As there are several different types of laser (Figure 1), the need for many different profilers to oversee the range of lasers has increased. Currently, there are cameras and scanning slit profilers, which possess a number of options for different types of detectors. This article deals with questions that users need to ask to locate the right laser beam profiler for their laser and application.
.bmp)
Figure 1. Laser beam profilers
Wavelength
The laser’s wavelength establishes the kind of detector the beam profiler should possess. They are as follows:
- Si – Visible, NIR
- Pyroelectric – UV, IR, THz
- Ge, InGaAs – NIR
In comparison to pyroelectric and InGaAs varieties, Si and Ge sensors are less expensive.
Beam Size
In the case of large beams, users require a profiler with an adequately large aperture. However with small beams, many things need to be considered. If a camera is being used, the beam should be no less than 10 pixels wide to provide excellent accuracy. In the case of a scanning slit, the beam should have a minimum of four times the slit width, providing a minimum of approximately 8 µm. For both small and large laser beams, reducing/expanding optics enable the use of previously unsuited profilers.
Power
It is a fact that each beam profiler has a saturation level and a damage threshold. If the damage threshold is exceeded, damage may occur, while saturating the profiler may decrease measurement precision. Cameras possess a very low saturation level, which means that only the lowest power lasers would require some form of attenuation. The attenuation has a damage threshold, which would require users to have a combination of beam splitters, ND filters, and other optics to profile the beam properly.
Scanning slits often measure up to kilowatts of power minus the attenuation. This is because the spinning slit only allows the beam to hit the detector for a minimum amount of time, efficiently reducing the beam’s average power by that factor. For very high lasers, scanning slits will require some kind of attenuation.
Pulsed or CW
Cameras operate using both CW and pulsed lasers. Scanning slits function only if the laser is pulsing at a low rep rate. The entire operation works fine at higher rep rates.
The line between high and low rep rate is based on the size of the beam and the scan rotation speed. The reason behind this is a bit complex, however the outcome is fairly simple. Table 1 shows how fast a laser has to pulse to enable scanning slit use.
Table 1. Minimum beam size per pulse frequency
Minimum Beam Size per Pulse Frequency |
NanoScan |
Normal Drum |
Large Drum (HP) |
Rotation Rate (Hz) |
1.25 |
2.50 |
5.00 |
10.00 |
20 |
1 25 |
2.50 |
5.00 |
10.00 |
Slit speed (um/msec) |
116.63 |
233.25 |
466.50 |
933.01 |
1866.01 |
233.25 |
466.50 |
933.01 |
1866.01 |
Data Points per Profile |
15 |
15 |
15 |
15 |
15 |
15 |
15 |
15 |
15 |
Pulse Frequency (kHz) |
Minimum Beam diameter in µm |
Minimum beam diameter in µm |
1 |
1749 |
3499 |
6998 |
13995 |
27990 |
3499 |
6998 |
13995 |
27990 |
2 |
875 |
1749 |
3499 |
6998 |
13995 |
1749 |
3499 |
6998 |
13995 |
3 |
583 |
1166 |
2333 |
4665 |
9330 |
1166 |
2333 |
4665 |
9330 |
4 |
437 |
875 |
1749 |
3499 |
6998 |
875 |
1749 |
3499 |
6998 |
5 |
350 |
700 |
1400 |
2799 |
5598 |
700 |
1400 |
2799 |
5598 |
6 |
292 |
583 |
1166 |
2333 |
4665 |
583 |
1166 |
2333 |
4665 |
7 |
250 |
500 |
1000 |
1999 |
3999 |
500 |
1000 |
1999 |
3999 |
8 |
219 |
437 |
875 |
1749 |
3499 |
437 |
875 |
1749 |
3499 |
9 |
194 |
389 |
778 |
1555 |
3110 |
389 |
778 |
1555 |
3110 |
10 |
175 |
350 |
700 |
1400 |
2799 |
350 |
700 |
1400 |
2799 |
11 |
159 |
318 |
636 |
1272 |
2545 |
318 |
636 |
1272 |
2545 |
12 |
146 |
292 |
583 |
1166 |
2333 |
292 |
583 |
1166 |
2333 |
13 |
135 |
269 |
538 |
1077 |
2153 |
269 |
538 |
1077 |
2153 |
14 |
125 |
250 |
500 |
1000 |
1999 |
250 |
500 |
1000 |
1999 |
15 |
117 |
223 |
467 |
933 |
1866 |
233 |
467 |
933 |
1866 |
16 |
109 |
219 |
437 |
875 |
1749 |
219 |
437 |
875 |
1749 |
17 |
103 |
206 |
412 |
823 |
1646 |
206 |
412 |
823 |
1646 |
18 |
97 |
194 |
389 |
778 |
1555 |
194 |
389 |
778 |
1555 |
19 |
92 |
184 |
368 |
737 |
1473 |
184 |
368 |
737 |
1473 |
20 |
87 |
175 |
350 |
700 |
1400 |
175 |
350 |
700 |
1400 |
21 |
83 |
187 |
333 |
666 |
1333 |
167 |
333 |
666 |
1333 |
22 |
80 |
159 |
318 |
636 |
1272 |
159 |
318 |
636 |
1272 |
23 |
76 |
152 |
304 |
608 |
1217 |
152 |
304 |
608 |
1217 |
24 |
73 |
146 |
292 |
583 |
1166 |
146 |
292 |
583 |
1166 |
25 |
70 |
140 |
280 |
560 |
1120 |
140 |
280 |
560 |
1120 |
50 |
35 |
70 |
140 |
280 |
560 |
70 |
140 |
280 |
560 |
100 |
17 |
35 |
70 |
140 |
280 |
35 |
70 |
140 |
280 |
150 |
12 |
23 |
47 |
93 |
187 |
23 |
47 |
93 |
187 |
Conclusion
While there is no universal solution to fit everyone's specific needs, users must consider the above questions and discover which beam profiler is appropriate for their applications, or alternatively they can discuss this further with a sales engineer.
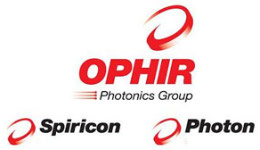
This information has been sourced, reviewed and adapted from materials provided by Ophir Optronics Group.
For more information on this source, please visit Ophir Photonics Group.