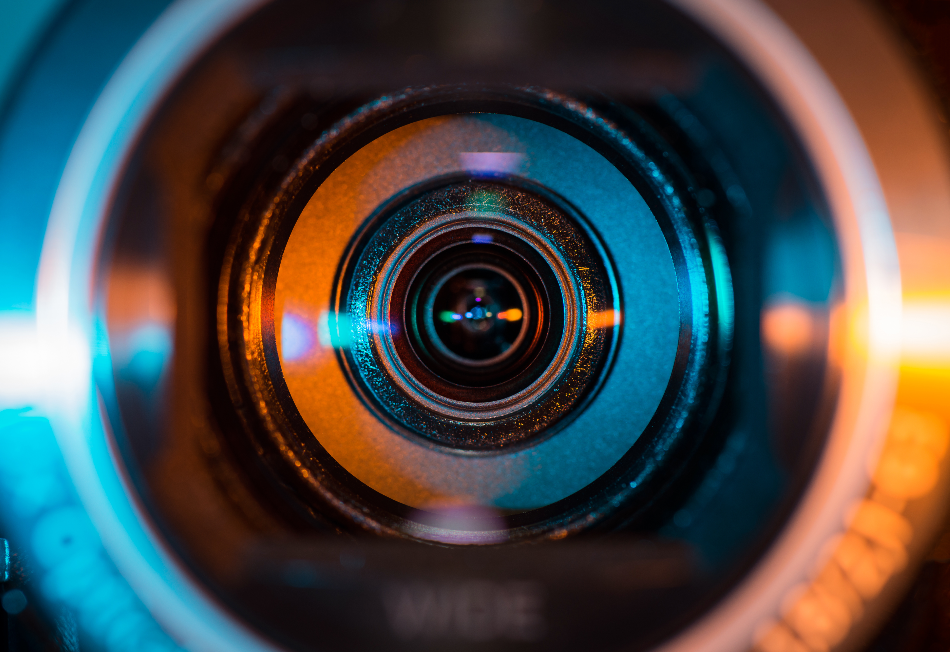
denniro / Shutterstock
Stereolithography (SLA), while not being the most popular method of 3D printing, is the oldest of the three types of technologies currently in use, having been developed in the 1980s by Chuck Hull, the founder of the company 3D systems. The company produced the first SLA printer in 1992 and with it the possibilities of rapid prototyping.
What is SLA Approach
The SLA approach uses a high powered ultraviolet laser to “draw” layers into a photosensitive resin bath. The area of resin that is targeted by the laser is hardened and the desired object is built layer by layer, as with all additive processes. The uncured resin is drained leaving the object to be cured in a UV oven to further harden and stabilize it.
SLA may have been the first 3D printing technology on the market but it is still regarded as the most precise, with the highest tolerance of currently available additive processes. Complex objects can be created to very fine tolerances, with smooth surfaces and a size of up to 50x50x60cm³ without compromising on quality. However, the process is slower and the objects tend to be more fragile than those produced by other technologies, due to the limitations of the resins used. So, perfect for high-resolution prototypes but less useful for functional parts, though this is changing as newer photopolymer resins are developed.
Specialist resins that can produce hard or flexible objects have been developed for the SLA that enable it to be used in niche areas such as medical devices, dental and jewelry casting, plus ceramics. It can also use transparent resins, so when developers and 3d printing enthusiasts began experimenting with ways to print optically transparent objects and eventually lenses, SLA seemed the obvious choice.
Challenge Facing Formlabs Engineers
Challenging themselves to produce a camera with an interchangeable lens produced entirely on their Form 2 SLA printer, Formlabs tasked one of their engineers to tackle the problem of producing an optical quality lens using one of their transparent resins. Aside from the limitations of the materials, lens design itself requires sophisticated software that can cost thousands of dollars. Formlabs kept things simple by using an open-source alternative that allowed the design of a single element lens. They also experimented with different orientations when printing the lens to minimize the artifacts that can occur within the printed material as part of the process.
SLA objects usually need a support structure integrated into the design of the object to stabilize it during printing, so a completed piece will nearly always need some post-print finishing to remove the superfluous printed material. The final printed lens would need significant finishing to polish the material to a point of optical clarity. This was achieved with rather low tech methods using a drill, sandpaper and eventually, they tried carefully hand sanding the lenses. Although the lens was smooth and clear, images through it were too blurred to be considered acceptable.
Application of 3D Printing to Solve the Challenge
However, they did what any self-respecting 3D printer company would do, they 3D printed a lens polishing machine. Still unhappy with the outcome, they noticed that dipping the lenses into resin post-printing and polishing, finally gave a surface smooth enough to try some sample photography. Given the results, their experiments with 3D printed lenses leave a lot to be desired. The lenses were not of a quality that could be used in spectrometers or optical sensors and though the resin lenses produced some artistic results, they would not satisfy the needs of a professional photographer.
Although plastic camera lenses are used in lower-end applications and in some cases there are plastic elements in high-end lenses, glass has always been the preferred material for use in optical devices.
It is possible to use a 3D printing process to produce glass objects. However, the two methods available, one using a deposition molding approach and the other using a glass filament melted with a laser, produce rough surfaces. In an article in Nature, “Three-dimensional printing of transparent fused silica glass”, Kotz et al described a method for producing high-quality glass components using a standard SLA printer. Using an SLA printable silica nano-composite that is heat-treated at temperatures of 1,300°C, silica glass of the highest quality is produced. The resulting glass has an exceptionally smooth surface and can be colored by the addition of alcoholic metal salts creating glass suitable for filters and a wide range of optical applications.
As the process utilizes a standard SLA printer, it brings the possibility of producing optical quality glass lenses to the benchtop and a much more acceptable solution than previous experiments with standard transparent photopolymer resins.
Sources
Disclaimer: The views expressed here are those of the author expressed in their private capacity and do not necessarily represent the views of AZoM.com Limited T/A AZoNetwork the owner and operator of this website. This disclaimer forms part of the Terms and conditions of use of this website.