Article updated on 17 August 2021.
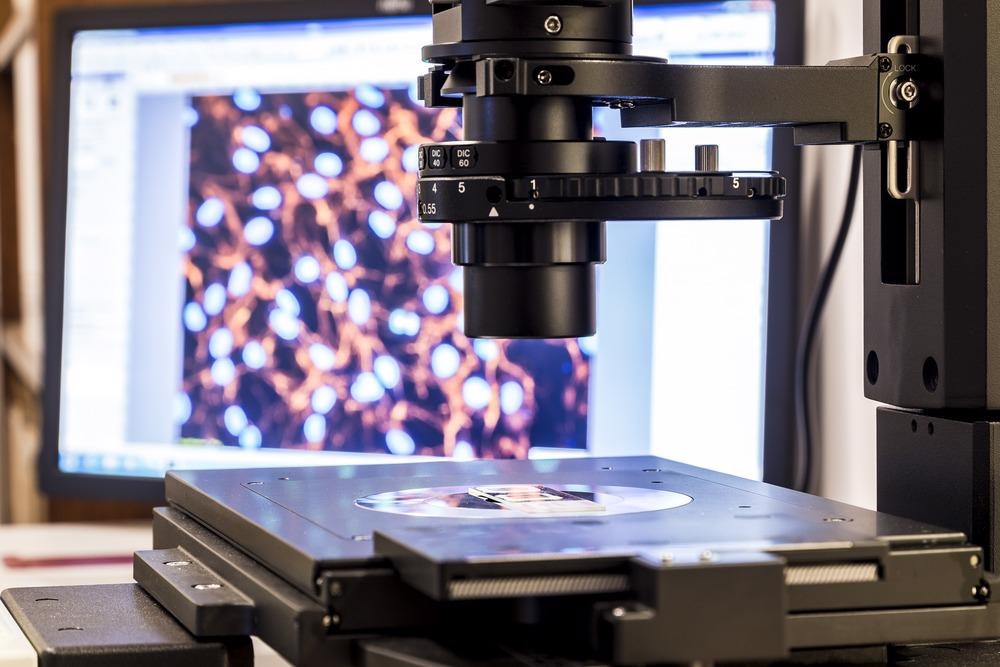
Image Credit: dominika zara/Shutterstock.com
An atomic force microscope (AFM) is a type of scanning probe microscope that was invented in 1985 and quickly became a fundamental instrument used in many different disciplines within science and technology. Recent improvements in AFMs are allowing their use to be expanded into new applications and industries.
How Does an Atomic Force Microscope Work?
An AFM uses a sharp probe tip fixed to a cantilever to scan the sample’s surface. As the probe tip can get very close to the surface, the sample's intermolecular forces cause deflections in the cantilever.
A laser beam is reflected off the cantilever into a photodiode detector to identify the cantilever deflection changes. The detector’s signals are then analyzed to establish changes in height on the surface to produce a three-dimensional topographical image.
AFMs have an incredible resolution, especially when compared to an optical microscope. They obtain measurements in fractions of a nanometer and scan samples in sit without needing a vacuum or sample preparation like other techniques such as electron microscopy. However, AFMs are large pieces of equipment and have expensive components, making them inaccessible to many.
Recent Improvements and New Applications
One of the recent improvements was the development of an AFM on a chip by researchers at The University of Texas at Dallas. A standard AFM is a costly and large machine that can be a barrier to more widespread use. Using a microelectromechanical systems (MEMS) approach allows all the electromechanical components to be downsized onto a single chip, producing a considerably smaller and cheaper AFM.
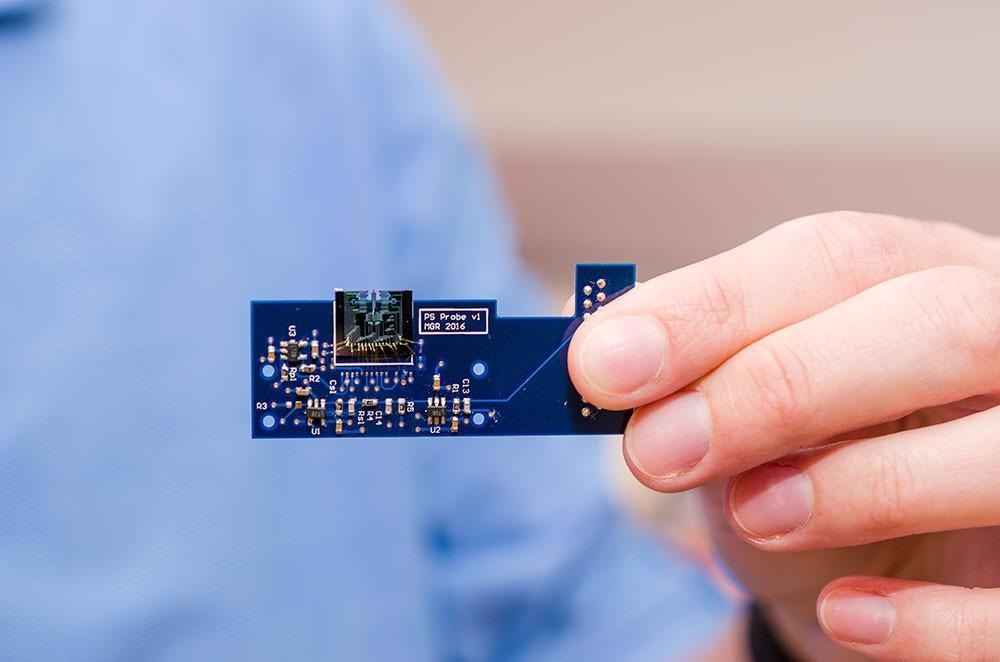
A MEMS-based atomic force microscope developed by researchers at The University of Texas at Dallas, shown attached to a small circuit board. Image Credit: The University of Texas at Dallas
A MEMS-based AFM is approximately 1 square centimeter in size and is attached to a small circuit board. The circuit board consists of the circuitry, sensors, and other components which control the device.
MEMs can be mass-produced cheaply, which means an entire miniature AFM system could be considerably less expensive than a conventional setup which requires lasers and other large components. This will make the use of atomic force microscopy accessible to more industries and research institutes.
Aside from size and cost, MEM-based AFMs also operate in a different mode to conventional AFMs. Conventional AFMs usually have the probe tip at a constant height with varying force applied to the sample, which can cause damage if the sample is exceptionally soft. If the sample surface is hard, then the probe tip can wear down.
MEM-based AFMs operate using tapping mode in which the cantilever and probe tip oscillates up and down on the sample’s surface while moving across the sample. A feedback loop maintains the oscillation height to create the topographical image.
The low cost and non-abrasive nature of MEM-based AFMs mean their use could expand into new industries. There is the potential for an array of AFMs to be used efficiently in quality control, for example:
- For detecting faults on silicon wafer surfaces
- The manufacture of brittle and easily breakable computer chips
A technique that can be used without the risk of damage is invaluable. One of the researchers Dr Reza Moheimani, professor of Mechanical Engineering at the university, said, “This is one of those technologies where, as they say, ‘If you build it, they will come.’ We anticipate finding many applications as the technology matures.”
From the University of Newcastle, Dr Ruppert and his team have published numerous papers recently proposing integrated cantilever designs that will improve overall AFM performance.
These designs optimize the deflection sensitivity of the cantilever as well as achieving arbitrary placement of resonance frequencies. They also offer integrated multi-mode Q control, which improves imaging stability and increases scan speed.
A further development comes from a research team led by Dr Paul Ashby at the Lawrence Berkeley National Laboratory. The majority of nanoscale imaging techniques can only be used on samples that are immobile. However, after decades of research, Ashby has developed novel AFM capabilities that allow liquid structure imaging.
The probe tip is controlled to interact with fast-moving particles on the surface without disturbing the remaining liquid underneath. The team utilized these new techniques to record high-resolution, real-time footage of liquid structures forming as nanoparticle surfactants formed a solid layer at the oil-water interface.
This is an exciting development as previously little information was known about how these materials form. The development could allow for advancement in the field. Liquid structures are used in many different applications, including cosmetics, food processing, and medicine. Further understanding of how liquid structures form could lead to new biomedical applications. They can be optimized to be used in drug discovery and drug delivery, such as targeted cancer treatments.
References and Further Reading
MENAFN (2021) Scanning atoms with the tip of a needle. [Online] MENAFN. Available at: https://menafn.com/1101650776/Scanning-atoms-with-the-tip-of-a-needle. (Accessed on 26 February 2020).
Asylum Research (2019) Applications of Atomic Force Microscopy (AFM) - A Guide. [Online] AzoNano. Available at: https://www.azonano.com/article.aspx?ArticleID=5182 (Accessed on 26 February 2020).
ICSPI Corp. What is Atomic Force Microscopy (AFM)? [Online] ICSPI Corp. Available at: https://www.icspicorp.com/. (Accessed on 26 February 2020).
Office of Media Relations (2017) Jonsson School Engineers Shrink Microscope to Dime-sized Device. [Online] The University of Texas at Dallas. Available at:
https://www.utdallas.edu/news/science-technology/jonsson-school-engineers-shrink-microscope-to-dime/ (Accessed on 28 February 2020).
Maroufi, M., et al. (2016) On-Chip Dynamic Mode Atomic Force Microscopy: A Silicon-on-Insulator MEMS Approach, Journal of Microelectromechanical Systems. doi.org/10.1109/JMEMS.2016.2628890.
Ruppert, M.G., et al. (2015) Multimode Q Control in Tapping-Mode AFM: Enabling Imaging on Higher Flexural Eigenmodes. IEEE Transactions on Control Systems Technology. doi.org/10.1109/TCST.2015.2478077
Ruppert, M.G., et al. (2019) Multimodal atomic force microscopy with optimized higher eigenmode sensitivity using on-chip piezoelectric actuation and sensing. Nanotechnology. doi.org/10.1088/1361-6528/aae40b
Ashby, P.D., et al (2020) Direct observation of nanoparticle-surfactant assembly and jamming at the water-oil interface. Science Advances. doi.org/10.1126/sciadv.abb8675
Duque, T. (2021) VIDEO: On the Line: Watching Nanoparticles Get in Shape.[Online] Berkeley Lab. Available at: https://newscenter.lbl.gov/2021/02/25/nanoparticles-get-in-shape/ (Accessed on 4 March 2021).
Disclaimer: The views expressed here are those of the author expressed in their private capacity and do not necessarily represent the views of AZoM.com Limited T/A AZoNetwork the owner and operator of this website. This disclaimer forms part of the Terms and conditions of use of this website.