Optical processing is one of the foundations of precision manufacturing. It involves transforming materials like crystals, glass, and plastics into optical components, including prisms, lenses, and mirrors.
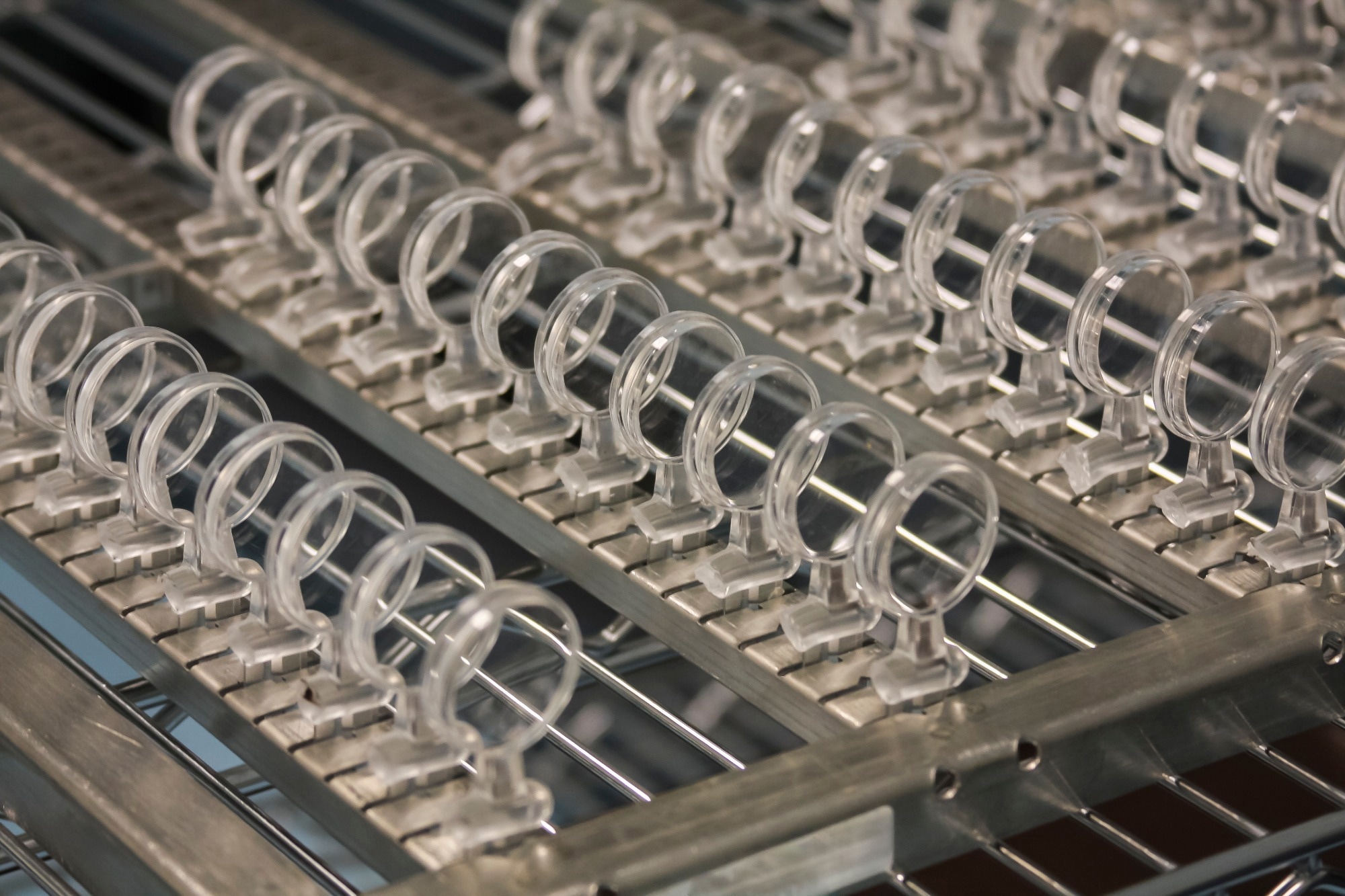
Image Credit: Susan Schmidt/Shutterstock.com
Employing technologies such as ultra-precision polishing, laser processing, optical coating, and computer-controlled surfacing, optical processing aids fields including consumer electronics, semiconductors, biomedical devices, and optical communications.
In 2020, the global optical and photonic components market was worth over $300 billion.
Precision Manufacturing
Optical processing starts with the raw materials and finishes with finely crafted optical components. The process involves cutting, grinding, fine grinding, polishing, and coating, with the aim of achieving strict dimensional and surface quality standards.
It is crucial for manufacturing components used in optical instruments, camera lenses, fiber optics, and laser devices. By combining traditional craftsmanship with modern automation technologies, precise light control is achieved, enabling accurate imaging and transmission.
Evolution of Optical Processing Technologies
Optical processing has significantly evolved, transitioning from manual methods to highly automated and precise techniques.
Early optical components were hand-crafted, a labor-intensive process with limited precision. In the early 20th century, mechanical methods were introduced, improving consistency and efficiency.
The development of CNC machines and laser technologies in the mid-20th and early 21st centuries revolutionized the production of optical components by enabling micron and nanometer-level precision.
The evolution of optical processing has been driven by increasing demand for high-precision and high-efficiency products across many industries.
Key Technologies in Optical Processing
Laser Processing
Laser processing utilizes high-energy laser beams for precise cutting, marking, welding, and engraving on various materials, including glass and metals. The technique is non-contact, making it particularly beneficial for processing brittle materials and high-melting-point metals. As a result, laser processing is indispensable for the electronics, automotive, and aerospace industries.
Ultra-Precision Polishing (UPP)
Techniques like magnetic rheological finishing are vital for producing precise and smooth surfaces, particularly on large or aspherical optical elements, such as those used in astronomical telescopes.
Optical Coating
Optical coating involves applying thin layers of material to optical components to enhance their properties, including transmission, reflection, and polarization. For example, anti-reflective coatings reduce surface reflections, improving the clarity of cameras and eyeglasses.
Computer-Controlled Optical Surfacing (CCOS)
By integrating CAM, CAD, and precision machining, CCOS enables the production of complex optical components with high surface quality, such as freeform mirrors and aspheric lenses.
Applications of Optical Processing
- Semiconductor Manufacturing: Optical processing is vital in photolithography and inspection processes, essential for creating nanometer-scale circuits on silicon wafers.
Consumer Electronics: High-quality optics are crucial for devices like smartphones and AR/VR systems, enhancing image capture and user experience.
Optical Communications: Precision optical components ensure efficient and reliable data transmission in optical networks.
Biomedical Devices: The production of high-precision imaging equipment, such as microscopes and diagnostic tools, depends heavily on advanced optical processing.
Outlook for Optical Processing
The optical processing industry is approaching the era of extreme precision and size diversity, from large-diameter mirrors to micron-scale structures.
A growing emphasis is being placed on integrating shape precision with optical performance, particularly in high-performance products such as diffractive optical elements and aspheric lenses.
Additionally, integrating processing and inspection technologies has become more commonplace, ensuring that products meet strict quality standards in real time.
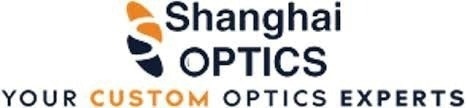
This information has been sourced, reviewed and adapted from materials provided by Shanghai Optics.
For more information on this source, please visit Shanghai Optics.