Interview conducted by Maria OsipovaApr 15 2022
In this Interview AZoOptics talks to Christine Desplat an Application Engineer at Master Bond Inc about the application of optical devices and properties that should be considered in the adhesive selection process.
Does an optical device always require an optically clear adhesive?
Adhesives can vary in color from transparent to opaque. For optical devices, the tendency is to think that you always need optical clarity, but this is not necessarily the case. There is no hard and fast rule for color in many optical applications, and the requirements can vary from case to case.
Some applications require a transparent product with high light transmission, whereas some optical assemblies require an opaque adhesive with light-blocking properties. In many optical devices, the adhesive may not even be in the optical path, so the color is not an important consideration in such cases.
What are some of the considerations when deciding on an adhesive for an application that requires optical clarity?
With the rapid advancement of technology in the optics industry, the adhesive selection process has become increasingly complex, considering the number of factors involved. Epoxies, silicones and UV/dual curing chemistries are frequently used for bonding, sealing, coating and encapsulating applications across optical, optoelectronic, fiber-optic and related industries.
Some of the important considerations in applications requiring optical clarity are the refractive index of the adhesive, as well as its transmission at different wavelengths, ranging from UV to far IR, such as 200 nm to 2500 nm or beyond. There is also a need to match the refractive indices of the substrates in many applications. The typical refractive index ranges for such compounds range from 1.40 to 1.60 at around 589 nm.
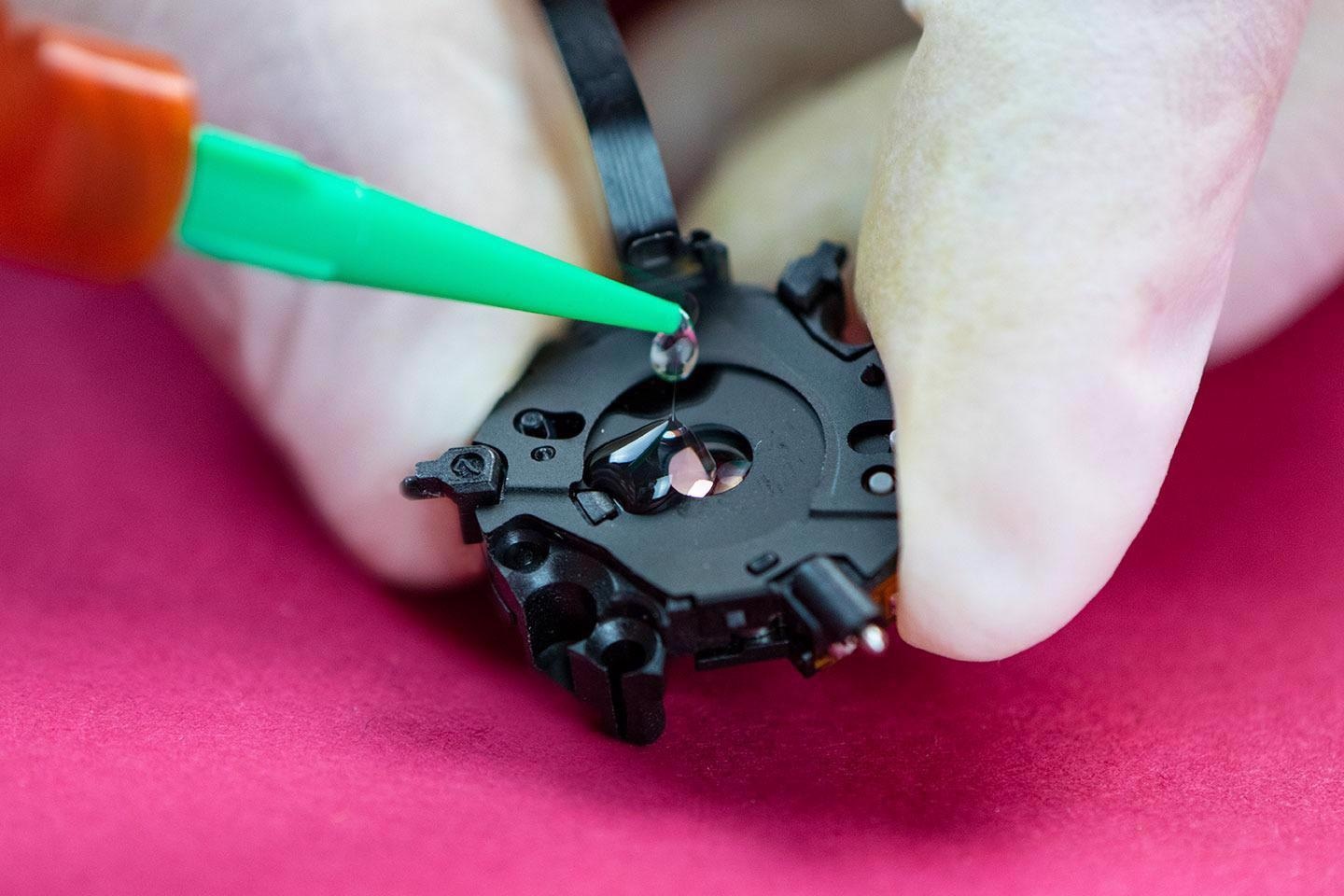
Image Credit: MasterBond
Besides color, what other properties should be considered in the adhesive selection process?
Other than color, some of the factors in the adhesive selection process are temperature resistance, mechanical strength, chemical resistance and modulus or hardness. These would be some of the cured properties that a design engineer may focus on. Handling and processing parameters such as mix ratios, viscosity, working life and cure time also play a vital role in the adhesive selection process.
The specifics of the application also need to be examined, including the geometry of the parts and their dimensions. For example, in a fiber in a ferrule type application, the compound should be very thin or have an ultra-low viscosity, such that it can wick into very narrow gaps. In other situations, such as for mounting optics on various substrates or sealing, a more moderate viscosity or even a paste is desirable.
Ultimately, the choice depends upon a whole host of different factors, including dimensions, the nature of the application, how the material will be applied and what properties are required after cure.
What are some of the other cured properties, which should be considered?
The coefficient of thermal expansion, outgassing, shrinkage, stiffness and dimensional stability are important considerations in an optical device. After polymerization, salient issues for epoxies might include a low coefficient of thermal expansion, excellent dimensional stability, high modulus and low shrinkage upon cure. Some silicone compounds offer excellent stress relief with their very low modulus of elasticity and low shore hardness levels after cure.
Finally, UV or dual curing chemistries offer ultra-fast fixturing and the ability to provide really fast alignments in certain bonding situations. Low outgassing is another important property in optical applications. This feature is highly desirable in numerous applications involving lenses, semiconductors, optical components and vacuum applications.
Many epoxies pass the NASA low outgassing test based on ASTM E-595, which is tested under vacuum conditions. Specialty silicones and UV curable products also pass this stringent test. Finally, in optical devices, reliability is also critical and many compounds have been specially formulated to withstand aggressive 85 C/85 % Relative Humidity environments.
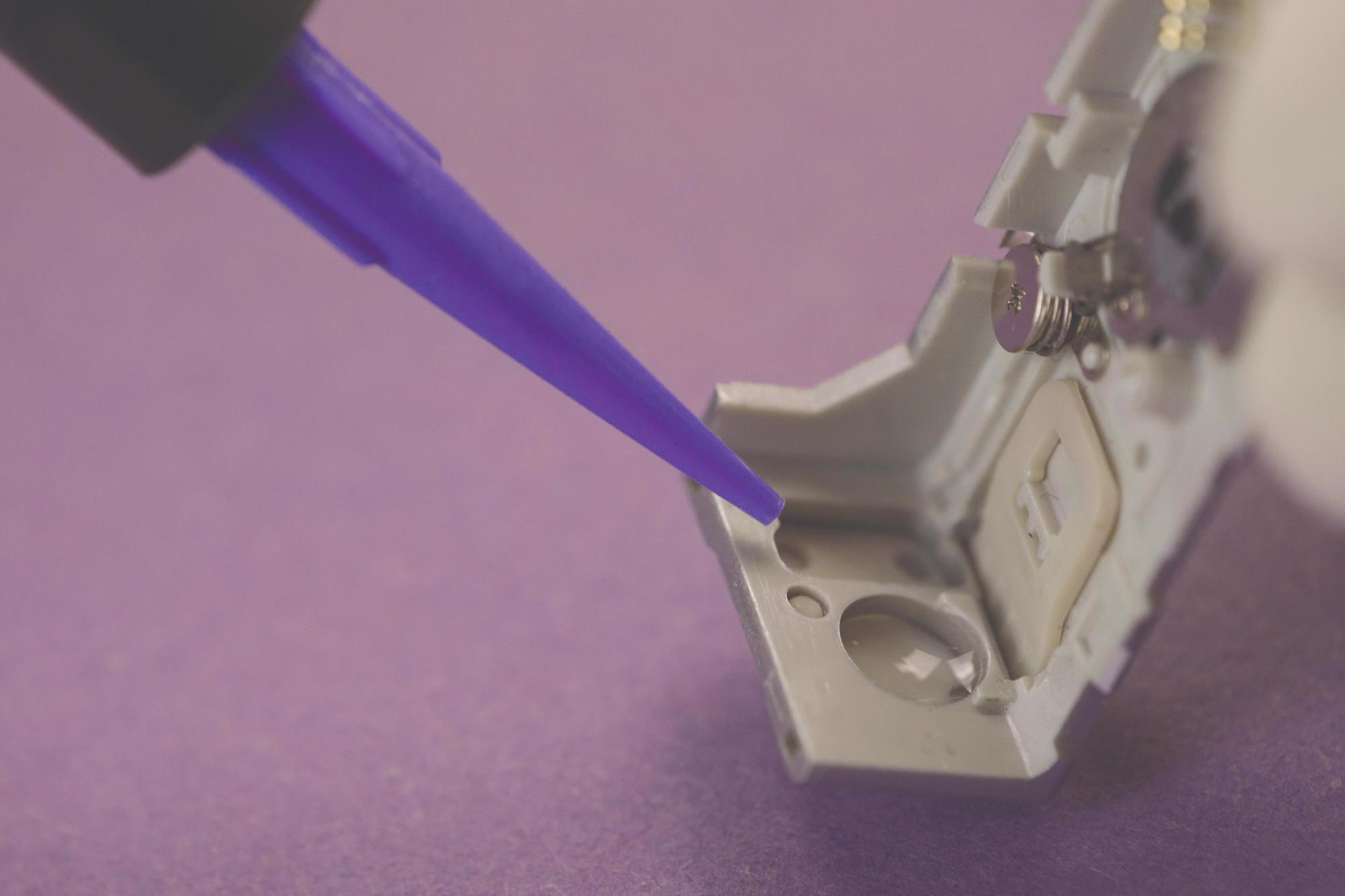
Image Credit: MasterBond
What Master Bond compounds might be recommended for optical applications?
We have a wide range of products that support optical applications. Here are a few with different properties and chemistries.
Master Sil 151 is a two-component, highly flexible silicone with superb optical clarity and a refractive index of around 1.405. It offers very low stress and is suitable for use in various potting, sealing and bonding applications involving substrates with different coefficients of thermal expansions.
UV22DC80-1Med is a nano-silica filled, UV + heat (dual) curable, USP Class VI and ISO10993-5 certified biocompatible and non-cytotoxic adhesive that features excellent optical clarity, and dimensional stability. It cures upon exposure to a UV light source emitting at a wavelength of 320 to 365 nm with an energy output as low as 20-40 milliwatts/cm2. Shadowed out areas can be post-cured at 80 °C for around 1 hour.
EP42HT-2LTE is a two-part, opaque epoxy, which offers the lowest coefficient of thermal expansion of 9 to 12 ppm/C at room temperature, among Master Bond products. It has a paste consistency and is used widely in situations requiring low outgassing, superior dimensional stability, as well as precise alignment in the bond joint.
EP30-2 is a two-part, clear, low outgassing epoxy that was qualified for use in critical Laser Interferometer Gravitational-Wave Observatory (LIGO) bonding applications. The main applications involved bonding prism elements and acoustical dampeners to optical components.
EP4CL-80 is a one-component, 80 °C curable, exceptionally low viscosity epoxy for bonding, coating and sealing. It is clear in color and is a reliable electrical and thermal insulator.
About Christine Desplat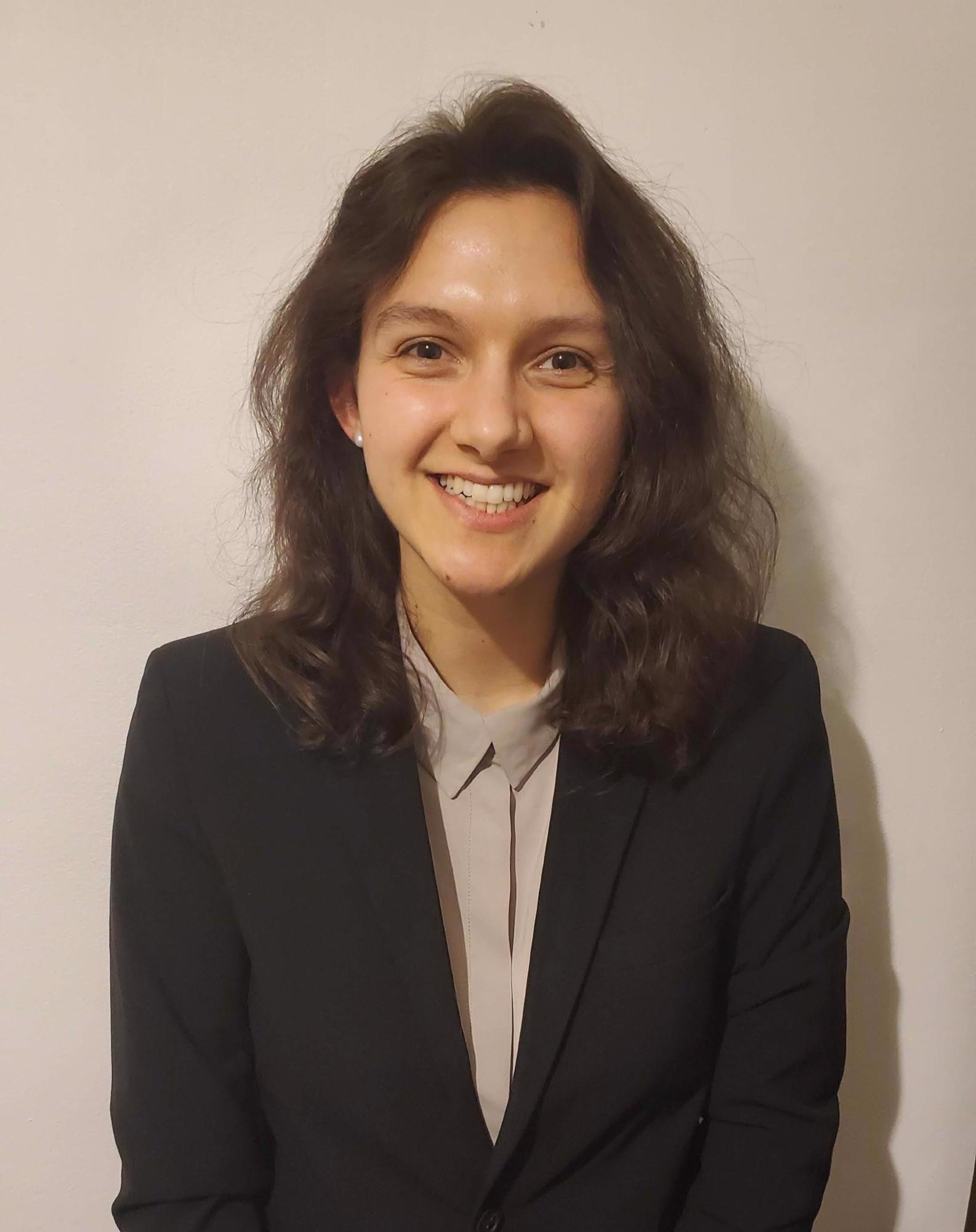
Christine Desplat is an Application Engineer at Master Bond Inc. She analyzes application oriented issues and provides product solutions for companies in the aerospace, electronics, medical, optical, and oil/chemical industries. She received a Bachelor's Degree in Chemical Engineering from Rensselaer Polytechnic Institute.
About Master Bond Inc
Master Bond is a leading manufacturer of high-performance adhesives, sealants, coatings, potting and encapsulation compounds and impregnation resins.
Master Bond custom formulates products with specific performance properties designed for unique applications. These compounds exhibit the advanced properties required for a number of different industries, including aerospace, medical, optical, electrical, electronics, OEM and other manufacturing industries.
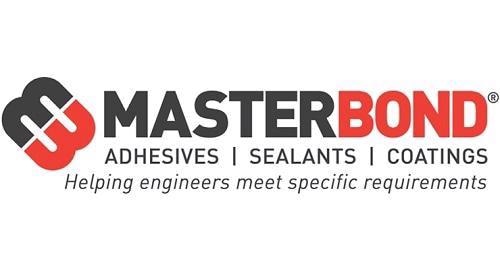
This information has been sourced, reviewed and adapted from materials provided by Master Bond Inc.
For more information on this source, please visit Master Bond Inc.
Disclaimer: The views expressed here are those of the interviewee and do not necessarily represent the views of AZoM.com Limited (T/A) AZoNetwork, the owner and operator of this website. This disclaimer forms part of the Terms and Conditions of use of this website.