A recent study published in Micromachines describes the design, fabrication, and testing of a silicon inertial optical sensor for low-frequency (less than 2 kHz) applications. The researchers used finite element analysis parameterization to consider different accelerometer designs.
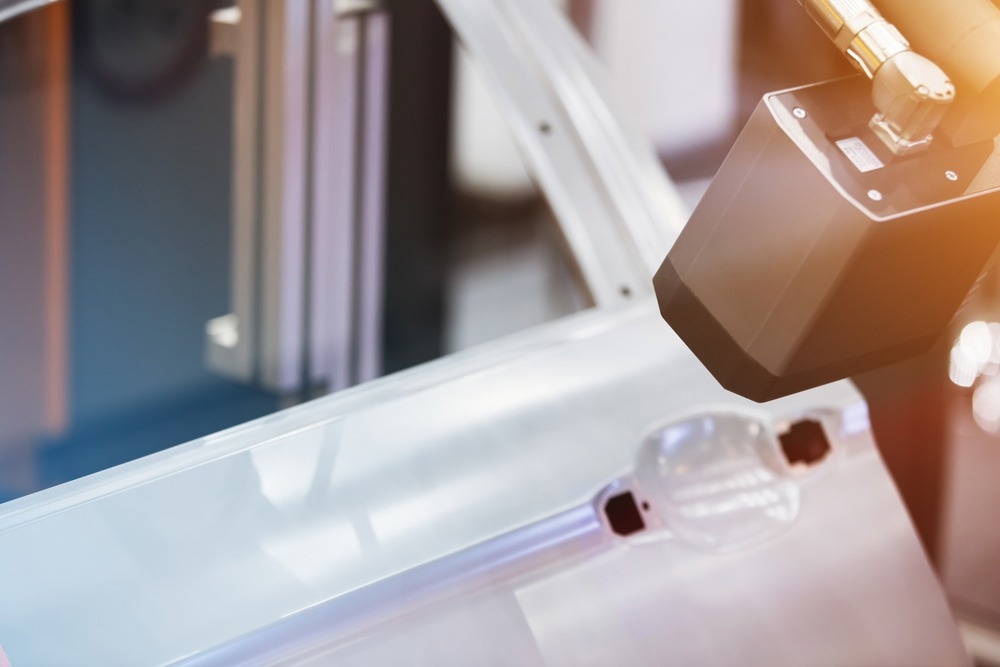
Study: Optical Sensor, Based on an Accelerometer, for Low-Frequency Mechanical Vibrations. Image Credit: MOLPIX/Shutterstock.com
An interferometer was used for detection, eliminating the requirement for electric signals vulnerable to electromagnetic interference and significant temperature changes. It was determined that it is possible and practical to design and manufacture an optical vibration sensor for potentially harsh environments with a low cost based on the fabrication technology using only a silicon wafer with both sides etched.
MEMS Sensors for Monitoring Vibrations at Low Frequencies
Seismic waves or piezoelectric vibrations of energy harvester systems are examples of low-frequency vibrations. Vibration detection can signal the presence of risks, necessitating a choice or course of action. Traditional vibration sensors use piezoelectric technology and are relatively larger.
MEMS sensors for vibration detections have been developed recently with many benefits, including lower weight and smaller size.
MEMS sensors are used at low frequencies owing to their high sensitivity, readout circuitry, straightforward transduction, reduced resistance to temperature linearity, low noise level, smaller area, and feedback-capable design. They also have advantages over other types of sensors because they can be manufactured without using exotic materials.
Vibration sensing tends to concentrate on oscillation magnitude rather than precise position tracking. Therefore, linear sensors such as MEMS accelerometers are sufficient for gathering motion data.
Designing Beam Geometries of MEMS Sensors for Determining the Frequency Responses
An accelerometer's components include mass coupled to an inertial frame via flexible supports and a device that measures the displacement of the moving mass. The surface of the mass is moved away from its resting position on an axis by mechanical vibrations related to the inertial frame. Acceleration forces can be static, such as the constant gravitational force (g force), or dynamic, such as those brought on by pulsating or moving the accelerometer.
The frequency responses of the accelerometers are influenced by the beams' effective stiffness constant, making them appropriate for various applications. As a result, various beam geometries have been developed, including folded, spiral beams, L-shaped beams, and folded beams with turns (comb accelerometer). These geometries include fully symmetrical double-sided H-shaped beams, slanted beams, symmetrical double-sided serpentines, straight- and crab-leg serpentines, and folded beams.
Development of an Optical Sensor Based on a Silicon Accelerometer
Sánchez-Fraga et al. developed an optical sensor based on a silicon accelerometer. The amplitude of the accelerometer mass displacement was determined using interferometric methods because the surface of the accelerometer mass reflects a monochromatic, coherent beam of light. The interference between a reference laser beam and the beam reflected from the accelerometer surface was examined using a Michelson interferometer. The measured electrical signal is used to cast the interference as a pattern of light and shadow bars onto a photodiode for analysis.
The pattern can show a shift in the perpendicular direction when the microstructure surface mirror swings back and forth in the light direction. This shift results from the shifting distance between the beam splitter and the microstructure surface. It was previously understood that the length shift that occurs when a bar replaces an adjacent one is equal to half the light's wavelength. The interferometer and shaker-mounted accelerometer were lined up for sensor testing. The shaker's purpose is to produce vibrational effects.
Improved Responses at Lower Frequencies
The optical sensor based on a silicon accelerometer developed in this research showed an improved response at lower frequencies than traditional designs. The mechanical mounting pieces were fabricated by researchers, while the interferometer was assembled with commercial components. The optical sensor based on a silicon accelerometer was utilized in environments with temperatures higher than 85 °C.
Young's modulus fluctuations in silicon, the material used to fabricate the microstructure, were reported to be negligible at 200 °C. Therefore, it is anticipated that the system will function at this temperature with an estimated 2% variance in vibration amplitude. The optical sensor based on a silicon accelerometer detected signals with a maximum resolution of 17.5 nm and a frequency of up to 13 kHz. This range can be extended and the number of applications can be increased by using a photodiode and shaker with a broader bandwidth. The optical sensor employs an interferometer-enabled microstructure detection at a distance adequate for measurements in sealed systems with a significant temperature differential and immunity to electromagnetic interference and radio frequency interference.
This research used monocrystalline silicon wafers etched on both sides during microfabrication rather than a silicon-on-insulator (SOI) substrate. This provided more ambiguity in the final microstructure thickness for a more practical and adaptable method. The ability to obtain various spring thicknesses represents flexibility.
Reference
Sánchez-Fraga, R., Tecpoyotl-Torres, M., Mejía, I., Mañón, J. O., Riestra, L. E., & Alcantar-Peña, J. (2022). Optical Sensor, Based on an Accelerometer, for Low-Frequency Mechanical Vibrations. Micromachines, 13(9), 1462. https://www.mdpi.com/2072-666X/13/9/1462
Disclaimer: The views expressed here are those of the author expressed in their private capacity and do not necessarily represent the views of AZoM.com Limited T/A AZoNetwork the owner and operator of this website. This disclaimer forms part of the Terms and conditions of use of this website.