Controlled by flexible process control software, the machines from ficonTEC become much more than just the sum of their parts.
ficonTEC has consistently retained a unique modular approach to machine design and this development path is true for the software as well as the hardware. ProcessControlMaster (PCM) is the user-friendly and process-orientated application software and control interface from ficonTEC. It is shipped with all multi-machine assembly lines and turn-key, ready-to-use machines.
PCM features an intuitive machine/process GUI and this includes all machine vision, system management and active positioning routines required to repeatably and reliably drive passive/active alignment and bonding process hardware. It is also fully enabled for automated electro-optical test and characterization tasks, including common tests such as spectral measurements, temperature dependence measurements, optical power insertion losses and electrical/optical bandwidth, and also for more complex modular instrumentation, for example optical switches, multi-channel power meters, tunable laser sources, etc.
Already, flexible and scalable options enable customized assembly and testing solutions that are suitable for early device developments, the introduction of new products and for production. PCM is already tried-and-tested in high-volume environments and has already addressed the problem of increasingly complex combined electro-optical testing by transitioning to more integrated photonic devices.
Testing protocols and automated testing sequences benefit from direct interfacing to an SQL database. This provides the user with access to statistical analysis of the data in order to meet traceability requirements.
Finally, PCM allows for as much or as little operator intervention as required and can even be used remotely, from fully flexible, to fully automatic, to fully remote.
.jpg)
.jpg)
Key Features
- Advanced editable process sequencing
- Fully-configurable assembly and testing processes
- Pre-loaded with algorithms for machine vision and passive/active assembly
- Recipe-based management of process parameters
- Component tracking from input/output trays and wafers
- SW drivers for direct interfacing to a wide range of instrumentation
- SQL database storage of process parameters and component data
- Flexible data import and export for process/yield monitoring
- System-wide implementation across all machines, for consistent ‘look & feel’
- Remote service and software upgrades via internet
Process Optimization
The process sequence and cycle time can be optimized by collaborating closely on the specific manufacturing steps.
ficonTEC can help customers with their process optimization at all stages of realization and development as volume requirements increase. By working closely with our customers, we can combine our own extensive experience with technical process control expertise to assist in the production process design, including those aspects relating to software control. This is particularly important when translating manual assembly and testing protocols during the transition from prototyping/low volume to full mass production.
.jpg)
The PCM software platform provides adaptable and powerful process sequencing and tuning that can then be further optimized after quantification, for example by drawing on the statistical data stored in the SQL database. Cycle time, cost per item, device performance and yield can all be optimized within the parameter space allowed by the production process. This can be done within a single cell machine or across entire production lines that comprise multiple in-line machines.
Lastly, a Revision Control Server (RCS) can be implemented to synchronize process parameters across all lines for high-volume demands that employ multiple identical lines. This allows for maximum repeatability and also consistency of yield and performance. The RCS can also be managed locally or remotely and the latter has obvious benefits for global players in the photonics market.
ficonTEC provides a tried-and-tested and reliable route to high-volume manufacturing when taken together – i.e. by starting to optimize each step from the design phase, utilizing high levels of advanced automation for even the most demanding assembly tasks, introducing innovative processes, and combining it all with tried-and-tested software control.
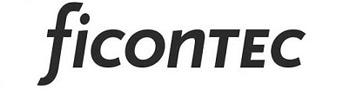
This information has been sourced, reviewed and adapted from materials provided by ficonTEC Service GmbH.
For more information on this source, please visit ficonTEC Service GmbH.