Laser heat treatment selectively modifies the surface of a material, using rapid heating and controlled self-quenching to induce microstructural enhancements while preserving its structural integrity. This article provides an overview of laser heat treatment, how it works, the various techniques and processes involved, key applications across industries, and the future outlook for this rapidly evolving technology.
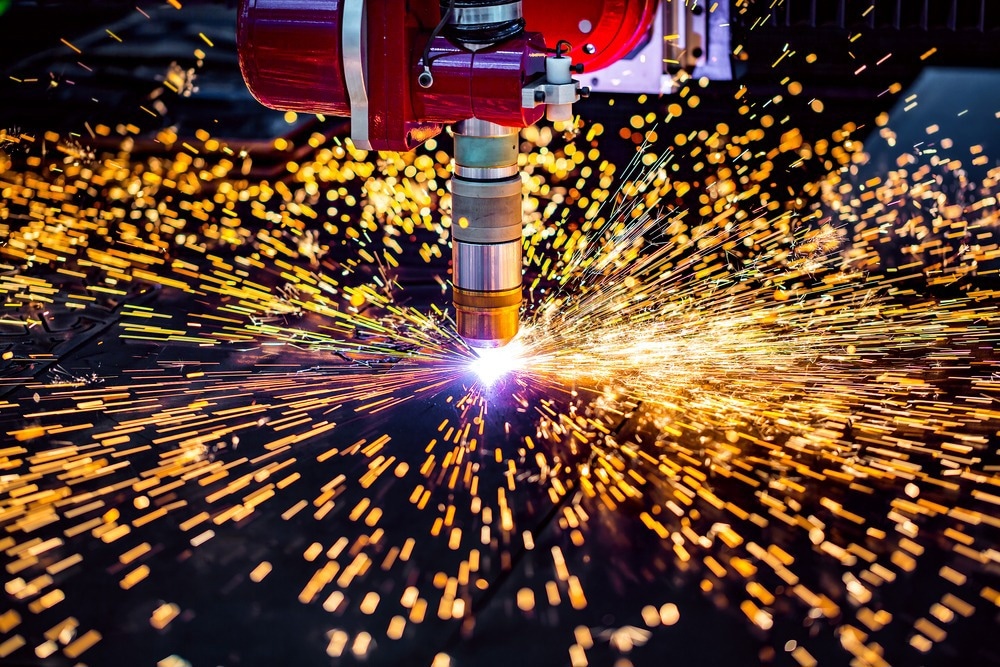
Image Credit: Andrei Armiagov/Shutterstock.com
Laser Heat Treatment: An Overview
Laser heat treatment is a surface engineering technique that uses high-power laser beams to selectively modify metal surfaces' composition, structure, and properties. It is commonly applied to steel and cast iron materials that require enhanced wear, fatigue, and corrosion resistance.
In contrast to conventional heat treating techniques, laser heat treatment offers the unique capability of precisely targeting specific areas for property improvements while preserving the integrity of the underlying material. This pinpoint accuracy results in surface modifications without the risk of warping or cracking, making laser heat treatment a highly precise and versatile method suitable for various parts and products in different industries.
How Does Laser Heat Treatment Work?
The process begins by directing focused laser energy onto the metal's surface, where it is predominantly absorbed. This absorption triggers the excitation of electrons within the metal, resulting in collisions between electrons and the metal's lattice structure. As a result, heat is rapidly transferred from the surface to the interior of the metal, creating a high cooling rate, a critical factor for achieving surface hardening.
What sets laser heat treatment apart is its high power density, meaning a substantial amount of energy is concentrated in a small area, allowing the treated area to swiftly reach the necessary temperature. After laser heating, most of the workpiece remains at a lower temperature, facilitating controlled self-quenching through heat conduction within the metal.
This induces microstructural changes, such as phase transitions, carbide dissolution, and grain refinement, culminating in a surface layer with enhanced properties, all while preserving the bulk integrity of the component.
Primary Laser Heat Treatment Processes
Laser heat treatment technology is employed in the following three different methods:
Transformation Hardening
Laser transformation hardening is the most common laser heat treatment process that uses high-power lasers to rapidly heat a shallow surface layer of ferrous alloys past the austenitizing temperature. This erases microstructural banding and diffuses carbon, producing a uniform martensitic or bainitic structure. The depth of hardening is controlled by laser power and interaction time.
This method improves extreme hardness while minimizing distortion, benefiting components like engine parts, cutting tools, dies, and bearings with significantly extended lifespans.
Laser Annealing
Laser annealing uses lower-power lasers to heat metals enough to relieve stresses, restore ductility, and remove the effects of cold working - all without melting. Although less common than transformation hardening, laser annealing finds applications in improving the fatigue strength of wires for steel-belted radial tires and for repairing cast aluminum housings with misplaced holes.
Laser Surface Melting
Laser surface melting involves using a high-power laser to melt a thin layer of metal on the surface, which subsequently self-quenches. This process refines the microstructure and composition of the surface. It can also homogenize alloys and dissolve harmful inclusions, improving corrosion resistance in aluminum, nickel, and bronze ship propellers.
Although melting may initially induce roughness, the enhanced properties often justify additional smoothing steps. For example, remelting the lobes of cast iron camshafts creates a uniform, wear-resistant martensitic case.
Industrial Applications of Laser Heat Treatment
Laser heat treatment is now widely embraced in industries demanding high wear resistance.
Laser Heat Treatment in the Automobile Industry
In the automobile industry, laser heat treatment is applied to key engine components, including cylinder blocks, liners, and crankshafts. For example, General Motors uses high-power CO2 lasers to partially harden the inner surface of the commutator shell, leading to a significant four-fold increase in work efficiency, with a daily production output of 30,000 sets.
Laser Heat Treatment in Locomotive Manufacturing
Laser heat treatment is being increasingly adopted in the large locomotive manufacturing industry to enhance the durability of locomotives. It involves treating critical components like crankshafts, cylinder liners, and main springs of locomotive diesel engines.
In addition to manufacturing, laser heat treatment of mold surfaces is gaining recognition in the complex, high-precision mold manufacturing process used in locomotive production. This technique can double the lifespan of molds without being constrained by shape or size.
Laser Heat Treatment in the Steel Industry
Laser heat treatment in the steel industry offers versatile hardening options for wear-resistant steel parts like stamping dies. It helps achieve surface hardness levels exceeding 60 HRC for cast iron and 70 HRC for medium and high carbon steel. This enhances wear, fatigue, corrosion, and oxidation resistance without inducing brittleness.
The Future of Laser Heat Treatment
Ongoing advancements in laser technology, such as high-power lasers, robotic automation, and innovative hybrid processes, will enable faster and more flexible laser heat treatment. Industry 4.0 connectivity and data analytics will optimize laser systems, while specialized alloys tailored for laser treatment will improve material performance. This transformative manufacturing process is expected to see wider adoption across industries, contributing to the manufacturing of high-performance products.
More from AZoOptics: What Lasers are Best for Raman Spectroscopy?
References and Further Reading
Dr. Vivian Merchant. (2010). Laser Heat Treating Simplified. [Online]. Available at: https://www.laserfocusworld.com/industrial-laser-solutions/article/14220260/laser-heat-treating-simplified
Haake, J. (2020). What is Laser Hardening? [Online]. Available at: https://www.titanovalaser.com/blog/what-is-laser-hardening/
Merklein, M., Böhm, W., & Lechner, M. (2012). Tailoring material properties of aluminum by local laser heat treatment. Physics Procedia, 39, 232-239. https://doi.org/10.1016/j.phpro.2012.10.034
Preco. (2023). Laser Heat Treating-Precise Surface Modification. [Online]. Available at: https://www.precollc.com/capabilities/laser-heat-treating
Shane. (2023). Laser Heat Treatment: Principles, Advantages, and Applications. [Online]. Available at: https://www.machinemfg.com/what-is-laser-heat-treatment/
Sistaninia, M. (2009). Laser Heat Treatment of Metals Using Rotating and Dithering Beams. InTech. https://doi.org/10.5772/7396
Disclaimer: The views expressed here are those of the author expressed in their private capacity and do not necessarily represent the views of AZoM.com Limited T/A AZoNetwork the owner and operator of this website. This disclaimer forms part of the Terms and conditions of use of this website.