Electric vehicles (EVs) are becoming an increasingly common sight with retail prices dropping, continuing technological developments, and a social push for green technologies. Over 2 million EVs were sold globally in 2019, with China continuing to lead this drive, particularly with the purchase of two or three-wheeled vehicles and urban buses.1
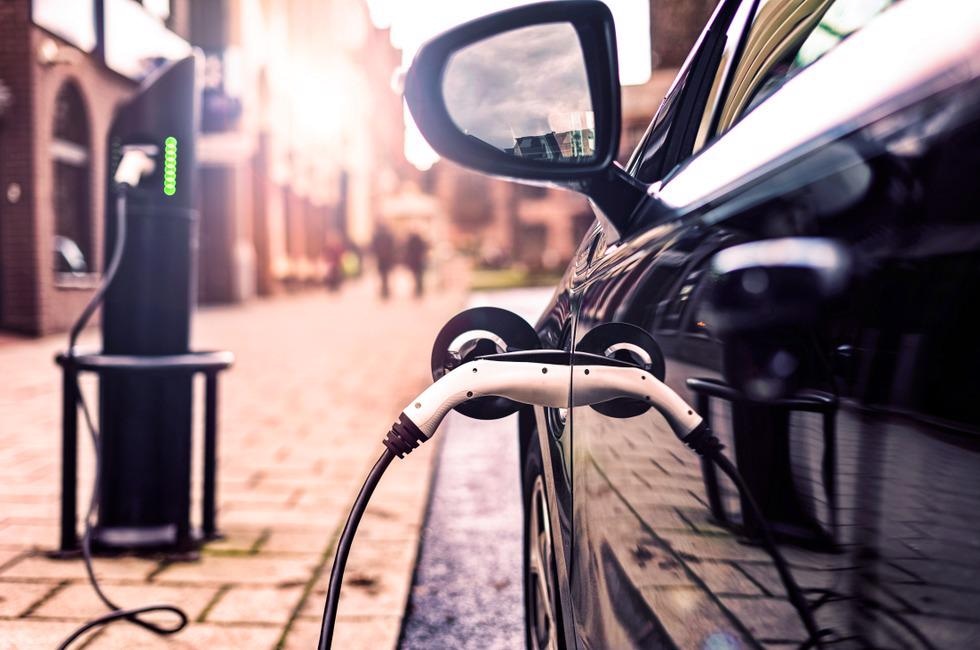
Image Credit: nrqemi/Shutterstock.com
One of the key developments in the EV industry has been the growth of battery technologies, such as improvements in their longevity, lifespans, and reductions in charging time. With the growth of new developments, though, comes the demand for new manufacturing and maintenance techniques. For the electric vehicle industry, one of these has been laser cleaning for EV batteries.
Laser Cleaning
Laser cleaning is an advanced manufacturing technique that can prepare surfaces for further work with micron precision. By using a high-intensity laser beam, imperfections in the surface structure can be ablated from the surface and removed by suction. This technique can be used to remove paint, rust, grease, and other surface contaminants.2
Different laser cleaning processes can be performed depending on the type of contamination and whether it is embedded on the surface or adhered to the top. If the contaminant and metal surface have different chemical properties, the contaminant layer can often be ablated with no thermal load induced in the metal surface. For more deeply embedded contaminants, it may be necessary to remove the first layer of the metal to obtain a thoroughly clean surface.
The key to achieving good cleaning properties is the use of lasers with very high peak powers. Pulse fiber laser sources with short pulse durations, often nanoseconds or less, help achieve the high power output required to ablate even very strongly bonded and stubborn contaminants. They can also induce the thermal load required to ablate the metal surface for deeper cleaning.
Cleaning For EV Batteries
The ability to control the cleaning process with micron precision and avoid excess thermal load on the substrate are amongst the reasons that laser cleaning has become widely used in the EV battery industry. High heat levels on batteries pose a significant explosion risk, emphasizing the need to design possible interlock systems that help safeguard the laser and battery in the event of a malfunction.
Now, Laserax has developed a new laser cleaning system optimized perfectly for EV battery cleaning.3 This new Battery Cleaning Machine is a turn-key system that wields a powerful 500 W pulsed fiber laser system for the rapid preparation of surfaces for welding.
Laserax’s Battery Cleaning System
The Battery Cleaning System consists of a gantry that moves the laser head, making it possible to reach all of the different areas of the battery cells and any busbars in full 360° motion.
Accompanying the flexible gantry system is an integrated camera for process monitoring that can measure all cell locations. It can also be used for manual or automated adjustments of the laser cleaning process. The laser and cleaning can be controlled with the use of an HMI control panel that provides direct access to all the laser parameters.
As well as the rapid cleaning speeds, one of the key aspects of Laserax’s Battery Cleaning System is its flexibility. The gantry system means that it can be used to clean a variety of shapes and sizes.
The flexible door system means that modules can be loaded manually or automatically into the machine with a conveyor; as your manufacturing needs evolve, Laserax’s systems can grow and adapt with you.
Battery Cell Laser Cleaning & Battery Tray Laser Marking
Video Credit: Laserax/YouTube.com
Vision and Safety
The Cognex camera and vision control system can be used to identify cleaning quality and dynamically adjust the cleaning process. Here, it can be synchronized with the conveyor system to ensure objects that require longer cleaning times can be stopped in transit – or be sufficiently short to facilitate cleaning on the fly.
One of the challenges with laser cleaning can be the toxicity of the materials ablated from the surface. The embedded fume management system helps remove particulates as they are generated and serves a dual purpose: one, to improve the quality of the cleaning by ensuring contaminants are rapidly extracted, and two, to keep the environment safe for employees at all times.
References and Further Reading
IEA. (2020) Global EV Outlook 2020 – Analysis - IEA. [online] Available at: https://www.iea.org/reports/global-ev-outlook-2020 [Accessed 15 August 2021]
Kane, D., (2007) Laser Cleaning Ii. Singapore: World Scientific. Available at: https://doi.org/10.1142/6301 [Accessed 15 August 2021]
Laserax. (2021) Laser Cleaning & Marking Electric Vehicle Battery Modules. [online] Available at: https://www.laserax.com/cleaning-marking-electric-vehicle-parts [Accessed 15 August 2021]
Disclaimer: The views expressed here are those of the author expressed in their private capacity and do not necessarily represent the views of AZoM.com Limited T/A AZoNetwork the owner and operator of this website. This disclaimer forms part of the Terms and conditions of use of this website.