Unwanted ambient vibrations that interfere with results produced from lab equipment, such as electron microscopes, can be prevented using active or passive isolator technology. Both types use different methods in achieving results, active technology electronically applies opposite forces that are the same strength and uses actuators and sensors to eliminate the unwanted vibrations.
This is different to passive methods, which remove of such vibrations by decreasing the probability of the interference being coupled to the object in question. This is implemented by using a mechanical bond that diverts and scatters the energy causing the interference prior to it reaching the object in question. In some cases, passive isolators are changed with the use of an electromechanical device, but the mode of vibration removal itself remains passive.
Elastomers, Coils, Negative-Stiffness and Liquid Components
Elastomers, coils, negative-stiffness and liquid components are used in passive technology and these types of isolators are usually cheaper than active mechanisms, as well as being more reliable and safe, as a result of to their simplistic design.
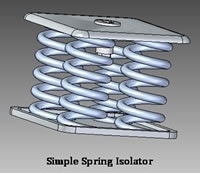
The diagram here shows the structure of a simplistic passive isolator design using a coil to separates surfaces, the vibration transmitting face and the object of interest. It functions by the coil lessening the impact of the vibrations by absorbing the energy as it changes in shape. The coil mechanism can also be muted by a fluid or elastomeric piece, similar to a shock absorber used in automobiles. In this example, mechanical energy from the shock (or vibration) is converted into thermal energy and transferred to the liquid component, minimizing the amount of energy converted to the rest of the automobile.
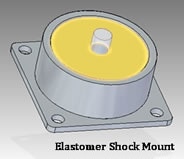
The diagram to the left shows an elastomer shock mount, which is made from a material similar to rubber and absorbs mechanical energy by changing in shape. Devices like this present in a wide variety of industries, and are used to lessen the impact and vibration by absorbing energy. Applications include factory equipment, car engines, construction and plane parts. The elimination of vibrations can be inconsistent depending on the direction of the vibration when using rubber, because of it’s differing directional characteristics.
Vibration Isolation Demo | Spacecraft Technology Expo Booth
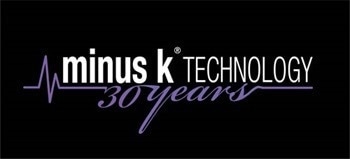
This information has been sourced, reviewed and adapted from materials provided by Minus K Technology.
For more information on this source, please visit Minus K Technology.