Lasers have become an indispensable tool in manufacturing. From precision cutting applications to complex micromachining, lasers are now the tools of choice to work with a range of materials and manufacturing processes. As well as direct cutting tasks, lasers can also be employed for coating techniques such as pulsed laser deposition.
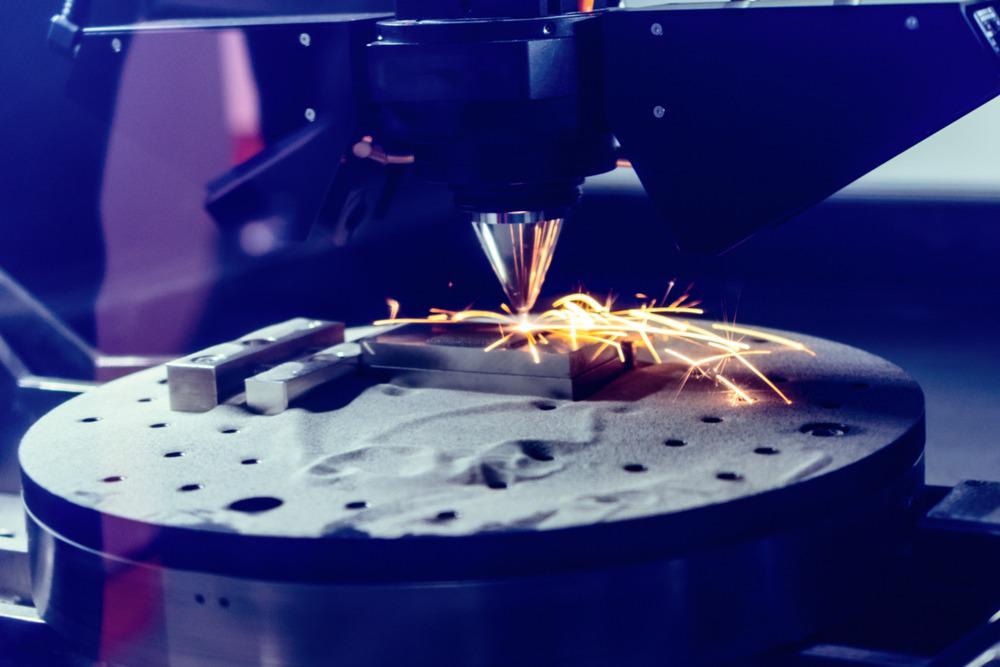
Image Credit: Nordroden/Shutterstock.com
What has made lasers such an invaluable tool is the degree to which the beam output can be controlled and how laser cutting and shaping processes do not induce any local stresses into the surrounding material.1
One of the key benefits of this level of control, precision, and reduction in stress induced in the material, is that lasers can help dramatically reduce the amount of waste in industrial manufacturing.
With traditional blade-based cutting techniques, it is necessary to account for additional material between regions to be cut that will simply be wastage. This ensures that the material properties are not altered by the strain applied during the cutting process.
As well as reducing the amount of material wastage, lasers for manufacturing are becoming increasingly efficient.2 New diode-based lasers use significantly less power than their older CO2 counterparts and developments are being made to increase the energy efficiency of lasers for manufacturing further. Generally, industrial manufacturing lasers are relatively low maintenance in terms of needing new parts and upkeep, whereas cutting blades require regular replacement.2
Photonics Industry
The UK-based photonics industry is anticipated to be worth £50 billion by 2035 and already represents one of the UK’s most productive manufacturing sectors.3 It is predicted that this development and growth will bring about a further 20% increase in the scale of manufacturing areas.
The UK currently employs laser processing for joining, marking, cutting, and 3D printing of materials. By combining these processing technologies with machine vision capabilities, a greater degree of automation can be achieved in the manufacturing process and improvements can be made for quality control.
Quality Control
Micro and nanofabrication have been areas revolutionized by lasers that provide programmable precision to machine structures on the sub-micron length scale. However, many of the applications of such devices, including biomedical systems are very demanding with low tolerances.4
Due to stringent patient safety regulations, medical devices need to be manufactured with a very high degree of precision and accuracy. This means that failing quality control measurements can be a source of great expense and wastage for the manufacturer.
Laser beam conditions, such as mode, pointing and power, can all be tightly controlled. Advances in laser technologies towards hermetically sealed units and greater stability also enhance beam stability performance.
These properties can be integrated into feedback loops for live process control. Many manufacturing applications that make use of laser processing are now taking advantage of the improved process reliability that the integration of beam diagnostics or metrological solutions facilitates.
Metrology has become a key part of laser-quality control assessment and manufacturing, as these high-precision measurements can be performed in-situ.5
Artificial intelligence can be integrated with metrological measurements for autonomous product verification. The high degree and volume of information that can be recovered with laser scanning methods also make them highly appealing for this application.6
New Dimensions
Another aspect of how lasers have drastically changed manufacturing processes and helped to reduce waste is in the creation of 3D and highly complex structures.
It is now possible to create very complex shapes with 3D printing methods without the need to create specialist dies or molds for every product.
As laser beams can be tightly focused, with the only limitation being the diffraction limit of the wavelength of the light used, it is possible to cut and etch very small structures. Some techniques are able to achieve sub-diffraction limit resolution in cutting processes as well.7 This cutting capability can be combined with translational stages for either the product or beam to control the pointing and create 3D structures.
In 3D printing, which is typically performed by depositing layers of resin and curing using a laser in specific shapes, there are increasing efforts to make use of recycled plastics as filaments for the process.8 Different filaments have varied optimal curing times and require different intensities of light, so the use of laser sources with tunable parameters can be helpful to optimize this process and achieve the best manufacturing quality with potentially variable input starting materials.
For 3D machining capabilities, femtosecond lasers have become a tool of choice. This is because their short temporal pulse duration results in very high peak powers generating very high local temperatures.9 They can be used with metals with very high melting points or for additive manufacturing.
The growing capabilities of techniques such as laser-based 3D nanolithography and better beam qualities and stabilities of laser systems will mean laser processing has even more opportunities to reduce waste in manufacturing through high reliability and the need for minimal starting materials.
References and Further Reading
- Bass, M. (Ed.). (2012). Laser materials processing. Elsevier.
- 1 K. Kellens, G. C. Rodrigues, W. Dewulf and J. R. Duflou, Energy and Resource Efficiency of Laser Cutting Processes. Phys. Procedia, 2014, 56, 854–864. https://doi.org/10.1016/j.phpro.2014.08.104
- Photonics Leadership Group (2022) Photonics by 2035, https://photonicsuk.org/wp-content/uploads/2021/10/Photonics_2035_Vision_Web_1.0.pdf, accessed February 2022
- D. Fine, A. Grattoni, R. Goodall, S. S. Bansal, C. Chiappini, S. Hosali, A. L. van de Ven, S. Sriniv, X. Liu, B. Godin, L. B. III, I. K. Yazdi, J. Fernandez-Moure, E. Tasciotti, H.-J. Wu, Y. Hu, S. Klemm and M. Ferrari. Silicon Micro- and Nanofabrication for Medicine. Adv Healthc. Mater., 2013, 2, 632–666. https://dx.doi.org/10.1002%2Fadhm.201200214
- S. K. Everton, M. Hirsch, P. I. Stavroulakis, R. K. Leach and A. T. Clare. Review of in-situ process monitoring and in-situ metrology for metal additive manufacturing. Mater. Des., 2016, 95, 431–445. https://doi.org/10.1016/j.matdes.2016.01.099
- Krar, S. F., & Gill, A. (2003). Exploring advanced manufacturing technologies. Industrial Press Inc.
- Y. L. Zhang, Q. D. Chen, H. Xia and H. B. Sun. Designable 3D nanofabrication by femtosecond laser direct writing. Nano Today, 2010, 5, 435–448. https://citeseerx.ist.psu.edu/
- Dubashi, J., Grau, B., & McKernan, A. (2015). AkaBot 2.0: pet 3D printing filament from waste plastic. Santa Clara University. https://scholarcommons.scu.edu/cgi/viewcontent.cgi?referer=&httpsredir=1&article=1043&context=mech_senior
- Chua, C. K., Vadakke Matham, M., & Kim, Y. J. (2017). Lasers in 3D printing and manufacturing. World Scientific.
Disclaimer: The views expressed here are those of the author expressed in their private capacity and do not necessarily represent the views of AZoM.com Limited T/A AZoNetwork the owner and operator of this website. This disclaimer forms part of the Terms and conditions of use of this website.