The last few years have seen a distinct trend in electronics development, with packing density increasing all the time. Today, contemporary smartphones are far more powerful than they were just a few years ago, despite being no bigger. This same principle applies to IT devices, consumer electronics, and automobile electronics.
These advances mean that great care must be taken to recognize problems caused by heating. Modern infrared measurement technology is a useful tool in this regard.
In 1965 Gordon Moore hypothesized the rule that today is generally known as Moore‘s law - that the integration density of semiconductor devices would double every 18 months.
The power of semiconductors - in line with this rule - has provided the basis for the development of modern-day information technology and digitalization, which govern virtually every aspect of our daily lives.
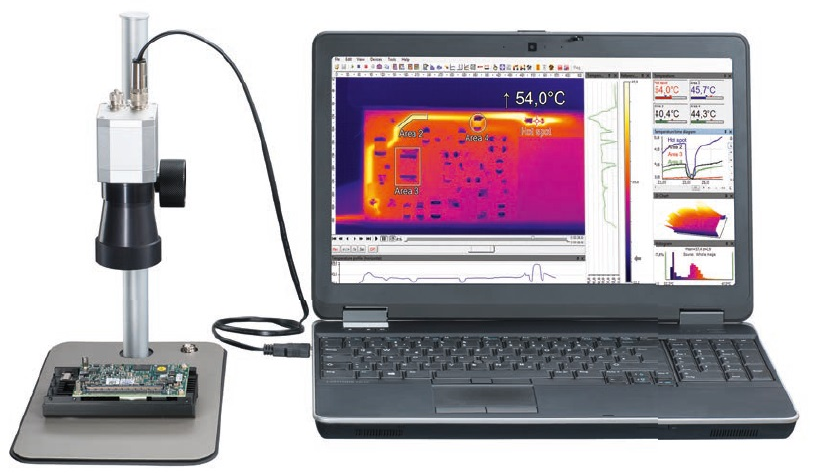
Measurement of hard disk electronics with microscope optics. The license-free software PIX Connect works as an analysis tool.
Power Loss Generates Heat
This constantly increasing integration density, however, means that the amount of heat resulting from power loss in components also continues to increase. Continual miniaturization is another factor that must be considered, as this can also adversely affect efficient heat dissipation.
Applications carrying comparatively large currents are also becoming more commonplace – for example in drive technology– thanks to the more widespread use of power electronics.
Semiconductor elements’ lifespans are hugely dependent on temperature, and even an increase in temperature of 10 °C can result in a 50% reduction in lifespan. Because of this, developers of electronic assemblies face the challenge of accommodating the thermal behavior of assemblies and circuit boards.
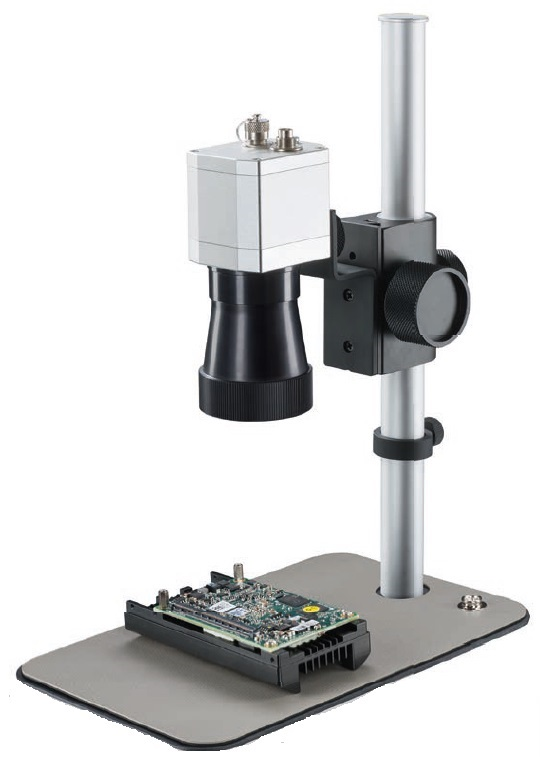
Infrared camera of the Precision Line with microscope optics.
Infrared technology can be employed to measure the temperatures of semiconductors, printed circuit boards, or whole assemblies. The measuring procedure is rapid, accurate, and non-contact – a particularly important consideration in electronics manufacturing. During measurements, regular checks should be made to ascertain exactly where a circuit board is showing specific temperatures.
Causes for excessive temperatures can be varied, including defective components, poorly soldered joints, or incorrectly dimensioned circuit paths. An infrared camera with an appropriately high resolution is able to properly record the temperatures of very small components and structures on a circuit board, allowing users to, for example, identify the exact component that is displaying excessive temperatures.
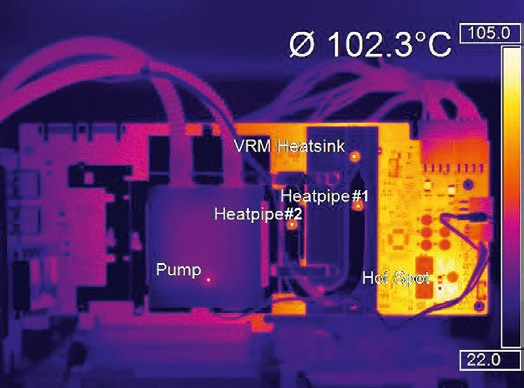
Thermal image of an operating motherboard. Image Credit: Igor Wallossek/tomshardware.de
Non-Contact Temperature Measurement Throughout Development, Production and Incoming Inspection
Infrared cameras are widely used in numerous stages of electronics development. Temperatures on printed circuit boards are often simulated in advance using thermal model calculations.
These model calculations can then be verified when measuring prototypes, and, should any discrepancies arise, the data gathered during measurement will be included in the simulations to further improve the models.
During the measurement of prototypes, components consuming excessive amounts of energy can then be identified. This process allows issues with circuit designs to be identified at an early stage, as well as spotting potential mutual interference of components on the circuit board.
Assemblies from external suppliers are often used during production. Infrared technology is also employed to undertake effective incoming quality control on these assemblies. These control measures can be carried out on every item, or selected items via random sampling.
Infrared cameras are also used in the final inspection of circuit boards or finished assemblies as part of the quality assurance process. This means that faulty assemblies or components can be efficiently identified during burn-in tests.
Choosing the Right Infrared Camera
High-quality infrared cameras are necessary to depict the minute structures present in electronic assemblies. Modern, powerful infrared cameras tend to utilize a matrix of miniaturized bolometers which have been housed on a chip. These microbolometer FPA detectors (Focal Plane Array) can be made up of more than 2 million pixels.
The bolometers themselves generally range from 12 µm x 12 µm to 35 µm x 35 µm in size and 0.15 µm in thickness. The bolometer’s resistance changes as it absorbs thermal radiation, and this enables the thermal image to be formed – with a temperature measurement value for every pixel.
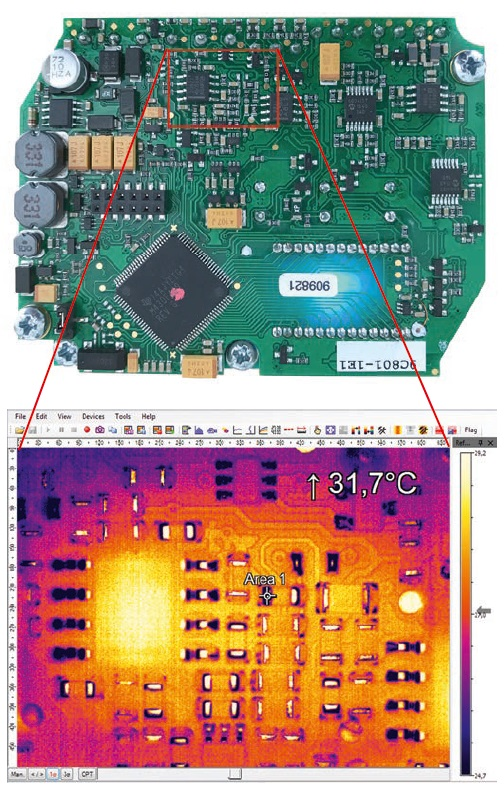
Microscope optics can be used to detect the smallest details. The temperature is measured in an area of 16 x 10 mm.
The more pixels an image sensor has, the higher the resolution it is capable of. However, individual bolometers become smaller as the number of pixels increases, so the thermal radiation emitted by each pixel is reduced.
Smaller pixels, therefore, need far higher detectivity to achieve the same temperature resolution. This places high demands on thermal isolation and temperature coefficients, as well as ensuring that the sensor surface is effectively utilized. In practice, however, a lower frame rate will be utilized to integrate image signals over a longer time period.
Generally, the frame rate, number of pixels and temperature resolution cannot be increased independently of one another.
Influence of the Lens and the Field of View
Like video or photo cameras, the image sensor (or its corresponding pixel count) is not solely responsible for ensuring high-quality images - the lens also plays a crucial role.
Infrared camera lenses commonly possess a high degree of luminosity, and in order to effectively use as much thermal radiation as possible whilst remaining free of atmospheric influences, work takes place in the spectral range of 8 µm to 14 µm.
To reliably identify the temperature of electronic components, the system’s measurement accuracy must also be provided for tiny objects. If this is not considered, a high resolution is not helpful with regard to the pure number of pixels.
As well as acquiring images of the smallest discernible structure, there is also an important consideration around the minimum size that an object needs to be in shot in order to reliably ascertain its temperature.
Should the resolution be limited to a low number of small pixels, smaller lenses that have a short focal length can be employed in visual fields of standard size. These tend to be more cost-effective but have the drawback of smaller apertures which let in less light. This, therefore, would need to be compensated by proportionally more sensitive sensors.
The thermal imaging camera’s visual field also depends on the selected lens, and this can range from 6° to 90°. The more distance between the camera and the object being observed, the larger the captured image region and, therefore, the image detail that each individual pixel can display.
The measuring device’s optical resolution must, therefore, be chosen depending on the size of the measurement object and the distance between this object and the sensor itself. Overall, a thermal imaging camera‘s sensor and lens must be appropriate for the measurement task in question, while also being suitable in terms of quality. This will ensure a thermal image that has both a good geometric and thermal resolution.
The PI 450 and PI 640 infrared cameras from Optris are well suited for the measurement of electronic assemblies. These instruments feature detector sizes of 382 x 288 pixels (PI 450) and 640 x 480 pixels (PI 640). Thanks to the exchangeable and highly focusable microscope lens (Figure 2) it is possible to easily capture the very small components or structures commonly found on a circuit board.
The smallest measurement spot diameter for the PI 450 is 42 µm in size and as small as 28 µm for the PI 640. Temperatures can be measured with an accuracy of ±2 °C. Additionally, due to the maximum possible frame rate of 125 Hz, even rapidly occurring processes can be made visible.
Both models of infrared cameras are capable of taking both static pictures and videos which can then be analyzed using the license-free analysis software.
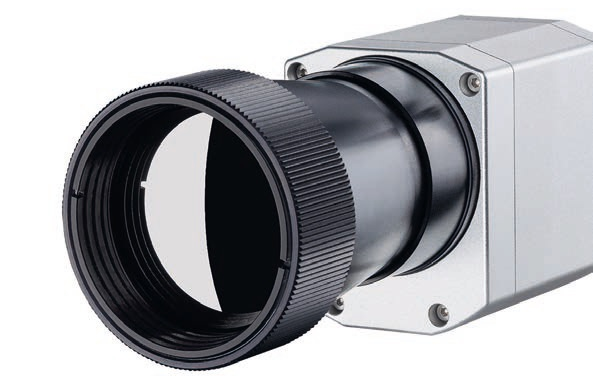
Temperature Control
Infrared cameras are a useful tool in the development, testing, and manufacture of electronic assemblies. Thanks to their high resolutions, temperatures, and temperature distributions of even the most miniaturized components can be easily measured, helping users to identify errors in the design process while reliably identifying faulty components. The end result of this process is faster, safer electronics development.
Acknowledgments
Produced from materials originally authored by Torsten Czech from Optris GmbH.
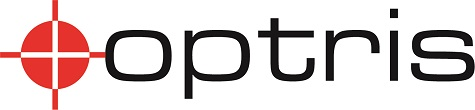
This information has been sourced, reviewed and adapted from materials provided by Optris GmbH.
For more information on this source, please visit Optris GmbH.