Thin-film optical coatings are utilized across a wide range of industries, including semiconductors, microelectronics, display technologies, and optical element manufacturing. The development and use of advanced coating technologies have ensured many technological breakthroughs. While the end application of the optical thin films can vary, the need for precise control over their thickness and optical properties remains consistent regardless of their use.
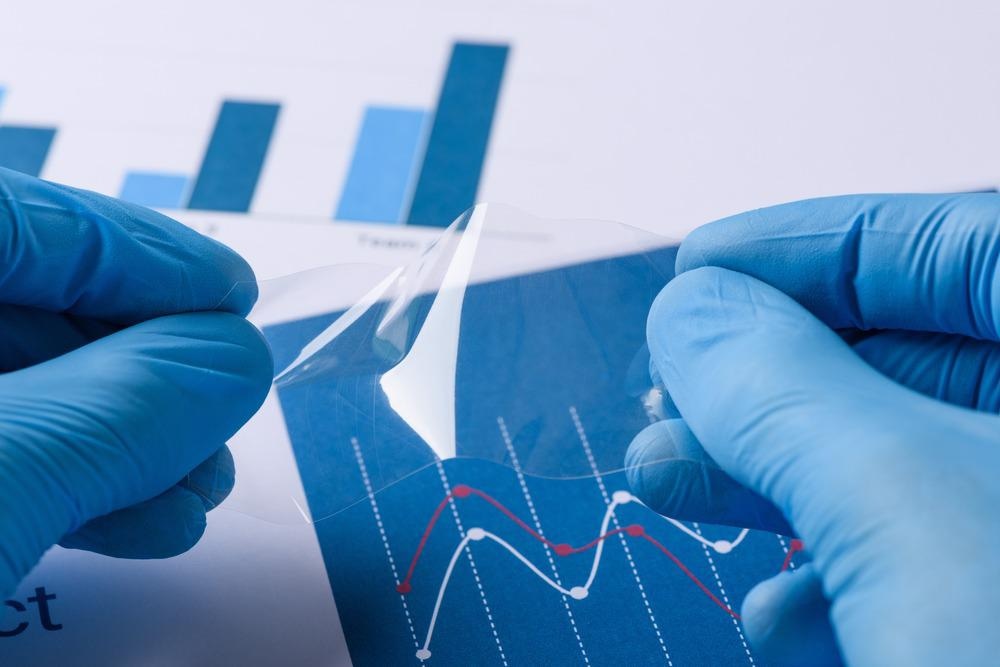
Image Credit: nevodka/Shutterstock.com
Most optical or optoelectronic systems include optical components, such as lenses, mirrors, gratings, detectors, and others, with surfaces and shapes specifically designed for optimal interaction with light.
However, often the specular and transmission properties (mirror‐like properties governed by the laws of reflection and refraction) of these components (determined by the optical properties of the material and surrounding medium), need to be modified to enhance the performance of the system.
What are Optical Thin Films?
Optical thin-film coatings can enhance the transmission, reflection, or polarization properties of an optical component. For example, nearly 4% of the incident light will be reflected by the surface of an uncoated glass component.
An anti-reflection coating can reduce the reflection at each air-glass interface to less than 0.1%. On mirror surfaces, applying a highly reflective dielectric coating could increase the reflectivity to more than 99.99%.
An optical coating is usually a combination of thin layers of materials such as oxides, metals, or rare earth materials.
The performance of a thin film optical coating depends on a wide range of parameters, including the number of the individual layers, their thickness and doping, and the difference in the refractive index of the layers.
The thickness of the individual layers of the coating, which can be from a few nanometers up to several hundred nanometers, together with the difference in the refractive indices of the layers causes interference effects that lead to the desired enhancement of the optical properties. Besides its primary function, since the coating is usually on the outside of the component, the thin film is often expected to perform other functions such as limiting corrosion and increasing abrasion resistance.
Most thin-film optical coatings are designed to enhance the performance of an optical component within a range of wavelengths and for a specific angle of incidence and polarization of light (such as linear polarization, elliptical polarization, or random polarization). Using a coating at a different spectral range, angle of incidence, or polarization than what it is designed for will result in a significant degradation in performance or even a complete loss of the optical function of the coating.
Fabrication of Thin Film Coatings
Thin-film optical coatings are usually fabricated by a vacuum deposition process, where a specifically designed sequence of substances is condensed onto the surface of the optical component through a range of chemical vapor deposition (CVD) or physical vapor deposition (PVD) techniques.
Several PVD processes are commonly used to apply optical coatings, including ion-assisted electron-beam evaporative deposition, ion beam sputtering, advanced plasma deposition, and plasma-assisted reactive magnetron sputtering. Each coating process has unique strengths that make it optimal for specific use cases.
Anti-Reflective Properties of Thin Films
The simple yet most widely used application of thin optical films is in anti-reflection coatings of various optical components.
By exploring the physics of low refractive index coatings deposited onto high refractive index optical material, researchers greatly minimized the amount of undesired reflected light in optical devices such as camera lenses, microscope objectives, binoculars, and spectacle lenses.
Modern high refractive index plastic lenses greatly benefit from such anti-reflective coatings as they reduce glare, particularly during night driving.
Anti-reflective coatings are based on magnesium fluoride thin films with a thickness equal to approximately a quarter wavelength that reduces the reflectance of the coated component. However, more demanding applications require better performance over the entire visible spectrum (400 nm to 700 nm).
The broader the spectrum over which reflection reduction is required, the more complex the structure of the coating is.
Several multilayer coatings have been developed that consist of layers of magnesium fluoride, tantalum oxide, and aluminum oxide that can cover a much broader spectral range.
Application of Optical Coatings in Various Spectral Regions
In practice, modern optical equipment is often required to operate over a much broader spectrum that extends from short wavelengths (UV) to long wavelengths (IR).
Optical components and instruments, such as telecommunication equipment, satellite imagery cameras, space- and ground-based telescopes, and many others, that operate in multiple spectral regions, in particular at long wavelengths in the infrared spectrum, require different coating materials.
Oxide compounds, such as silicon oxide, aluminum oxide, and yttrium oxide, exhibit excellent optical properties at wavelengths shorter than 7 µm and can provide the low-, medium-, and high- refractive indices required for anti-reflective thin-film coatings suitable for the short wave IR and mid-wave IR regions (wavelengths of 0.9-1.7 µm and 3-5 µm, respectively).
At wavelengths longer than 7 µm, the best performing coating material are fluoride-based compounds combined with groups IIB-VIA compounds (ZnS and ZnSe) and germanium.
Silver-based high-performance reflective coatings have become indispensable for many large-aperture optical instruments, such as astronomical telescopes, high-power laser systems, and space-based optics operating at IR wavelengths.
Multi-layer thin films that combine protective layers of silicon nitride, nickel-chromium nitride, and highly-reflective silver film have enormously improved silver mirror durability and performance. For example, such coatings ensure the highest performance of the 8-meter primary mirrors of the telescopes in the Gemini Observatory in Hawaii.
References and Further Reading
Watts, K. E., et al. (2019) Optical Spectroscopy of Surfaces, Interfaces, and Thin Films: A Status Report. Analytical Chemistry, 91 (7), 4235-4265. Available at: https://doi.org/10.1021/acs.analchem.9b00735
Piegari, A. and Flory, F. (eds.) (2018) Optical Thin Films and Coatings - From Materials to Applications, 2nd ed. Elsevier Ltd. Available at: https://doi.org/10.1016/C2016-0-02583-4
Stenzel, O. (2016) The Physics of Thin Film Optical Spectra, 2nd ed. Springer International Publishing, Switzerland. Available at: https://doi.org/10.1007/978-3-319-21602-7
Disclaimer: The views expressed here are those of the author expressed in their private capacity and do not necessarily represent the views of AZoM.com Limited T/A AZoNetwork the owner and operator of this website. This disclaimer forms part of the Terms and conditions of use of this website.