High resolution, high sensitivity measurements of adhesion forces can potentially transform many applications. A newly developed Fiber-Tip Microforce Sensor (FTMS) by Professor Yiping Wang and colleagues from the Guangdong and Hong Kong Joint Research Centre for Optical Fiber Sensors at Shenzhen University, displays unseen levels of micronewton sensitivity to measure adhesion forces. Their findings are published in the latest issue of Multidisciplinary Digital Publishing Institute (MDPI) - Biosensors.
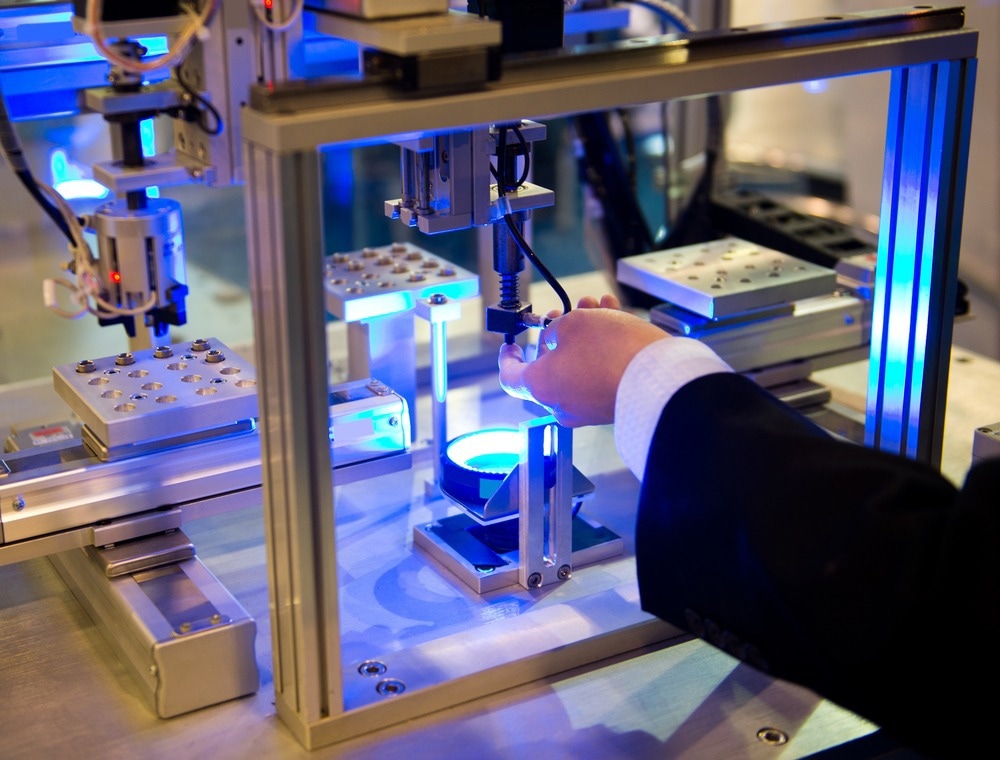
Study: Measurement of Interfacial Adhesion Force with a 3D-Printed Fiber-Tip Microforce Sensor. Image Credit: hxdbzxy/Shutterstock.com
What is Adhesion Force?
Adhesion force describes how two interfaces are pulled and maintained together under general environmental conditions. For example, when water is poured into a glass, there are natural molecular mechanisms at work between the surface of the glass and the water molecules.
Adhesion force is a collective effect constituted by the attractive electrostatic force, the chemical bonds between hydrogen atoms, the van der Waals force and the capillary force.
The importance of understanding adhesion forces in depth has risen due to the rapid growth of nanotechnology. At nano interfaces, the ratio of surface area to volume increases. Better knowledge of the underlying physics at these nano interfaces will aid in developing better nanotechnology.
What is Adhesion Force Used For?
Adhesion forces are used advantageously in many industries. Molecular dynamics at the interface of two materials determines critical structural behavior in civil and automotive engineering. Biomedicine uses adhesion forces in drug development. Material science, nano, electromechanics, and the aerospace industry study the interface interactions to develop valuable tools.
What Technology is Used for Measuring Adhesion Forces?
Atomic force microscopy (AFM) is currently the primary technique used for measuring forces between interfaces. AFMs use a scanning probe across the surface under investigation and record any deflection using a feedback loop.
Adhesion force detection has been routinely carried out using AFMs. While slight variations of AFMs have successfully revealed subtle adhesion forces, several drawbacks have been encountered.
AFMs have been primarily used in specialist laboratories because of their large dimensions and complicated operational procedures.
Furthermore, the rigidity of the different materials used as micro-cantilevers limits the detection sensitivity. AFM tips resonate or fluctuate in the presence of external forces. The threshold to detect subtle variations is low for weak forces, such as adhesion forces, and the AFM feedback mechanism has not been successful.
Optical fiber-based detection schemes are another method used for force sensing at interfaces. Optical fibers offer shielding against electromagnetic interferences and are compact. Nevertheless, the elasticity associated with silica, a major component in fiber technology, has proved to be too great to measure adhesion forces, which are in the order of micro-newtons.
Fiber-Tip Microforce Sensor
The research efforts of Professor Yiping Wang’s group have developed a fiber-tip microforce sensor (FTMS) that can detect very weak forces. The objective of the FTMS was to measure adhesion forces between interfaces at micro and nanoscales.
Femtosecond laser two-photon polymerization (TPP) nanolithography is a 3D fabrication method commonly used in nanotechnology. The FTMS in Prof. Wang’s laboratory was built with ultra-high accuracy using femtosecond TPP.
A micron-sized clamped-beam probe was 3D printed on a single mode fiber (SMF). As described in the MDPI-Biosensors publication, the spacing between the clamped-beam probe and the fiber face created a Fabry-Perot microcavity. This unique arrangement made the FTMS capable of sensing weak forces.
Any forces encountered by the clamped-beam probe will alter the Fabry-Perot cavity length. This could be any non-contact force such as electric fields, or an external element can slightly nudge the clamped-beam probe. The change in the Fabry-Perot length acts as an optical signal amplifier to detect the weak force.
The FTMS was used to detect adhesion forces on the surface of a hydrophilic hydrogel. The measured data was fitted with a finite element analysis model. Contributions from electrostatic force and the capillary force were studied. The FTMS was found to have a force sensitivity of 1.05 nm/μN and a force sensing resolution of 19 nN. Another test of non-contact adhesion force of adult female hair was also measured successfully by FTMS.
The results from Wang's group showcase the FTMS as a flexible, compact, microscale force detector for adhesion forces acting on micro/nanoscale structures.
Future Prospects
Due to the high force sensitivity displayed by FTMS, it is positioned to have a big impact on assessing adhesion forces. Apart from increased imaging potential in biological materials, the small size, flexible usage and all-optical operation are attractive features in other industries. AFM microscopes can easily integrate the FTMS to its range of capabilities.
References
Zou, Mengqiang, Changrui Liao, Yanping Chen, Zongsong Gan, Shen Liu, Dejun Liu, Li Liu, and Yiping Wang. (2022) Measurement of Interfacial Adhesion Force with a 3D-Printed Fiber-Tip Microforce Sensor. Biosensors, 12, no. 8: 629. www.mdpi.com/2079-6374/12/8/629/htm
Disclaimer: The views expressed here are those of the author expressed in their private capacity and do not necessarily represent the views of AZoM.com Limited T/A AZoNetwork the owner and operator of this website. This disclaimer forms part of the Terms and conditions of use of this website.