.11 to 0.24, and the substrate roughness increased from 1.4 nm to 54.8 nm. The wear life of the laser-induced graphene was more than 20,000 cycles for the rough and mirror-polished silicon substrates.
When the substrate roughness rose to 21.2 nm, the wear life first reduced dramatically from over 30,000 cycles to 10,000 cycles. However, it increased to more than 20,000 cycles when the substrate roughness was more than 35.6 nm.
An analysis of the laser-induced graphene films on silicon substrates using SEM, EDS, optical microscopy, and Raman spectroscopy indicated an evolution of the friction mechanism.
A stable and thick graphene nanocrystallite transfer layer could grow and persist on the counterpart ball for the mirror-polished Si substrate, causing friction between the film and the Si substrate.
For Si substrates with a relatively minor surface roughness, laser-induced graphene could not be maintained on either the Si substrates or the counterpart balls, resulting in severe friction between them.
In case of high surface roughness, laser-induced graphene would be compressed and stored in the grooves of the Si substrate. It enables a stable anti-wear performance and lowers the surface roughness at the friction interface. This proves the high adaptability of laser-induced graphene as a lubricant.
This study demonstrates the excellent friction adaptability of a laser-induced graphene film. Furthermore, it highlights the friction mechanism development of laser-induced graphene films manufactured on silicon substrates with varying surface roughness.
Reference
Xue, P., Huang, Z., & Chen, C. (2022). Effect of Substrate Roughness on the Friction and Wear Behaviors of Laser-Induced Graphene Film. Lubricants. https://www.mdpi.com/2075-4442/10/10/239/htm
Disclaimer: The views expressed here are those of the author expressed in their private capacity and do not necessarily represent the views of AZoM.com Limited T/A AZoNetwork the owner and operator of this website. This disclaimer forms part of the Terms and conditions of use of this website.