Due to the number of technologies available today, users are swamped with tons of data, especially in areas of business and marketing. The same is true when measuring lasers too. Although many items can be measured, taking measurements make sense only if the data collected is used for some productive purpose.
For instance, in business, there is plenty of statistics and information available regarding the user’s business; however, one has to prudently select only the data that will be useful for the growth of the business. Likewise, in laser usage, there are many ways to perform laser measurements, and many types of values that can be checked. The crucial decision is to figure out which measurements will help enhance laser efficiency.
The Most Important Laser Parameter to Measure
The solution is based on the user’s application, how the laser system is used, the user’s prime concerns and so on, but the user simply requires a key performance indicator (KPI). KPIs are mostly dependent on factors very important to the user. However, it is suggested that measuring power and M-Squared (M²) is an ideal starting point. Laser profiling will provide a lot of information, but M² is the most suitable area to begin if only one number is required to establish the quality of a laser.
What is M²?
The technical definition can be found in the Ophir Photonics’ M² tutorial. This section will focus on the importance of measuring M² rather than how M² is measured.
If a Gaussian-type laser is being used, it is recommended to have the laser closer to a perfect Gaussian to obtain better results. M² defines the closeness of the laser to a Gaussian. M² = 1 for a perfect Gaussian beam, and M² > 1 for all other laser beams (Figure 1).

Figure 1. M² = 1 when the laser beam is a perfect Gaussian beam
Based on the industry and application, M² values of 1.1, 1.2, and even up to 1.5, can be considered as high quality lasers. However, this value would depend upon the power as well. M² will generally be higher, even reaching up to values of 5-10, for higher powers, but these will in turn offer lower beam quality.
Significance of Using Near-Gaussian Lasers
The closer the laser is to a perfect Gaussian shape, the tighter it can be focused. Were you cutting steel, this would mean a smaller kerf, thereby reducing material wastage. Likewise, the output would be more precise when processing intricate medical devices. The key point is that a very tightly focused laser beam operating at a lower power can offer users a higher power density than a larger beam at higher power.
Conclusion
To all its material processing customers, Ophir Photonics recommends that if more power is required, instead of increasing the throttle, the beam profile needs to be measured.
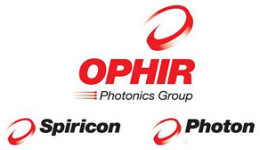
This information has been sourced, reviewed and adapted from materials provided by Ophir Photonics Group.
For more information on this source, please visit Ophir Photonics Group.