The project was the pick & place of scaffolding poles with the EyeVision 3D software and the HELIOS Time-of-Flight 3D sensor by Lucid.
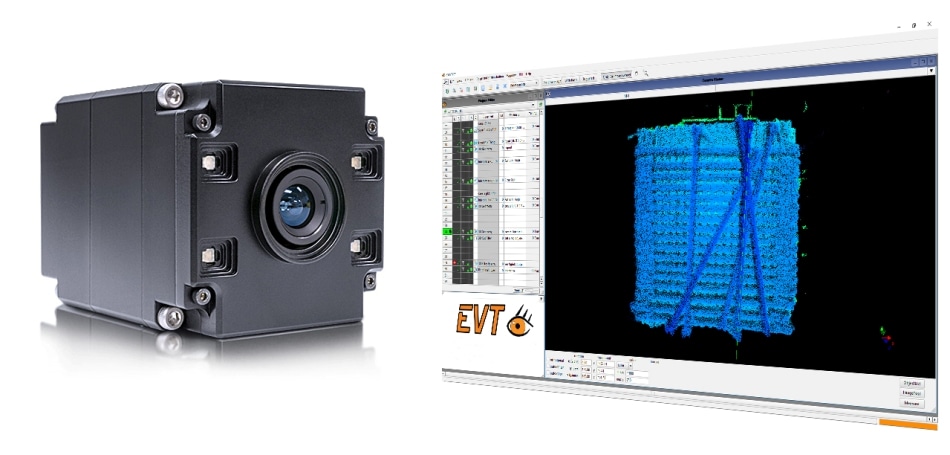
The scaffold loading station was 3D processed using fast time to market, EyeVision 3D software for EVT and the HELIOS Lucid Vision’s high-performance ToF camera.
The scaffolding loading application is capable of handling an object size of 1200 x 1200 mm in width and height and is able to recognize pipes (poles) with a diameter of 60 mm within a precision of 5 mm.
HELIOS was selected as the most suitable ToF solution considering the range, resolution and processing speed. EyeVision 3D was selected as a software, that has rapid development and high flexibility with drag-and-drop programming and a little script programming for further flexibility. And the system was therefore carried out successfully.
On the software development aspect, the conventional method of development using commercial library had several burdens: development time, difficulties to cope with complicated situations and frequent updates to the program requirements.
The software development to process the recognition result from the camera in combination with the robot coordinates and posture in relation to the object recognition is not easy with the conventional method of programming.
And the packaged type 3D sensors for picking systems are limited for customization needs, and provide little flexibility and are therefore not suitable for this project.
But with EyeVision 3D the implementation of the scaffold loading station was very easy.