In this interview, Dr. Erik Novak, from 4D TechnologyTM, talks to AZoM about 4D dynamic interferometry.
To begin, can you give us an introduction to what dynamic interferometry is and how it can be done?
In the past, the largest limitation of interferometers was the need to acquire multiple camera frames to achieve the proper signal, making such systems sensitive to vibration and air turbulence. Traditional, temporal phase-shifting interferometers are particularly sensitive to vibration because interferometric data frames are acquired sequentially, over hundreds of milliseconds. The exposure time is long enough for vibration and air turbulence to cause unpredictable phase shifts between the data frames.
The measurement accuracy is significantly reduced, and sometimes the environment is sufficiently bad that the measurement cannot be performed at all. Dynamic Interferometry® makes it possible to acquire all measurement data simultaneously, with such a short acquisition time that vibration and turbulence are effectively frozen. In 4D Technology's dynamic interferometers, a micro polarizer sensor array is used to spatially encode the captured interferometric image with four-phase shifts of 0, 90, 180, and 270 degrees—enabling a single frame, quantitative phase measurement.
Why is high-speed surface data acquisition significant?
With information acquired in microseconds, instruments can be mounted on robots, take measurements of continuously moving parts on a conveyor belt, or be hand-held—since a well-controlled lab environment is no longer needed to achieve good data. Thus, metrology can go directly into manufacturing lines or the shop floor, enabling real-time feedback to the production process.
Continually, why is dynamic interferometry significant in terms of getting metrology measurements in adverse conditions (such as in a vacuum or a production environment)?
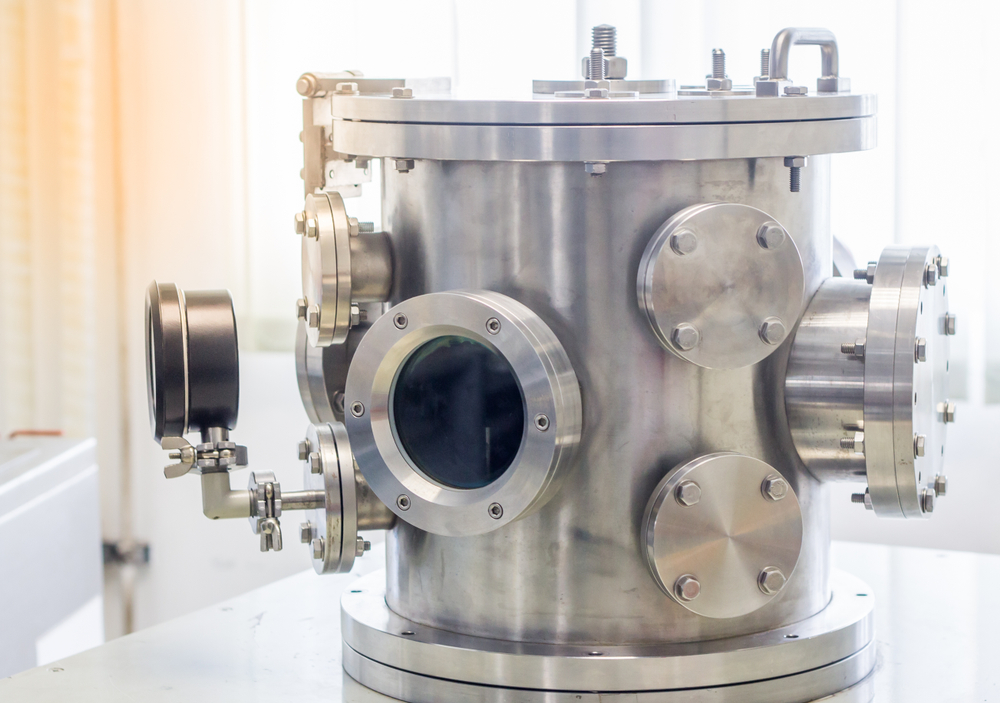
Image Credit: Shutterstock/Ariyaporn chumkong
The above also applies to measuring into vacuum chambers, where the measuring instrument and test piece are physically separated and, therefore, subject to different vibrations and other environmental changes. The vibration caused by a vacuum pump is an example. With vibration-immune measurements, this doesn't pose a problem for achieving accurate results.
Can you tell us about some of the dynamic systems applications (such as shop floors and cleanrooms)?
Dynamic systems can be mounted in machining centers, on robotic arms for rapid automated inspection of various parts, and also can be used in a hand-held manner. Makers of large telescope optics, like the James Webb Space Telescope, can measure their huge optics across large spaces.
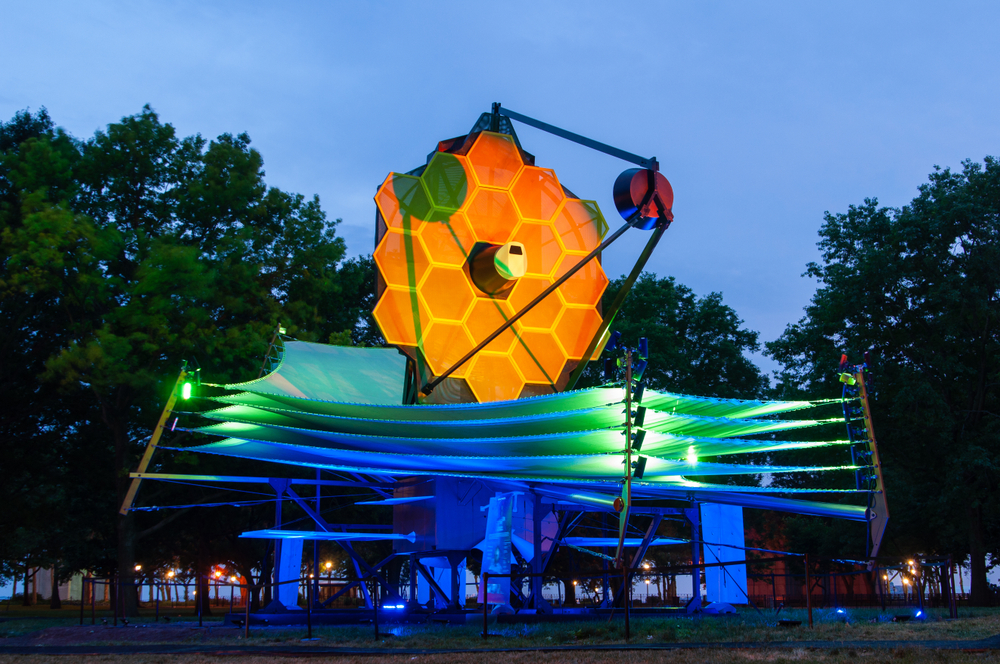
Image Credit: Shutterstock/Bobby Bradley
Some customers mount our profilometers into their computer-polishing systems to take in situ measurements of optics being polished, eliminating transport and positioning wastes. Some systems even come with a holster and backpack that holds a battery, so one can take measurements while walking around a shop floor, inside a submarine, at the top of a wind turbine tower, or on an aircraft wing,
What are some examples of dynamic interferometers being used at a wide variety of wavelengths?
UV interferometers are often used in measurements for the semiconductor industry, while visible metrology systems are often precisely matched to the optical system's wavelength being tested. 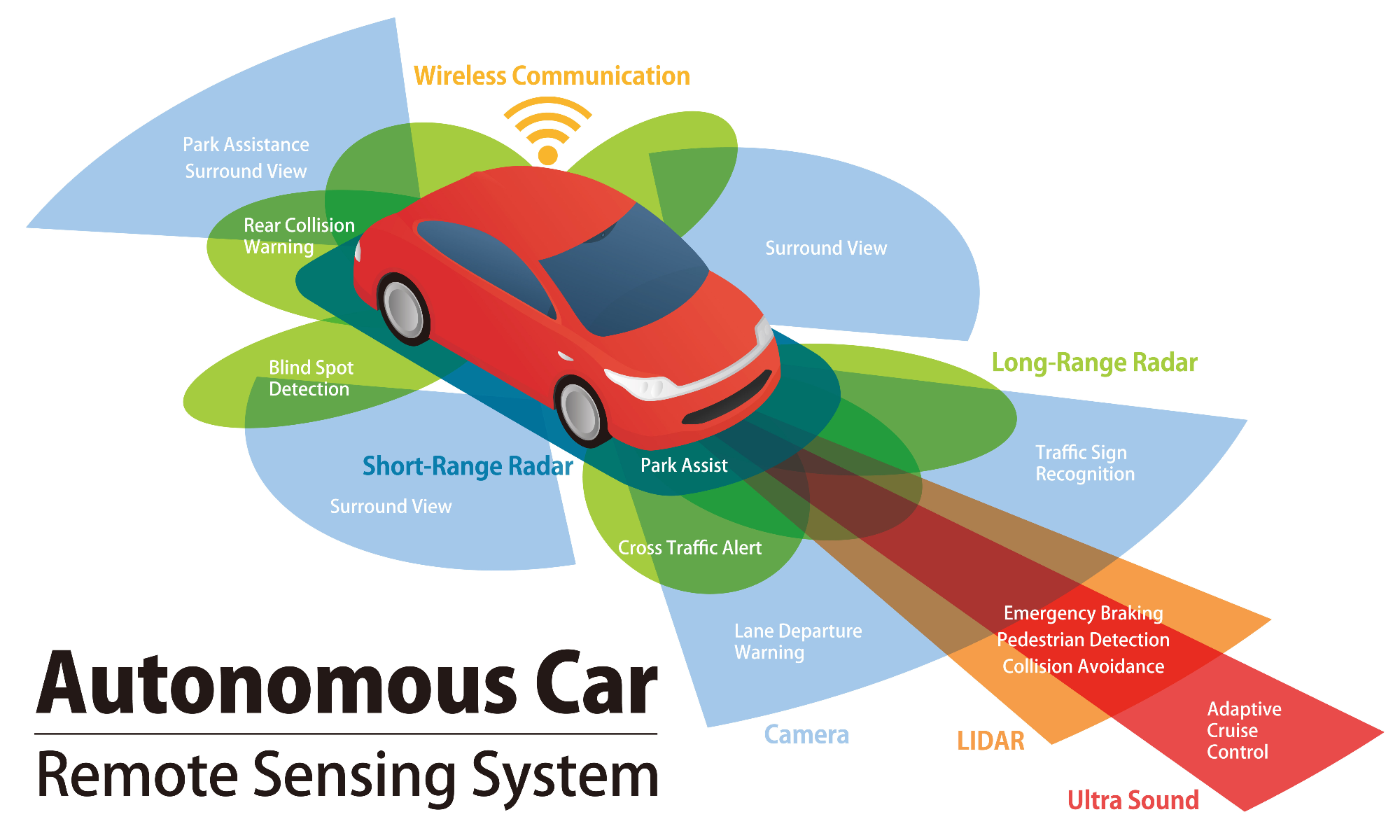
Image Credit: Shutterstock/metamorworks
Interferometers with infrared wavelengths are used for sensing applications, for everything from measuring optics for various military applications to the measurement of earth-observing systems or sensors for autonomous vehicles.
What role do pixel-level micro polarizer arrays bonded to scientific cameras play in terms of commercial dynamic interferometers?
The micro-polarizer arrays are what allows the necessary phase-shifted signals to be acquired simultaneously. Other configurations for dynamic interferometers are possible, but they are typically more expensive, larger, and less robust than using a polarizer array integrated into the camera used for the measurements. 4D Technology's patents on using micro-polarizers for dynamic interferometry have made us pioneers in the field.
In terms of 4D TechnologyTM and your products, can you tell us about some of the 4D dynamic interferometers you offer?
4D TechnologyTM offers AccuFiz® dynamic Fizeau interferometers for testing of traditional optics such as flats, lenses, mirrors, and prisms. Our PhaseCam® product line provides a highly compact Tywman-Green interferometer producing a diverging beam perfect for measuring large telescope optics and precision alignment of complex optical systems. Its high brightness and acquisition in millionths of a second make it essential for measuring large and remote telescope optical systems.
PhaseCam ESPI is used to measure the deformation of optical, structural supports, which are essential for aligning multi-mirror telescopes. We also offer a 3D-microscope interferometer for sub-nanometer roughness measurements of optics, semiconductors, and other precision surfaces. Last, we provide the 4D InSpec® product line, which are hand-held devices for measuring small-scale surface features such as chamfers, radii, pits, scratches, and nicks.
In addition to this, what sets your interferometers apart from others that are currently on the market?
4D TechnologyTM is an engineered solutions-provider and works closely with our customers to ensure not just that the hardware can take the necessary data but that it is analyzed and reported in a manner that can be readily used to improve their processes and achieve the quality products that are needed.
We also are very focused on the real-world evaluation of our products. We will do multi-person gauge studies to guarantee that results are consistent across different test pieces, operators, and environments.
About Dr. Erik Novak
Dr. Erik Novak has been Director of Business Development at 4D TechnologyTM since 2013, responsible for driving their products into new markets. 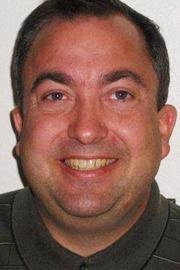
He has been developing instrumentation for precision metrology for more than 24 years in applications such as semiconductor, optics, aerospace, automotive, photovoltaics, and medical devices.
Erik has received seven international product awards, holds over a dozen patents, and has more than sixty publications and book chapters related to surface measurement and industrial process control
Disclaimer: The views expressed here are those of the interviewee and do not necessarily represent the views of AZoM.com Limited (T/A) AZoNetwork, the owner and operator of this website. This disclaimer forms part of the Terms and Conditions of use of this website.