Optical Surfaces Ltd. has delivered five challenging lenses to AMOS, the prime contractor supplying the Time Delay Integration (TDI) optical corrector unit for the International Liquid Mirror Telescope (ILMT).
Due to be installed at Devasthal (India) the International Liquid Mirror Telescope is made up of three main components: a primary rotating mirror, a focal structure and a CCD camera with optical corrector. The ILMT uses Liquid Mirror technology whereby the primary mirror of the telescope is a rotating container with a highly-reflecting liquid (mercury) in it. The surface of the spinning liquid takes the shape of a paraboloid. As the primary mirror of the ILMT is parabolic, the off-axis imaging is distorted by spherical, coma and time delay integration (TDI) aberrations. In order to correct these off-axis aberrations and to increase as much as possible the field of view of the telescope, an optical corrector must be inserted before the CCD camera.
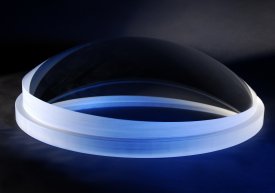
Stefan Denis, Project Manager at AMOS commented 'The lenses manufactured by Optical Surfaces are to be assembled into our TDI optical corrector, which - beside the basic field correction - aims at correcting for the trajectory of stars passing by at the zenith of the ILMT'. The supplied high precision lenses were of various sizes - the largest of which was a 465mm diameter steep meniscus. He added 'Optical Surfaces was selected for its well-known high-level quality in optical manufacturing, including off-axis and special shape optics'.
Dr Aris Kouris, Sales & Marketing Manager of Optical Surfaces Ltd commented 'We are pleased to have successfully completed and supplied critical optical components for such a prestigious project as the International Liquid Mirror Telescope'.
Reflecting on the challenges of producing the five challenging lenses for the TDI optical corrector he added 'the absence of any means of adjustment imposed by the system design and the accuracy that the elements had to be placed with respect to each other generated significant challenges in the manufacturing of these elements. Strict tolerances were required in many physical parameters including centre thickness, radii of curvature, relative positions and references. In addition, the lenses had to be machined with a wedge and decentre between the mechanical and the optical axis, while an accurately positioned reference slot would allow the precise positioning of the lenses within the system'. 'The strict manufacturing tolerances required careful planning and execution from the beginning to the end in order to ensure that all parameters would converge simultaneously to their target values'.
The size and depth of the larger meniscus lens meant that conventional polishing machines were not adequate to polish the two surfaces. Optical Surfaces designed and build a purpose-polishing machine to allow multiple accurate and synchronised motions (including an accurately defined swinging motion on the polishing tool) to generate the spherical surfaces with the correct radii of curvature and shape. After the polishing was complete, the lenses were machined to generate a wedge and decentre between the mechanical and optical axis. For that reason the polished lenses were placed accurately in position for the machining and several mechanical and optical reference surfaces were either attached or generated on the substrates. The latter gave OS the flexibility and the capability to remove and re-place the lenses back at their exact location during machining. The multiple references gave confidence on the positioning process while eliminating single points of failure. Finally, it allowed Optical Surfaces to verify the validity of the method, before and after completion, by using the CMM measuring capability at Rutherford Metrology Facility (UK).
AMOS* is an international leader in the engineering and manufacturing of high accuracy Advanced Mechanical and Optical Systems for space and astronomy projects. Based in Liege (Belgium) - AMOS employs over 75 skilled personnel. For further information please visit www.amos.be.
Optical Surfaces Ltd. has been producing optical components and systems for more than 45 years and is now accepted as one of Europe's leading manufacturers of high-precision optics for ground and satellite based telescope systems. The company's ISO 9001-2000 approved manufacturing facility provides the flexible resources to supply from single specialist requirements to OEM quantities. All high precision optics are provided with a complete quality test assurance report.