Offering speed, flexibility and accuracy at a reasonable cost, galvanometer-based optical scanners or ‘galvos’ are the ideal positioning solution for a myriad of scientific, imaging, industrial and medical laser applications.
The constant developments in servo and galvo technology have resulted in devices with step-response times of 100-µs range, single microradian-level positioning resolution, closed loop bandwidths in the kilohertz range even for larger beams, and optimum RMS frequency of greater than 2kHz.
Design requirements differ for each application. However, the availability of a wide choice of galvo configurations and capabilities provides more options to system designers to meet the prerequisites of a specific application.
Components and Technology
The three main components of a galvo system are the mirror or mirrors, galvanometer and the servo driver to control the device. Selecting these components with an appropriate design is crucial to achieve optimum performance from a galvo system. Most of the design principles and rules that are applicable in the measurement of system-positioning performance in milliseconds are inadequate for galvo systems.
The two key components of a galvanometer (Figure 1) include the actuator and the integral position detector. The mirror load is controlled by the actuator and the closed loop system gets information about the mirror position from the integral position detector. Today’s high-performance systems have two actuator configurations.
.jpg)
Figure 1. Galvanometer
A galvo system’s positioning accuracy is heavily influenced by the design of the positioning detector and its speed is affected by the inertial and resonant frequency characteristics of the positioning detector. With a smaller footprint, low inertia and low noise characteristics, Cambridge Technology’s patented optical position detectors are compact, economical and have better speed when compared to capacitive devices, while maintaining stability and accuracy.
The mirror (Figure 2) plays a vital role especially at the increased speeds of galvo systems. Its profile, thickness, materials and cross section not only affect the galvo system’s inertia but also influence the resonant frequency, stiffness of the actuator and mirror assembly. In two-axis steered-beam systems, the size of the second mirror is typically bigger than the first because of the available angular range of the design and the distance between the axes of rotation.
.jpg)
Figure 2. The mirror plays vital role especially at increased speeds of galvo systems.
The servo circuitry of a galvo system drives the system and controls the mirror position. The current output signals of the position detector are demodulated and compared with the commanded position signal by the servo, which then brings the system to the position of interest by driving the actuator. The error between the signals is forced to be nearly zero. Galvo performance has been significantly improved with new digital servo architectures like State-Space when compared with analog or digital PID servos.
Analog Servo Configurations
There are two analog servo configurations to balance or optimize the speed and accuracy requirements of galvo systems. Class 1 or integrating servo or Proportional-Integral-Derivative (PID) (Figure 3) achieves the optimum positioning accuracy with the minimum angular error using integrated position error. Class 0 or non-integrating servo is preferred for applications where accuracy is secondary over speed. Non-integrating Class 0 servos are preferred in most of the highest-speed applications.
.jpg)
Figure 3. Analog PID servos
New Digital State-Space Servo Architectures
Galvos’ performance is improved with new digital state-space servo architectures (Figure 4) through reduction and elimination of the "Tracking Error" that is most common in PID servos. Reduced tracking error significantly improves the overall galvo performance by eliminating software delays in motion programs that were introduced to offset the time differences caused by the tracking error. Computer-assisted tuning or self-tuning is another advantage of digital servos.
.jpg)
Figure 4. Digital state-space servo
Motion Categories
Although laser systems use many different kinds of beam positioning motions or command structures, the most commonly used are Raster, Vector and Step-and-Hold positioning motions. In vector-positioning applications, beam motion would be structured into a string of tiny angular vectors or steps for process uniformity and optimum material throughput.
In Raster-positioning applications, the velocity of the aperture or beam is constant during active imaging, creating active lines connected by a faster retrace. Acceleration is virtually zero during this active imaging time. The acceleration becomes high during fly back, thus increasing current through the galvo coil. In Cambridge Technology 62xxH family of galvos, the moving-magnet actuator’s rigid structure and its low thermal resistance from coil to case make it ideal for most Raster-positioning applications.
In step-and-hold positioning applications, a high torque actuator with low inertia for fast acceleration and for rapidly reaching the commanded position, and a highly precise and stable position detector are the most critical galvo system parameters. The moving-coil class of galvo featuring uncompensated scale drift of 50PPM per degree of temperature change, position detector linearity of greater than 99.9%, and single-microradian repeatability is suitable for these applications.
Conclusion
The closed-loop galvanometer meets the speed and accuracy requirements of system designers at a lower cost, with more options that are impossible with other scanner technologies. With a wide range of features, galvo systems meet the requirements of a myriad of applications.
Developments in this technology in combination with laser technology developments extend the application range of the galvanometer, realizing new performance levels, markets and applications. Gaining knowledge about the key parameters for positioning speed and precision, in conjunction with appropriate design and selection of the galvo system components such as the mirror, servo driver and galvanometer is of high importance to achieve the optimal performance in any galvo application.
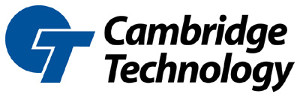
This information has been sourced, reviewed and adapted from materials provided by Cambridge Technology, Inc.
For more information on this source, please visit Cambridge Technology, Inc.