Solar cell manufacture is becoming a highly competitive field as high speed automation techniques tend towards zero defect tolerance. YAG lasers are being used for error-free scribing of solar panels. After laminating different photovoltaic material layers to glass, a sequence of channels is scribed by the laser. Each of these channels will act as a voltage-generating cell.
Careful monitoring and control of the shape, size, intensity and quality of the laser is crucial to ensure that the solar cell adheres to the cost requirements and specifications. The two most important variables that need to be observed and controlled are the laser beam energy or intensity, and its shape and size.
Laser Scribing Process
A laser beam without the required intensity level would be unable to ablate the photovoltaic material. Any leftover material causes a short circuit between subpanels, resulting in rejection or scrapping of the entire panel. The shape and size of the laser beam are also equally important in the scribing process. Only those beams with the exact shape and size can produce channels that have a uniform width.
Any discrepancies in the channel width can cause short circuits at the completion of the manufacturing process, again resulting in scrapping of the entire lot of solar cells. By controlling the shape and size of the laser beam, the total area of photovoltaic material can be maximized, which, in turn, delivers maximum wattage. Laser beams with intensity levels greater than the requirement will result in less electricity generating area, thereby reducing the efficiency of the panel.
Figure 1 shows an assembly in which a number of laser beams are used for scribing a coated glass panel simultaneously. There are two lasers shown in the figure, one on either side. The two beams are split into four directions, resulting in eight beams for scribing the panel placed below the laser optics assembly.
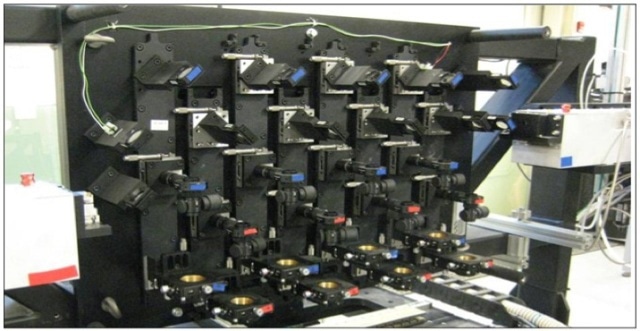
Figure 1. Solar cell scribing station; two lasers/eight laser beams
Measurement of the Laser Beam
The requirement in the above assembly was to set up eight uniform laser beams, implying that the energy per pulse for each beam was well within the permissible limit, and shape, size, and intensity were also within the specifications. At first, the eight laser beams were profiled using the Spiricon SP620U and the USB CCD beam profiler camera (4.4 um x 4.4 um pixels) 1600 x 1200. The versatility of this camera finds many applications, including the manufacture of solar cells. For performing this measurement and establishing the base lining, the Spiricon camera was placed below each of the eight focussing lens. Through this arrangement, each of the eight beams was imaged, quantified and displayed graphically.
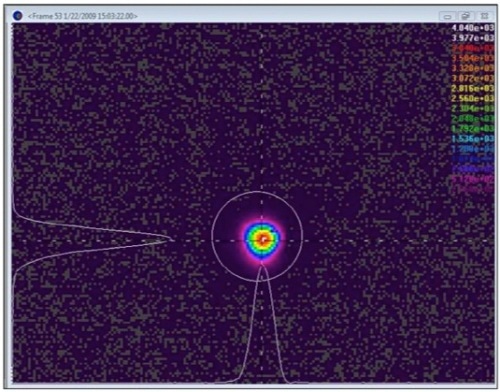
Figure 2. Solar cell, beam profile at focal point
This method allowed a laser beam size measurement to be established with a 1/e2 (13.5% of Peak), which was then used as a baseline for measurements in the future. This measurement is particularly useful for determining the quality of beam splitters, malfunction in transmission optics, and the deterioration of the supply laser in the long term.
The second set of measurements of the eight laser beams was aimed at understanding the energy per pulse value of each beam. Along with the USB SP620U profile camera, an Ophir PE10 pyroelectric energy sensor (2 µJ to 10 mJ) was placed under each of the eight beams, and the quantitative measurements were recorded. One measurement helped to corroborate whether the energy per pulse was within the specification, and another ensured that each of the eight beams was within tolerance to one another.
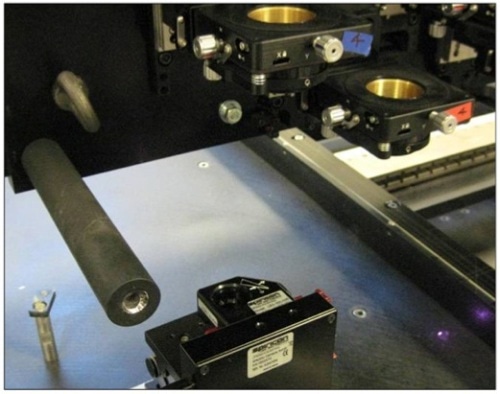
Figure 3. Beam Profiling 1st of eight laser beams – located at the focal point (SP620 Camera with LBS300)
While using energy sensors for measurements, a drop in measurement occurs due to laser failure. There will be a dip in energy measurement if beam splitting wedges crack or become coated with residue, or if the focussing lens gets coated with dust. Even changes caused by a slight power supply failure inside any one of the lasers are detected by these measurements.
This two-set method needs to be performed at the start of each process until manufacturers gain confidence on the reliability of these settings. Once this is achieved, the measurement frequency will likely be reduced to twice or once a week.
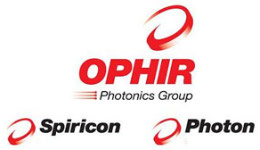
This information has been sourced, reviewed and adapted from materials provided by Ophir Photonics Group.
For more information on this source, please visit Ophir Photonics Group.