One of the most common questions asked is, “Why do I need a beam profiler and what basic or specific tools and methods do I need to profile my beam?" Specialized tools are needed by all industries in order to be effective and efficient; the laser industry is no different.
Laser operators typically validate the average energy or power and, if everything is in order, put their laser back into service. This measurement can be effortlessly performed using a power meter or interface module combined with an energy/power sensor.
.jpg)
Figure 1. Vega power meter coupled with 10 kW water cooled power sensor.
Beyond knowing energy or power, most laser operators and owners have never observed their beam in real time, because most lasers cannot be seen by the human eye. Users rely on the certification sheet that accompanies their laser when new and assume that the laser will remain stable over time.
Similarly, many industries have to develop products and comments with a high degree of precision, which makes it essential to keep traceability records and data to prove that the process is in control and producing at spec during a manufacturing campaign.
This means, a reproducible, accurate, and reliable method is required by engineering and quality teams to characterize beam structure, i.e. 3D and 2D tomography, spacial intensity, centroid location, diameter, etc. The teams know that variables such as beam propagation, energy density, concentration, and collimation have a profound impact on overall process consistency and beam quality.
Before the advent of digital profiling, if a “laser jock” wanted to know what the beam looked like, a number of different, and to some extent primitive techniques are used, such as a chunk of drywall, targeted reflections, burn paper or photographic film, wooden blocks or tongue depressors, or scrap pieces metal or aluminum.
Also, acrylic blocks (acrylic mode burns) were used by “sophisticated” operators. Although these techniques did yield some results, they were cursory and subjective at best. Safety, reproducibility, accuracy, precision were lacking.
With advancements in laser science and photonics, there have also been equal developments in the means for enhanced digital laser profiling techniques and measurement. This article discusses the basic steps and key considerations essential to identify and use a camera profiling system (beam dump, attenuator, and arrayed camera).
The discussion presented here is by no means all-inclusive; a beam can be profiled in a number of ways. However, the profiling system described here is an effective and ideal way to achieve high precision qualitative and quantitative data, which when correctly used (below 400 Watts) can help laser operators in characterizing and optimizing their laser system with safety, reproducibility, accuracy, and precision.
.jpg)
Figure 2. Example of drywall (left) and acrylic mode burn.
A wide range of lasers are currently used to cover the entire electromagnetic spectrum - ultraviolet to beyond far infrared.
.jpg)
Figure 3. Electromagnetic spectrum.
However, profiling technology has not advanced to the point that a researcher or laser operator can exclusively rely on a single profiling system or tool to measure every type or power of laser. So far, a one size fits all solution, application, or method has not been developed or commercialized.
The basic steps required to identify what is considered a common or standard profiling set-up are further discussed in the article. The first order of business is to choose a suitable camera for the job and this is best accomplished by addressing the following questions.
Question 1 – Wavelength
What specific wavelength or spectral response do users want to measure? Laser wavelength(s) can range from about 157 nm in the Ultraviolet to 1 mm and beyond in the Far-IR. Most detectors used in slit profilers and camera only cover a narrow specific range within this spectrum.
Detectors are usually made of CMOS, CCD, single element or multiplexed array, pyroelectric, InGaAs, Germanium, Silicon, etc. Most of these detectors come with different pixel spacing and size active areas, the degree of which will dictate accuracy, cost, and resolution. As mentioned earlier, there is not a one size fits all detector.
Question 2 – Average Power
In most cases, the entire laser beam will be interacting with or impinging on the surface of the cameras detector. The average power of the laser being evaluated should be known beforehand, as this information will help to determine the level of attenuation needed to protect the camera array or detector element.
Regardless of detector type, most cameras need some degree of attenuation. Scanning slit profilers can be the exception, based on the combination of average power and focus spot size, since the rotating slit provides a “natural” level of attenuation. Additional attenuation, when needed, can be achieved with either a beam splitter(s) or other filter components.
Recently, non-contact pass-through focus spot and position camera systems have been developed which employ the principle of Rayleigh scattering, which allows operators to profile their beams without external attenuation.
.jpg)
Figure 4. BeamWatch®, noncontact, focus spot size and position monitor.
Question 3 – Beam Size
It is necessary to know both focused and collimated spot sizes as these dictate the size detector (active area) that will be needed. Profiling can be carried out on most beam sizes and shapes with and without additional optical manipulation or enhancement.
Most Ophir-Spiricon arrayed cameras have the potential to image a beam as small as 40 microns, while a rotating slit profiler can accommodate beams between 7 microns to 6 mm. Some detectors are large enough to profile beams as large as 24 mm x 35 mm (Ophir-Spiricon L11059 camera).
Question 4 – CW or Pulsed
A CW or pulsed laser source can be effectively profiled with a single element or multiplexed array camera. If a laser is pulsed, the camera may need to be synced to the laser to achieve a stable beam profile. This is effortlessly accomplished by using either an optical trigger or trigger cable input up to the repetition rate of the camera.
A repetition rate above 10 khz is needed by the scanning slit profiler to get a stable profile. Focused spots may require repetition rates approaching several hundred kHZ for the scanning slit devices.
BeamGage® software and cameras have a built-in video trigger that enables users to capture pulses that go beyond a pre-selected threshold up to several hertz. Cameras have a set frame rate and any beams sampled above that rate will be averaging a series of pulses.
Let’s Profile
For the purpose of this article, a laser is profiled with the following parameters:
- Focus Spot = 200 microns
- Wavelength = 1064 nm
- CW or pulsed = Continuous wave
- Collimated spot size = 2 mm
- Average power = 40 Watts
Proposed Method:
Ophir-Spiricon SP Series USB camera, StarBright power meter, LBS-300-NIR Beam Splitter, and a 50(150)A-BB-26 general purpose power sensor.
Step 1 – Camera Selection
Either a rotating slit profiler (NanoScan Pyro/9/5) or USB Silicon CCD camera (SP Series) can be used to image a laser with a wavelength of 1064 nm. The USB SP camera is recommended for the best image resolution. The NanoScan Pyro/9/5 is considered the best solution to evaluate the focus spot.
.jpg)
Figure 5. SP Series Camera (left) and NanoScan Rotating Slit Profiler (right).
Step 2 - Attenuation
What does attenuation mean in the context of profiling? It is a way of redirecting or filtering out the overall energy intensity of a laser before the beam impinges on the imaging detector. Based on the laser and its end application, peak and average power levels can range anywhere between the pico watt level to well beyond the multi-kilowatts level.
So, attenuation is extremely important to help ensure that a laser’s energy is reduced to a safe and manageable level before the beam encounters or impinges on the detector array or camera detector.
The degree of attenuation differs based on the camera and method being used, i.e., slit, camera array, etc., and also the detector robustness. The power level needs to be somewhere at or below the milliwatt range for most detectors.
Rotating slit profilers and pyrocams can accommodate much greater levels. The most common way to effectively attenuate a laser beam is using metalized Inconel filters, a neutral density (ND) or beam splitter(s), or a combination of these.
.jpg)
Figure 6. LBS-300 Beam Splitter Configured with Generic Camera.
Step 3 – Power/Energy Readings and Waste Beam Management
In this example, a LBS-300-NIR beam splitter is used to attenuate the beam. The LBS-300-NIR is designed to dump or redirect more than 99% of the laser energy passing through it. A way of dealing with the waste beam is required, because the by-passed laser energy may be quite concentrated.
Many different methods are available. A piece of scrap metal is used by some operators, while other operators use a power/energy sensor, i.e., 50(150)A-BB-26 general purpose power sensor. The recommended method is to use an energy/power sensor combined with either an interface module or a power meter.
It is then possible to correlate this information in real time directly to the tomographic profiling image. Different models of power meters and interface modules are available with a wide range of features with different sizes and types of energy/power sensor heads to accommodate all sizes and types of lasers. The best sensor for a given application can be identified using the Ophir-Spiricon Sensor Finder Tool.
.jpg)
Figure 7. Example of Sensor Finder results.
Step 4 – Data Analysis
All Ophir-Spiricon profiling systems are available as a system and are interacted with the suitable software, in this case NanoScan (slit profiler) or BeamGage® (arrayed camera).
BeamGage was specifically developed to address the profiling requirements of all industry user and research groups. This easy-to-use software has customizable features to assist the end user in collecting real-time critical data.
The most common measurements tend to be divergence, pointing stability, centroid location, ellipticity, and diameter. However, there are many more to choose from. The Ultracal® algorithm is one of the key features not found in Ophir’s competitor’s software products.
When used properly, the Ultracal® algorithm increases measurement accuracy by eliminating background signal interference. BeamGage also has a broad based statistical analysis tool set and an embedded BeamMaker beam simulator program, which enables the user to practice using the program without being on an active laser source.
.jpg)
Figure 8. Example of a “typical” profiling set-up highlighting a power meter & sensor, camera, and software.
.jpg)
Figure 9. Typical BeamGage® user interface.
Do users need to profile? The answer is yes. The marketplace will continue to demand higher and higher levels of perfection and precision; having the right tools to understand a given process and maintain proper control, its nuances and variabilities will be paramount.
The effects of subcomponent degradation and laser pointing instabilities can be monitored and measured by using the correct profiling tools. It will be easy to detect and negate the understanding of modal pattern variations, misalignment and alignment of optics, etc.
Ophir Photonics is a global leader in providing these tools.
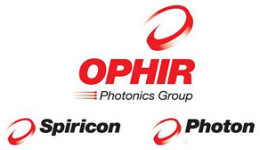
This information has been sourced, reviewed and adapted from materials provided by Ophir Photonics Group
For more information on this source, please visit Ophir Photonics Group