Working for many years in laser marking and engraving could leave users with the mindset of "if the laser is making a mark, when why check the performance of the laser?"
This article discusses how this mindset could result in a loss of time and money for many different laser applications.
Industrial laser markers have found their use in nearly every market segment. For the purpose of this article laser marking involves multiple processes such as ablating, etching, annealing, and engraving. Some marks are made using a mechanical process, some made using a thermal process, and some using a chemical process. Laser marking can be carried out on different materials, such as plastics, organic materials, metals, and painted surfaces. Permanent marks can be made on these materials using lasers in multiple different ways.
The method of developing lasers used for marking is very similar to other laser technologies. High-powered Nd:YAG lasers (in the order of 100s of Watts) have been the foundation of industrial part marking for many years (Figure 1). Even today, they continue to be used in conditions requiring raw horsepower. However, the fiber laser has found its way into laser part marking due to its high beam quality and comparatively low overall cost.
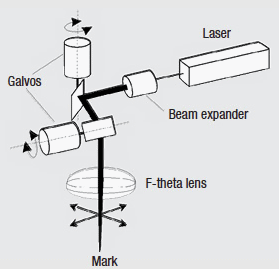
Figure 1. Example of typical laser marking system.
A hybrid of the Nd:YAG lasers and the fiber laser also provides stable and high-quality beams, and ensures higher flexibility for the end user. A diode-pumped crystal with a fiber-delivery system is used as the laser source. This source homogenizes the beam that is delivered for the process. The laser marking technologies are equally as interesting as the development of laser welding, cutting, additive manufacturing, and other laser applications and technologies.
As all lasers are made of matter, the matter may be degraded and fail after some time, causing physical changes to the laser system, consequently changing the beam output power or energy and the beam quality, or even the size and/or shape of the beam. Due to this natural event, the performance of the laser systems should be monitored in the same way as any other laser application. If the performance of the laser is not monitored, after a point in time the user may have to face the adversities of part replacement, expensive technician visits, and production down time.
This article discusses the timeframe for making laser performance measurements to make sure that the laser application works successfully for a longer period of time.
Deep Engraving
Deep engraving is carried out for specific part marks to make sure that the mark is clearly visible and permanent for a longer period of time (Figure 2). In certain cases, the agencies supervising the product manufacture regulate the specifications related to the depth of the marks.
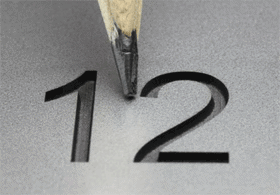
Figure 2. Example of deep laser engraving.
The marking depth is under high scrutiny because at times the part marks are covered with anodizing or a coating. As time is precious and costly, the performance of the laser decides how fast the part is marked to the desired depth. To ensure that the laser process provides a consistently high throughput, the laser energy or output power per pulse should be constantly monitored, not only during the laser application development, but also after the laser enters the production process. It is highly important to measure the laser spot size consistency, because the energy density or power at the workpiece is determined by the area within the laser spot. Any change in the spot size or the laser energy/power changes the laser process.
Plastics Marking
The laser is also used for rapid part marking during plastics marking. The laser engraves a high-contrast permanent mark within fractions of a second if the chemical composition of the plastic is suitable, although this may again depend on the content of the mark. Great care and a greater amount of time go into the application of the laser in such processes to ensure process optimization, because the laser is generally used in a production line that requires a high throughput. To realize desirable results, the power density of laser, i.e. laser power with regard to the beam size, should be optimized for any material processing, e.g. plastic marking, that involves the use of laser.
A laser applications engineer can adopt many clever tricks while performing plastic marking. One trick for achieving quicker fill speeds and a higher-contrast mark is increasing the spot size either by applying the laser slightly off focus or through optical configuration. The problem lies in transferring the process from the laser in which the application was developed to the laser that enters the production. This problem can be overcome by carrying out laser measurements. Ensuring the result of the applications lab’s laser is similar to the production laser, by measuring the measurement and viewing of the laser’s spot size and the laser’s energy/power. If there are hindrances in production, these measurements can be benificial to set the performance of the production laser to the same as that of the original laser.
Conclusion
Similar to maintenance and performance issues of lasers, the laser marking applications do have their own approaches and issues as they are nothing but applications of lasers. If the laser’s performance characteristics are not measured and set to optimized settings for consistent performance, then the expensive equipment involving these lasers may become vulnerable. This may also cause loss of money and precious time. The measurement of laser beam characteristics ensures highly successful and efficient laser part marking.
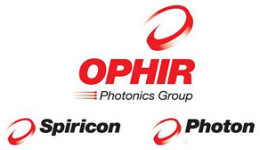
This information has been sourced, reviewed and adapted from materials provided by Ophir Optronics Group.
For more information on this source, please visit Ophir Photonics Group.