Sponsored by CavitarReviewed by Louis CastelDec 13 2022
High-power laser illumination has several unique features that facilitate the acquisition of critical measurements across various industrial and scientific applications. It is the perfect light source for high-speed cameras as well as for machine vision cameras.
Laser lighting allows for the visualization of applications that otherwise can be impossible to capture with traditional light sources such as LED or halogen lamps. Diode laser illumination has particular characteristics that make it well-suited for the visualization of various applications.
Firstly, the light is extremely monochromatic, which allows for the elimination of thermal radiation or chromatic aberrations. Secondly, laser illumination can produce high-power pulses of short duration, which facilitates the precise visualization of small and fast objects at greater resolutions without generating motion blur.
Therefore, eradicating motion blur is still possible regardless of the camera shutter, as the exposure is set in relation to the laser pulse duration. Moreover, laser light can be fiber-coupled which can be extremely useful in certain scenarios, for instance where space is limited.
All of these properties make diode lasers excellent light sources across various demanding processes such as welding, combustion, explosions, ballistics, flow and shockwave studies.
It is possible control diode lasers with high levels of precision. This facilitates the generation of short pulses which are crucial for eliminating motion blur.
Motion blur occurs when the object is moving too fast for the camera shutter. Therefore, combining short pulses with high output-power ensures that diode lasers are ideal light sources in ballistics, flows, and shockwave studies.
The remainder of this article will seek to outline the various applications of high-power laser illumination.
The Ability to See Through Heat
When it comes to imaging bright processes such as welding, combustion, or explosions, the camera sensor can easily become completely saturated due to a large amount of process light. Moreover, there are different ways to eliminate process light in order to make details visible.
The first step towards the reduction of process light is filtering - neutral density or narrow band filters can be used to accommodate this. Neutral density filters are able to reduce brightness evenly over a broad spectral band. Therefore they produce darker images but do not influence the relative brightness of objects in the images.
This means that the brightest object in the image will be the brightest visible. As an example, in arc welding, it is possible to reduce the brightness of the arc with the application of neutral density filters, but at the same time, the entire image would become very dark. Conversely, narrow band filters only allow a very narrow range of wavelengths to pass through to the camera. If the proper filter is selected, a considerable portion of process light can be eliminated.
By actively illuminating the object using narrow band light matching with the transmission band of the filter, the object can be illuminated in a controlled manner while simultaneously eliminating thermal light.
Another key element in the imaging of bright processes is the camera exposure time. The longer the camera allows light to pass through, the brighter the image. Therefore short camera exposure time is preferred when imaging bright objects.
As laser illumination can produce enough power to illuminate the object with an extremely short pulse, laser illumination allows for the use of short camera exposure time.
Moreover, due to the high brightness of laser illumination, the light can be focused on the desirable area efficiently, thus highlighting the advantages of laser illumination when compared to traditional light sources.
With active pulsed laser illumination, short camera exposure time, and optimized narrow band filtering, it is possible to realize the optimal image quality for light emitting and bright processes. This technique is well-suited for use in high-speed cameras as well as in machine vision cameras.
The image below displays the effects of no filtering (left), filtering without laser illumination (middle), and filtering with laser illumination (right):
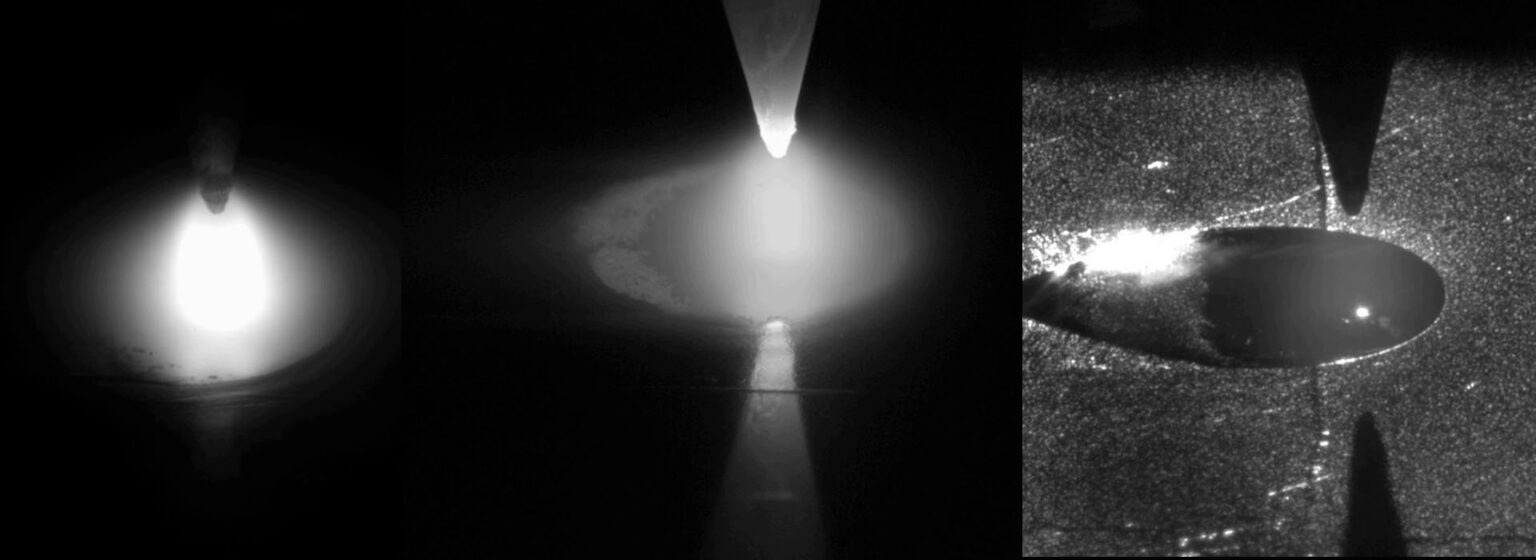
Figure 1. TIG welding process imaged at 1.000 fps. (Images courtesy of Nobby Tech, Japan)
Freeze the Motion
Various industrial and scientific processes involve the use of small and fast-moving objects. As the velocity of the object increases, there will be a concurrent increase in the amount of motion blur for fixed camera exposure time and optical magnification. Motion blur leads to a reduction in the amount of information in the images.
To effectively address this challenge, several cameras can produce very short exposure times at the micro-second level. However, with shorter exposure times comes a greater demand for illumination. For example, if the camera exposure time is 1 µs, the illumination that is sufficient for illuminating the object in the correct manner has to be generated during that exposure time.
In several cases, even the micro-second-level exposure time may be insufficient. Examples of such processes include shockwaves, small-scale explosions or microscopic imaging of fast-moving webs.
It is possible to solve this deficiency by utilizing a pulsed light source that can send pulses that are shorter than the camera exposure time and still incorporate appropriate amounts of light to properly illuminate the object.
Diode laser illumination is perfect for this purpose as the pulses can be created easily by digital inputs allowing for extremely short pulses at the nanosecond level. The laser output power needs to be high to achieve sufficient brightness with such short pulses.
The image below displays the difference between a CW (continuous wave) light source (left) and laser illumination with extremely short pulses (right). The camera exposure time is short in each of the images. Laser illumination limits levels of motion blur and offers more information in contrast to the CW light source.
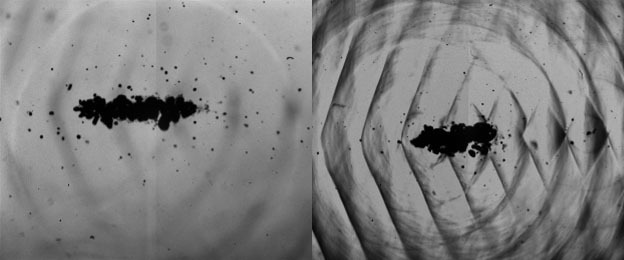
Figure 2. Shockwave in gel created with sonosensitizer imaged at 500.000 fps. (Images courtesy of Prof. Umemura and Prof. Yoshizawa from Tohoku University, Japan)
Focused Light Without Heat
A number of traditional light sources produce significant amounts of heat, which warms the surrounding environment and the object under investigation. Moreover, such light sources cannot be focused easily on the target. Therefore a considerable part of the illumination is not used as it does not fall into the specified region of interest.
The light from diode lasers can be fiber-coupled relatively easily and also focused with a variety of optics. This allows access to limited spaces, which is not usually possible for other light sources. Furthermore, the heat generated by diode laser illumination is minimized due to the ability to only generate light when the camera is exposing.
Diode laser illumination is, therefore, an excellent solution for heat-sensitive targets like paper webs and explosive environments such as liquid tanks in the chemical process industry.
The image below demonstrates the surface of a paper web. The paper web’s rapid speed and the high-resolution demand high-power illumination with short pulses. Since paper is a flammable material, it is crucial to note that the light source does not heat up the object.
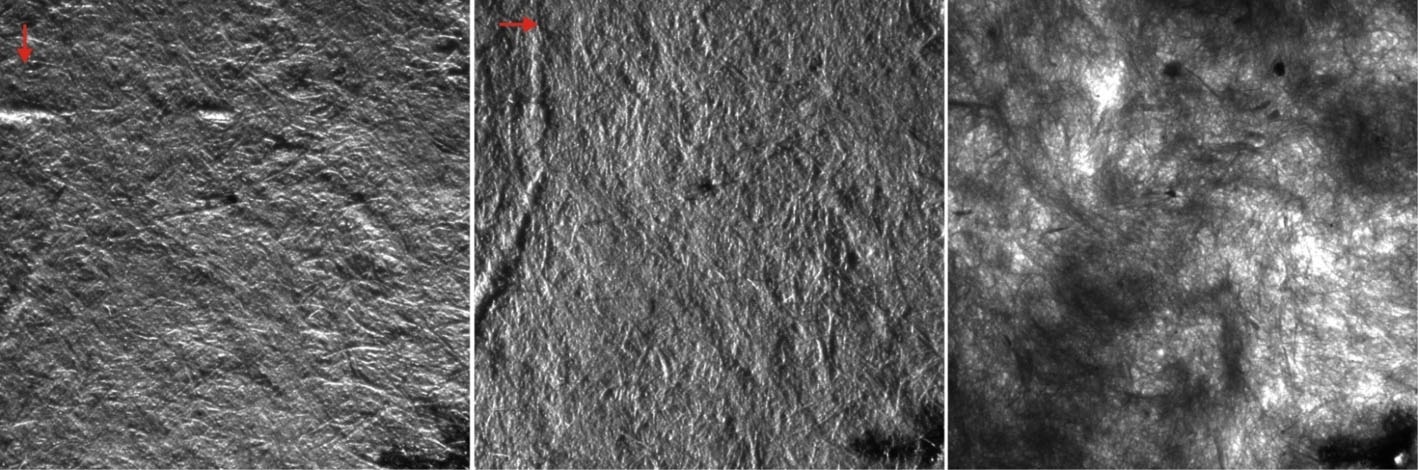
Figure 3. Surface topography of paper web imaged at 20 fps. Image Credit: Cavitar
Intelligent Light
With diode lasers, users can create varying illumination shapes that can then be employed to meet the demands of different applications.
A round uniform spot is utilized in most front illumination applications. The spot covers the area of interest, and the spot size can be adjusted with ease. In several cases, the area of interest can be reduced in height and increased in width.
With the right optics, the laser light can be transformed, for instance, to an elongated ellipse to focus specifically on the area of interest.
It is also possible to generate light sheets that are typically applied in PIV (Particle Image Velocimetry) imaging. While diode lasers do not offer the same high intensity as conventional PIV lasers, they can still be applied in some micro-PIV applications.
Diode laser illumination is also appropriate for use in Schlieren and Shadowgraph applications. With multi-output light guides, unwanted reflections that come from shiny objects can be reduced.
Lasers also have the ability to produce various illumination patterns with active or passive lines. For example, in the image below, a pattern of shadow lines is displayed. It can be applied for triangulation measurements, while the illuminated part of the image can show the surface properties.
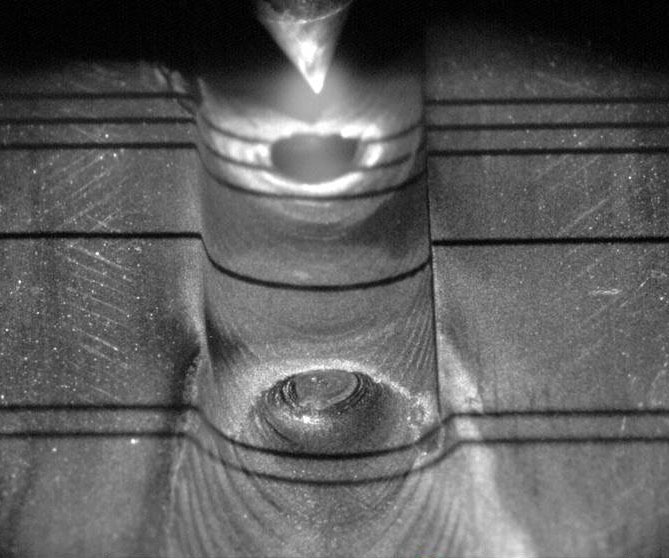
Figure 4. TIG welding process illuminated with structured light at a frame rate of 20 Hz. (Image courtesy of at Hollming Works Oy, Finland).
High-power diode laser illumination facilitates a number of new applications in machine vision where conventional light sources cannot meet the expected requirements.
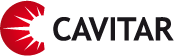
This information has been sourced, reviewed and adapted from materials provided by Cavitar.
For more information on this source, please visit Cavitar.