W. Edwards Deming stated “If you can't measure it, you can't control it," and "You cannot inspect quality into the product; it is already there." It is more important to focus on value addition once there is the assurance that the prior process was performed appropriately and as per specifications, instead of inspecting-in quality.
Since the mid 80’s, the number of machine vision cameras deployed in assembly stations and manufacturing plants has been truly huge. These cameras are present in almost all sectors, where there are a large number of users such as pharmaceutical, automotive, aerospace, medical devices, electronics, and practically every industry that is into the manufacture of some product. The reason for the extensive use of machine vision cameras is that value addition to a good component brings down the price of goods, rendering the business more profitable. Machine vision is one of the reasons that the US has reiterated itself as a leader in manufacturing high-quality products at affordable prices.
Measuring the Quality of Laser Beam
There are machine vision systems available that determine and monitor the quality of a laser beam. The output of a laser beam is similar to a light bulb and varies continuously. Lasers are being deployed in the manufacture of highly accurate and reliable components in the automotive, aerospace and electronics industry. There is a need for reliability and accuracy in the laser beam over time. However, manufacturers have not understood the importance of periodic or on-line measurement of the laser beam.
The reasons why they are not interested in periodic measurement of the laser beam are:
- They have never measured it from the time it was installed and assume it is fine
- Periodic service maintenance is carried out and it is assumed that measurements were performed then
- When the quality of components actually deteriorate, they would call for service technicians after shutting down the line
The Problem with Burn Paper
The present techniques used for measuring the laser are
Burn paper is one-dimensional, or in other words, the resulting burn is either burnt or not burnt. A burn does not have any spatial depth. A laser beam’s power cross section however, is 3D and not 1D. The data on how the laser is going to weld or process depends on the shape of the power cross section. The burn paper is not dimensionally precise, and has a restricted spatial depth. The burn occurs when there is sufficient power to burn — measuring it for obtaining useful data about power density is worthless.
The Problem with Acrylic Burns
For representing the profile in three-dimensions, certain manufacturers use acrylic plastic. Firstly, burning of acrylic plastic results in carcinogenic fumes, so companies keen on being OSHA compliant will surely want to avoid it. However, certain manufacturers do not seem to care about this issue, stating that fans vent the fumes to the outside, so there is no threat to the operator. Some of them claim that they adopt this procedure very rarely so that the operator is not in the fumes frequently.
Lasers Change Over Time
In technical terms, an acrylic block cannot be created with a single laser pulse or in the case of CW it has to be more that few seconds. Users feel that the first laser pulse appears as the 100th pulse, or the first millisecond CW power distribution seems exactly as the power distribution when the 1st second or the 2nd second is over.
However, this is false, particularly if comparing the initial laser output to that after having the laser on for a specific time period. In fact, in order to sell profilers, it is important to provide an on-site demo so that customers can accept that their lasers are not performing to the mark. Even after demonstrations, manufacturers still ask why they need to go for a change as the methodology that they have been following until now seems to work.
Change Because Technology Has Changed
The reason why it is important to change is that now we understand some laser performance characteristics, things that were not possible previously can now be accomplished, some of which are:
- Predicting the future, similar to a machine vision system. The knowledge of some measurements of the laser beam will help forecast periodically, and over a specific time period, when periodic laser maintenance is required. It is possible to schedule the downtime, and be sure there will be no occurrence of a catastrophic line shutdown.
- When the same laser is deployed for different processes, the beam adjustments can be optimized to every process.
- A valuable argument is that once the optics are dirty, they are changed. There are very small differences from the first day to the change out day. How does that impact the manufacture of a reliable product? Beam delivery parameters change over time until the optics are changed. Change does happen, but it is essential to measure so that one realizes when the change reaches a point where it is not acceptable anymore.
Calculating ROI
Manufacturers are ready to accept this electronic method of beam monitoring, but believe that it is very costly. Hence, an understanding of the ROI is important. The product value, the number made per unit of time, scrap cost, how many need to be made before identifying a problem and the cost of unscheduled down time need to be considered. Using the ROI calculator, it is possible to easily predict the payback time.
If you have over one laser in production, and the welding is being performed using the laser for one shift at least for a precision-product, the payback will be less than 16.7 months. There are still arguments, it is too small, too big, is not suitable and that they are not used to the data obtained.
Yet, this surely does not imply that Dr Deming’s "measure it and control the process" is not appropriate for manufacturers deploying lasers. Manufacturers need to be alert and adopt this new technique for improving their processes, particularly at a time where there are so many significant technological advancements.
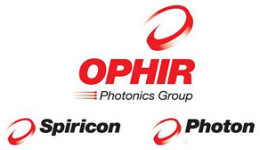
This information has been sourced, reviewed and adapted from materials provided by Ophir Photonics Group.
For more information on this source, please visit Ophir Photonics Group.