Since its invention in the 1980s, the atomic force microscope (AFM) has become indispensable for nanoscale imaging and metrology across scientific fields. At the heart of the AFM lies a host of precision components working in unison to acquire high-resolution topological images.
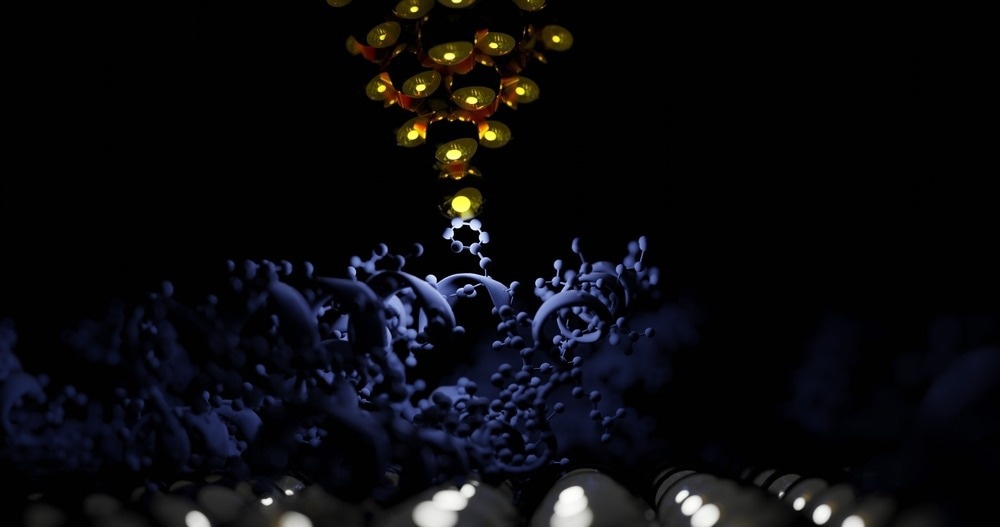
Image Credit: sanjaya viraj bandara/Shutterstock.com
What is an AFM?
The atomic force microscope (AFM) is a versatile and powerful scanning probe microscope capable of imaging surfaces and measuring physical properties, dimensions, magnetism, and surface roughness at the atomic scale.
The AFM scans its sharp probe over the sample surface, using piezoelectric positioners to track tiny tip-sample forces (pico-Newtons), generating high-resolution images and precise measurements.
Invented in the 1980s, the AFM can achieve lateral resolution down to a few nanometers and vertical resolution under 35 picometers, enabling atomic-scale topographical mapping and measurement of various surface properties.
The AFM's high resolution, non-destructive, 3D imaging and atomic manipulation capabilities have enabled revolutionary advances in nanoscale metrology and characterization across scientific and technological fields.
The Underlying Principle of the AFM System
The working principle of an atomic force microscopy (AFM) system involves using a sharp probe attached to a cantilever to scan across a sample surface. The probe's motion is detected and recorded to create a three-dimensional image of the surface.
The AFM operates based on three main principles: surface sensing, detection, and imaging.
Surface sensing is achieved by the cantilever, which has a sharp tip that interacts with the sample surface. When the tip approaches the surface, attractive van der Waals forces between the surface and tip cause the cantilever to deflect toward the surface. However, repulsive forces take over as the tip gets closer and makes contact, causing the cantilever to deflect from the surface.
Detection is accomplished using a laser beam directed at the top of the cantilever. When the cantilever deflects towards or away from the surface, the reflected laser beam undergoes slight changes in direction. These changes are monitored by a position-sensitive photodiode (PSPD), which records the deflection and changes in the reflected beam.
Imaging involves scanning the cantilever over a specific area of interest on the sample surface. The elevated and recessed features of the surface influence the deflection of the cantilever, which the PSPD detects. By maintaining a constant laser position through a feedback loop that controls the tip height above the surface, the AFM generates an accurate topographic map of the surface features.
Imaging Modes of the AFM System
AFM has three imaging modes: static or contact, non-contact, and intermittent (tapping).
Static or Contact Mode
AFM's contact mode involves the tip continuously in contact with the sample surface, allowing for surface imaging. Repulsive van der Waals forces prevail during contact, while attractive van der Waals forces dominate as the tip moves away from the surface.
This mode is suitable for rough and rigid surfaces, but care must be taken with soft samples to avoid deformation or damage. A feedback system maintains a constant deflection and interaction force, and measurements can be performed in aqueous environments to reduce the applied force.
Tapping Mode
Tapping mode in AFM involves oscillating the cantilever at its resonance frequency and lightly tapping the sample surface during scanning. Constant tip-sample interaction is achieved by monitoring the oscillation amplitude, influencing image acquisition and contrast through parameters such as height, phase signals, and amplitude.
Tapping mode is useful for delicate samples and provides higher resolution than non-contact mode, but it requires slower scanning and is more challenging in liquid environments.
Non-Contact Mode
The non-contact mode in AFM involves oscillating the probe above the sample surface without physical contact. Weak attractive forces between the tip and surface are detected through changes in cantilever oscillation frequency.
This mode offers low surface force and extended probe lifespan but has reduced resolution and sensitivity to surface contaminants. It often requires careful environmental control, such as operating in an ultra-high vacuum.
Main Components of the AFM System
Scanning probe: Cantilever and Tips
The scanning probe in AFM consists of a cantilever with micrometer-scale dimensions and a nanometer-sized tip, where the cantilever serves as a flexible beam supporting the probe and enabling its free movement.
The properties of an AFM probe, including length, shape, and material (silicon or silicon nitride), determine its performance characteristics, such as stiffness, flexibility, resolution, and chemical sensitivity.
Selecting the right probe properties allows the optimization of AFM imaging and measurements for particular samples and experiments.
Transducers
The cantilever's mechanical motion in AFM is generated by electromechanical transducers, commonly using a piezoelectric ceramic material. Piezoelectric materials change their shape when subjected to an electric field, and the amount and direction of this motion determine the AFM measurements.
Force Sensor
The AFM system uses a force sensor to measure the minute forces between the probe and the sample surface. The motion of the cantilever is detected using the light lever method, where light reflects off the backside of the cantilever onto a photodetector to measure the motion.
The image quality and operation of AFM heavily rely on these force interactions, which can be calculated by knowing the cantilever's stiffness and using Hooke's law:
F = -kx
Where:
F = force
k = cantilever stiffness
x = deflection distance
Feedback Loop Control
The feedback loop control in AFM involves using a laser deflector to regulate force interactions and probe positions.
A laser beam reflects off the cantilever into a photodetector, and as the tip scans the surface, the laser spot position shifts, feeding back to the z-piezo controls to adjust tip height in real time, maintaining the desired force. This closed-loop feedback enables precise tracking and quantitative measurement by regulating the probe position relative to the sample topology.
Scanning Stage
The scanning stage is a platform designed to hold the sample and facilitate its movement relative to the probe.
It is usually constructed from a lightweight and rigid material, such as aluminum, and is equipped with precision motors or piezoelectric actuators capable of making highly precise and small incremental movements of the sample.
Control and Data Acquisition System
The AFM's control and data acquisition system uses computer hardware and software to direct the positioning of the probe and sample while processing the detector signal to generate surface maps and measurements.
This centralized computer system coordinates the instrument components and converts raw data into usable images and information.
Concluding Remarks
Despite its slow scanning speed and composition detection limitations, atomic force microscopy remains an invaluable and powerful tool for nanoscale imaging and measurement.
Its versatility and impact across scientific disciplines have elevated it from a research tool to essential product development and quality control device in industries.
AFM has revolutionized nanoscale metrology and will continue to drive advancements in nano research and technology. With its capabilities and ongoing advancements, AFM holds immense potential for shaping the future of scientific exploration at the atomic scale.
More from AZoOptics: Can AFM be used for Imaging in Liquids?
References and Further Reading
Eaton, P., & West, P. (2010). Atomic force microscopy. Oxford university press. Available from: https://www.uni-wuerzburg.de/fileadmin/1101-f-praktikum/2020/AFM/AFM_Theory__Practice_and_Application.pdf
Liu, S., & Wang, Y. (2010). Application of AFM in microbiology: a review. Scanning, 32(2), 61-73. https://doi.org/10.1002/sca.20173
MN Editors. (2023). Atomic Force Microscope (AFM) – Definition, Principle, Application. [Online]. Available from https://microbiologynote.com/atomic-force-microscope-afm/
Pavliček, N., & Gross, L. (2017). Generation, manipulation and characterization of molecules by atomic force microscopy. Nature Reviews Chemistry, 1(1), 0005. https://doi.org/10.1038/s41570-016-0005
Rao, R. (2021). Atomic Force Microscopy Explained: Principles, Construction, Working, and Applications. [Online]. Wevolver. Available from: https://www.wevolver.com/article/atomic-force-microscopy-explained-principles-construction-working-and-application
Disclaimer: The views expressed here are those of the author expressed in their private capacity and do not necessarily represent the views of AZoM.com Limited T/A AZoNetwork the owner and operator of this website. This disclaimer forms part of the Terms and conditions of use of this website.