Measuring technical mirrors is a constant challenge in the optics industry. With special sensors and measuring systems, Micro-Epsilon can help solve these tasks with the highest precision. With a deep understanding of the complexity and importance of surface characterisation of technical mirrors, Micro-Epsilon is pushing the boundaries of precision and optimising measurement processes for applications ranging from medical technology to aerospace, says Glenn Wedgbrow, Business Development Manager at Micro-Epsilon UK.
Image Credit: Micro-Epsilon UK
The surface characterisation of technical mirrors is of critical importance for manufacturers. In many cases, quality is still assessed by the human eye. As this work requires maximum concentration, it depends on the ability of the inspector on the day and leads to eye fatigue over time. As a result, employee performance fluctuates and not all existing parameters are reliably recognised. This means that reproducible quality is only possible to a limited extent.
Micro-Epsilon’s reflectCONTROL measurement system is an ideal solution here. It enables automated surface inspection of reflective or shiny objects with consistently high quality. The results are output in the form of 2D images and a 3D point cloud.
Advantages of 3D Technology
When high precision 3D measurements on glossy and shiny components are required, the reflectCONTROL sensor is the ideal choice. In particular, with flat surfaces, the reflectCONTROL technology impresses with its high measuring rates and nanometer accuracies. The 3D sensor uses the principle of phase-measuring deflectometry. It is characterised in particular by its extremely high z-axis resolution in the nanometer range. In combination with its large measuring range of approximately 170 mm x 160 mm, up to five million data points of the surface to be measured can be recorded within a few seconds. A conventional point sensor with an X-Y scan would need at least half an hour to do this.
The reflectCONTROL sensor is used, for example, for 3D shape detection of wafers in semiconductor production, quality inspection of flat glass, e.g. in smartphone production, and surface inspection of head-up displays.
Precise Measurement of Technical Mirrors
In many cases, manufacturers of technical mirrors use sensor solutions in which mirrors with a diameter of 100 mm are measured using around 16 sensors. The resulting measuring points are interpolated across the mirror surface to determine the respective deformation. These measuring methods are often only suitable to a limited extent for quality specifications in the nanometer range.
The reflectCONTROL sensor, on the other hand, captures the surface with up to five million data points, allowing the measuring object to be precisely reconstructed. An example of a measurement on a technical mirror can be found in Figure 1.
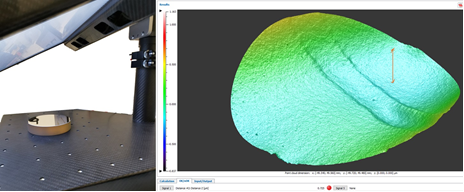
Fig 1: Left: Real representation of the measurement; right: evaluation of the captured 3D surface. Image Credit: Micro-Epsilon UK
By removing the aspect ratio in image 1, the surface, which is only deformed by 725 nm, can be visualised with high precision. Both the groove-shaped indentation and the smallest particles on the mirror surface can be identified. In addition, the reflectCONTROL sensor also provides 2D images of the recorded surface, see Fig. 2 and Fig. 3.
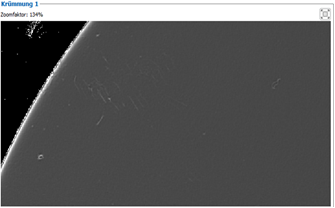
Fig 2: Curvature image of a reflective surface. Image Credit: Micro-Epsilon UK
Numerous surface deformations can be identified in the curvature image in Figure 2. Indentations such as scratches, dents, notches etc., as well as elevations such as pimples and granules can be visualised. All effects that change the reflectivity of the surface are shown in the amplitude image. Classic examples of this would be fingerprints or other soiling marks.
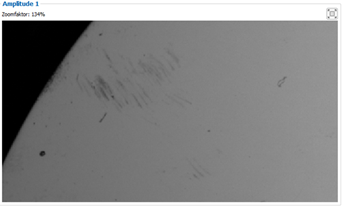
Fig 3: Amplitude image of the same reflective surface as in Fig 2. Image Credit: Micro-Epsilon UK
Measuring Principle of Phase-Measuring Deflectometry
The reflectCONTROL sensor works according to the principle of phase-measuring deflectometry. The method is particularly suitable for high precision defect detection and three-dimensional geometrical detection of flat reflective objects. With deflectometry, the surface itself is not examined but its optically distorted or intensity weakening effect, which shows itself in the mirror image of a pattern. In the process, a sine pattern is shown on a display and then the reflection of this pattern is recorded by cameras. A few images are taken with CCD cameras with a phase shift of the displayed pattern. The data obtained is processed using special algorithms to determine curvatures and intensity amplitudes over the entire surface. Deflectometry systems are superior to other optical methods in that the required local curvature, intensity and amplitude data are available over the entire area captured by the camera. The advantage of the stereo measuring system lies in the simultaneous image acquisition of two cameras from different directions. The combined evaluation of the data from both cameras enables a 3D reconstruction of the measuring object with nanometer precision.
Summary
By using phase-measuring deflectometry in the form of the reflectCONTROL sensor, even the smallest defects or deformations can be reliably detected. Particularly in the field of technical optics and mirrors, the process described here represents an outstanding opportunity to meet the high quality requirements in this area.