The challenging task of manufacturing aspheric optics, such as an Off-Axis Parabolic mirror or lens, can be contingent on the degree of asphericity of the optics as well as quality factors such as surface accuracy, surface quality, slope errors, and microroughness. The latter of which, microroughness, is an area of quality that must be mitigated for due to complex features that are even smaller than slope errors.
.jpg)
Effects of Scattering Due to Microroughness
Often these are expressed in RMS terms after integrating over spatial periods that are typically less than 0.25 mm. Thus, if such features are prominent they have the tendency to cause effects that may be compared to mild scattering. While these effects may not be critical for some applications, for others they can have grave consequences.
Consider high power laser applications, those that use mirrors or lenses as key focusing elements, or alternatively in imaging applications where the signal-to-noise ratio is extremely low, these scattering effects can play a crucial role. Therefore, microroughness levels need to be expertly controlled. Optical Surfaces Ltd. has discovered that microroughness can be controlled during the manufacturing process using a pitch-polishing technique, and although not yet fully understood, they have found that this procedure produces exceptional results that consistently remain below 1 nm RMS.
Microroughness Measurements
.jpg)
Graph 1. Microroughness distribution using pitch-polishing
Graph 1 illustrates a selection of microroughness measurements carried out on a number of optics manufactured in recent years by Optical Surfaces Ltd. The corresponding data shown in Graph 1 suggests that some of the higher values (i.e. those close to 1 nm RMS) may be related with optics that generate higher asphericity. Yet, the data sample is not large enough to confirm the latter argument in a definitive manner. Graph 2 exhibits the distribution of the results in a pie-chart format. While a standard surface map measurement obtained using While Light Interferometry (WLI) can be seen in Graph 3.
.jpg)
Graph 2. Microroughness percentile distribution for three selected ‘discrete’ regions.
.jpg)
Graph 3. Typical microroughness surface map obtained using WLI (White Light Interferometry)
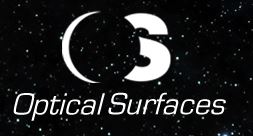
This information has been sourced, reviewed and adapted from materials provided by Optical Surfaces Ltd.
For more information on this source, please visit Optical Surfaces Ltd.