There is a lot of confusion surrounding the terms “integration time” and “response time” of energy sensors. This article will define these terms with respect to Ophir’s pyroelectric “Smart Sensors.”
A pyroelectric sensor is equipped with a pyroelectric crystal. An absorbed laser pulse is converted into a heat pulse in the crystal, which generates an electric charge proportional to the amount of heat absorbed.
As the two crystal surfaces are coated with metal, the coated crystal acts as a capacitor, and total charge generated is collected, meaning the response is independent of beam position or size. This turns into a voltage pulse. This pulse value is then determined. A schematic view is shown in Figure 1.

Figure 1. Schematic view of a pyroelectric sensor
Response Time and Integration Time
The pyrolelectric sensor’s response time is based on the time taken for heat to penetrate the crystal and cause it to heat up. For metallic type pyro detectors, this time is in the order of milliseconds, and so the metallic type can perform at an increased repetition rate. The response time is in the order of milliseconds, with a considerably lesser repetition rate in the BB and BF black coated types.
The time taken for the voltage pulse to increase, and then stabilize so that it can be measured, is termed as the integration time. Once the integration time period is over, the voltage is again set at zero so that the sensor can take the following pulse.
The time taken for this reset is based on the sensor’s thermal relaxation time and on the electronic device’s RC time constant. To explain this more clearly, the integration time is the time span during which the measurement of a particular pulse is carried out (Figure 2).

Figure 2. Response time and integration time
It is important to note that it is clear that selecting a specific “Maximum pulse width” setting ascertains the maximum pulse repetition rate, as observed in the specifications. For example, when the maximum pulse width is set by the user at 2 µs, the integration time gets automatically set. If,the pulse width is just 3 ns, the voltage will be held by the sensor for 2 µs as per this specific example, and the same is integrated, or in other words, stored and measured.
When the pulse is more than 2 µs, and the maximum pulse width is still set at 2 µs, a certain amount of the pulse is ignored or cut off, resulting in discrepancies in the final values. However, when the maximum pulse width setting is fixed at a value longer than the pulse width, the noise level increases. Typically, it is good to select the shortest “maximum pulse width” setting that is still a higher value than the pulse.
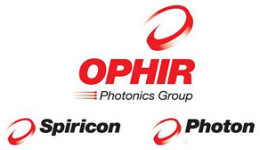
This information has been sourced, reviewed and adapted from materials provided by Ophir Photonics Group.
For more information on this source, please visit Ophir Photonics Group.